Introduction
Backwash filters are essential components in numerous industrial and commercial applications, ensuring the continuous removal of contaminants from water and other fluids. These filters are designed to provide efficient, automated cleaning without interrupting the filtration process. This article delves into the introduction, working principle, components, technical specifications, and application fields of backwash filters.
Product Introduction
Backwash filters are advanced filtration systems that use a backwashing mechanism to clean the filter media. This process involves reversing the flow of fluid to dislodge and remove trapped contaminants. Backwash filters are commonly used in water treatment, petrochemicals, pharmaceuticals, food and beverage, and power generation industries. They are designed to handle high flow rates and maintain optimal filtration efficiency with minimal manual intervention.
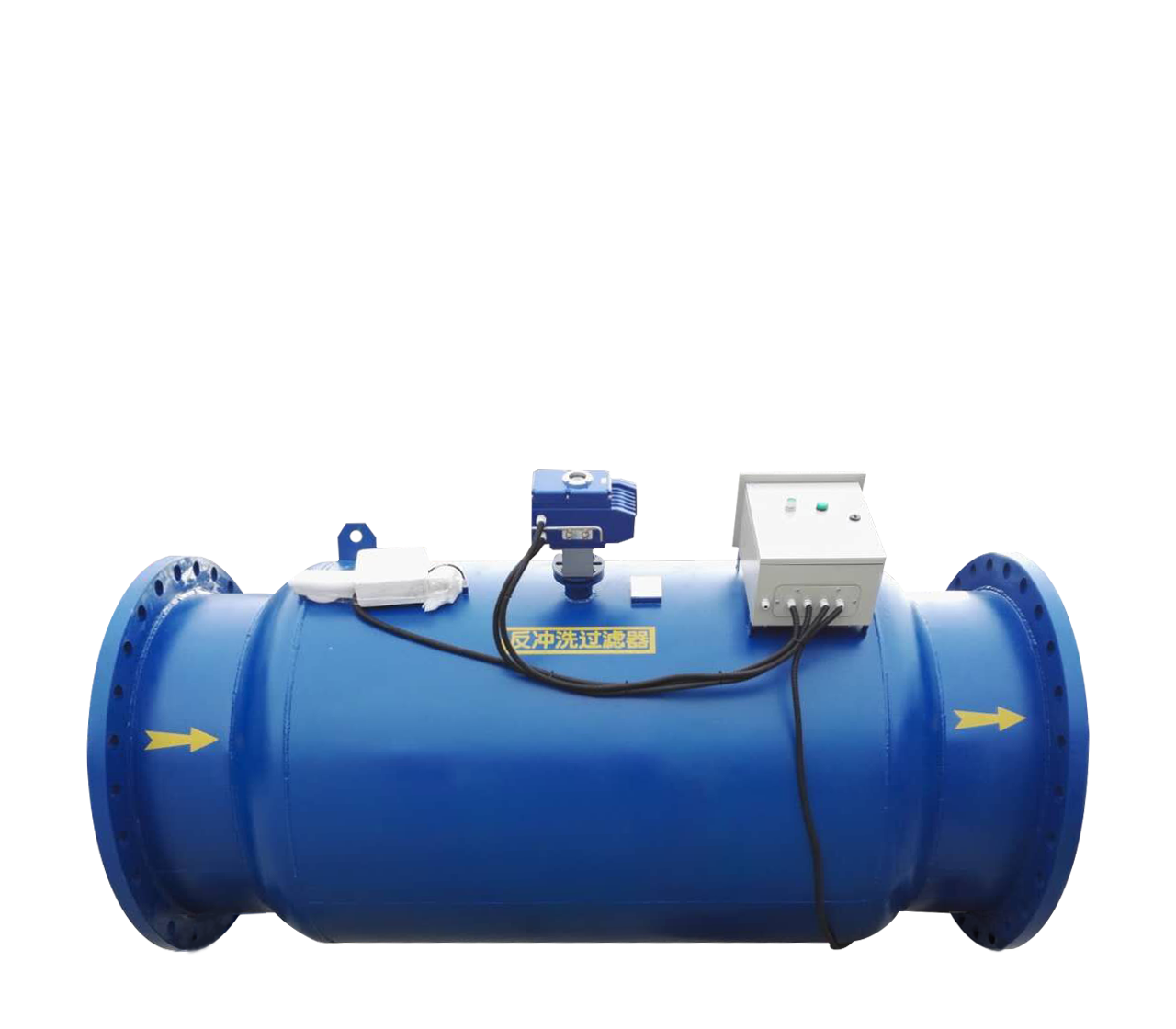
Working Principle
The working principle of a backwash filter involves several key stages:
Filtration: Fluid enters the filter housing through the inlet and passes through the filter media. Contaminants are trapped on the surface or within the filter media, allowing clean fluid to flow through and exit via the outlet.
Accumulation: As filtration continues, contaminants accumulate in the filter media, creating a layer of debris that can reduce filtration efficiency and increase pressure drop.
Backwash Activation: When the differential pressure across the filter media reaches a predetermined threshold, the backwash cycle is initiated. This can be triggered automatically by the control system based on time intervals or pressure sensors.
Backwashing: During the backwash cycle, the flow of fluid is reversed. Clean fluid or air is forced through the filter media in the opposite direction, dislodging and flushing out the accumulated debris.
