Introduction
In the ever-evolving world of industrial filtration, the brush self-cleaning filter stands out as a reliable and efficient solution for maintaining clean fluids across various sectors. These filters are designed to automatically remove contaminants from water and other liquids, ensuring uninterrupted operation and reducing maintenance costs. In this article, we will delve into the intricacies of brush self-cleaning filters, exploring their working principles, components, technical specifications, and diverse applications.
Working Principle
The brush self-cleaning filter operates on a straightforward yet effective principle. It utilizes a rotating brush mechanism to clean the filter screen without interrupting the filtration process. Here’s a step-by-step breakdown of its working principle:
Filtration Process: The liquid enters the filter through the inlet and flows through the filter screen. As the liquid passes through the screen, contaminants are trapped on the surface, allowing clean fluid to exit through the outlet.
Accumulation of Contaminants: Over time, contaminants accumulate on the filter screen, leading to increased differential pressure.
Automatic Cleaning Initiation: When the differential pressure reaches a pre-set value, the self-cleaning cycle is triggered automatically. This can also be initiated manually or based on a timer.
Brush Cleaning Mechanism: The motor-driven brush rotates along the inner surface of the filter screen, dislodging the trapped contaminants.
Removal of Debris: The dislodged contaminants are collected in a sludge chamber and are periodically expelled through a drain valve, ensuring continuous filtration.

Components
Brush self-cleaning filters are composed of several key components that work in harmony to ensure efficient filtration:
Filter Housing: The robust structure that houses all internal components. It is typically made of stainless steel or other corrosion-resistant materials to withstand harsh operating conditions.
Filter Screen: The core component responsible for trapping contaminants. Screens are available in various mesh sizes to suit different filtration requirements.
Brush Assembly: Consists of motor-driven brushes that rotate and clean the filter screen. The brushes are designed to effectively dislodge particles without damaging the screen.
Motor and Gearbox: Powers the brush assembly and ensures smooth and consistent rotation.
Control System: Manages the self-cleaning cycle, monitoring differential pressure and initiating the cleaning process as needed.
Sludge Chamber and Drain Valve: Collects and expels dislodged contaminants, maintaining filter efficiency.
Technical Specifications
Brush self-cleaning filters come with a range of technical specifications tailored to meet diverse industrial needs. Here are some common parameters:
Flow Rate: Typically ranges from 10 to 10,000 cubic meters per hour, depending on the filter size and application.
Filtration Degree: Available in various mesh sizes, usually from 50 to 3,000 microns, to cater to different levels of filtration precision.
Operating Pressure: Designed to operate within a pressure range of 0.1 to 10 bar, ensuring compatibility with various systems.
Temperature Range: Can handle a wide range of temperatures, from -30°C to 150°C, making them suitable for diverse environments.
Material of Construction: Commonly constructed from stainless steel (304, 316) or carbon steel, with options for special coatings to enhance durability.
Power Supply: Typically requires a standard electrical supply, such as 220V or 380V, to operate the motor and control system.
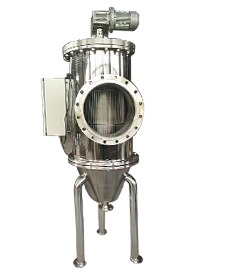
Applications
Brush self-cleaning filters are versatile and find applications in numerous industries, including:
Water Treatment: Used in municipal and industrial water treatment plants to remove suspended solids and ensure clean water supply.
Agriculture: Essential for irrigation systems, protecting spray nozzles and drip lines from clogging.
Food and Beverage: Ensures the purity of process water and other liquids, maintaining product quality and safety.
Oil and Gas: Protects equipment and processes by removing contaminants from cooling water, injection water, and other fluids.
Chemical Processing: Maintains the integrity of chemical processes by filtering out impurities from process fluids.
Power Generation: Used in cooling systems to prevent fouling and maintain efficient heat exchange.
Pulp and Paper: Ensures the cleanliness of process water, reducing downtime and maintenance costs.
Mining: Filters out particulates from process water, enhancing the efficiency of mining operations.
Conclusion
Brush self-cleaning filters represent a significant advancement in the field of industrial filtration. Their ability to automatically clean the filter screen without interrupting the filtration process makes them an invaluable asset across various industries. By understanding their working principles, components, technical specifications, and applications, businesses can make informed decisions about integrating these.
Other Related Products:
High Flow Cartridge Filter
Basket filter
High flow filter element
{sval:sql sql='SELECT n_parameter FROM dede_addonarticle WHERE aid = ~aid~ ' } {/sval:sql}
{sval:sql sql='SELECT n_parameter FROM dede_addonarticle WHERE aid = ~aid~ ' } {/sval:sql}