Debris Expulsion: The dislodged contaminants are collected and expelled through a drain or waste outlet. Once the backwash cycle is complete, the filter returns to normal operation, continuing to provide clean fluid.
Product Components
Backwash filters are composed of several key components that ensure efficient filtration and automated cleaning:
Filter Housing: The filter housing is a durable casing that encloses all internal components. It is typically made from materials such as stainless steel or carbon steel to withstand high pressures and corrosive environments.
Filter Media: The filter media is the primary filtration element, available in various materials such as sand, activated carbon, or synthetic fibers. The choice of media depends on the specific application and the type of contaminants to be removed.
Backwash Mechanism: The backwash mechanism includes valves, nozzles, or other devices that control the reverse flow of fluid during the cleaning cycle. This mechanism is driven by a motor or pneumatic system.
Control System: The control system monitors the differential pressure across the filter media and manages the backwash cycle. It can be programmed to initiate cleaning based on specific parameters, ensuring optimal performance and minimal manual intervention.
Inlet and Outlet Ports: These ports allow fluid to enter and exit the filter housing. They are designed to accommodate various pipe sizes and connection types, ensuring compatibility with different systems.
Drain and Waste Outlets: These outlets are used to expel the dislodged debris and waste fluid from the filter housing during the backwash cycle. They are typically automated to synchronize with the cleaning process.
Technical Specifications
Understanding the technical specifications of backwash filters is essential for selecting the right filter for a specific application. Key specifications include:
Filtration Efficiency: This measures the filter's ability to capture particles of different sizes. High-efficiency filters can remove particles as small as a few microns, ensuring superior fluid cleanliness.
Flow Rate: The maximum flow rate indicates the volume of fluid the filter can handle per unit of time. Backwash filters are designed to accommodate high flow rates, making them suitable for large-scale applications.
Pressure Drop: The pressure drop across the filter measures the resistance to fluid flow. Lower pressure drop is preferred as it reduces energy consumption and maintains efficient system operation.
Media Capacity: The capacity of the filter media determines the overall filtration capacity of the filter. Higher capacity media allow for longer intervals between backwash cycles.
Material Compatibility: The materials used in the filter housing, media, and seals must be compatible with the fluid being filtered. This ensures durability and prevents corrosion or degradation.
Operating Pressure and Temperature: The filter must withstand the operating pressure and temperature conditions of the application. Specifications include maximum allowable pressure and temperature ranges.
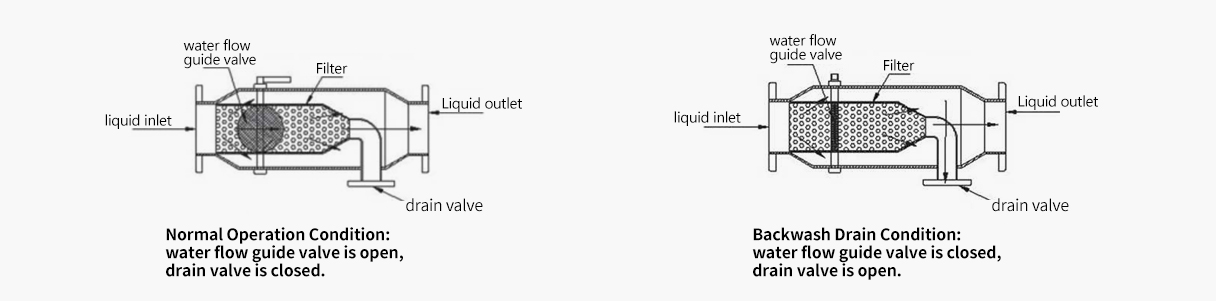
Application Fields
Backwash filters are used in a wide range of applications to ensure clean and efficient fluid systems:
Water Treatment: In water treatment plants, backwash filters remove suspended solids, algae, and other contaminants from raw water, ensuring clean water for municipal and industrial use.
Petrochemicals: In the petrochemical industry, backwash filters protect equipment and processes by removing particulates from hydrocarbons, solvents, and other fluids.
Food and Beverage: These filters are used to maintain the purity of ingredients and final products, ensuring compliance with strict hygiene and safety standards.
Pharmaceuticals: In pharmaceutical manufacturing, backwash filters remove contaminants from process fluids, ensuring product quality and preventing contamination.
Power Generation: In power plants, backwash filters protect turbines, boilers, and cooling systems by removing debris and contaminants from water and other fluids.
Agriculture: In agricultural applications, backwash filters are used to purify irrigation water, ensuring the health and productivity of crops.
Conclusion
Backwash filters are vital tools for maintaining clean and efficient fluid systems across various industries. By understanding their working principles, components, technical specifications, and application fields, we can appreciate their crucial role in ensuring operational efficiency, product quality, and equipment longevity. Whether in water treatment, petrochemicals, food and beverage, or pharmaceuticals, backwash filters provide reliable and continuous filtration solutions.
{sval:sql sql='SELECT n_parameter FROM dede_addonarticle WHERE aid = ~aid~ ' } {/sval:sql}
{sval:sql sql='SELECT n_parameter FROM dede_addonarticle WHERE aid = ~aid~ ' } {/sval:sql}