A bag filter dust collector, often referred to as a baghouse, is an air pollution control device that is used to filter out dust and other particles from the exhaust gases of industrial processes. The "bag" in its name refers to the fabric bags that serve as the filtering medium.
The primary function of a bag filter dust collector is to ensure the purification of air or gases by capturing the dust particles suspended in it. The critical components of this system include a dusty gas chamber, a clean gas chamber, the fabric bags or filters, and the dust collection equipment.
The polluted air or gases enter the dusty gas chamber and pass through the fabric bags which catch and retain the dust particles. As the gas passes through the fabric bag, the dust particles get trapped in the fabric while the clean gas escapes through the top of the bag into the clean gas chamber.
Bag filter dust collectors stand out for their efficiency, as they can effectively filter very fine dust particles. They are commonly used in a variety of industries, including power plants, steel mills, pharmaceutical producers, chemical producers, and more.
In conclusion, a bag filter dust collector is a crucial piece of equipment for industries, especially those producing considerable amounts of dust and particulates. It plays a vital role in maintaining air quality, ensuring a safer working environment, and contributing to environmental protection.
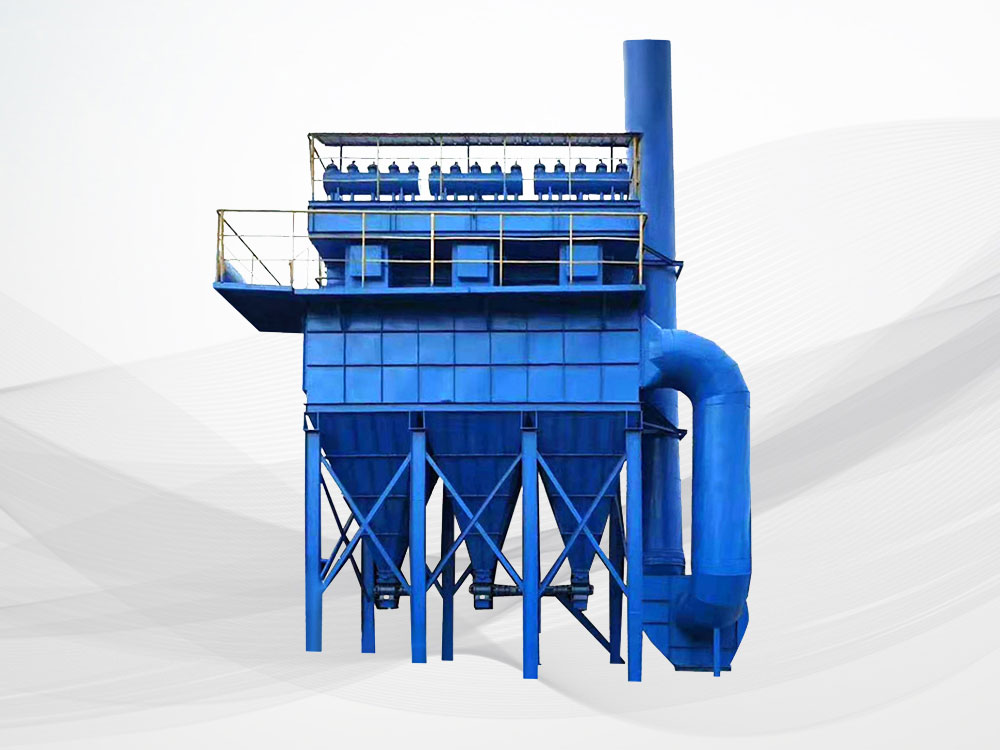
Of course! Baghouse dust collectors brag multiple advantages stemmed from their design and functionality, which makes them desirable in diverse industrial settings.
High Efficiency: Baghouse dust collectors' efficiency rate is impressively high, often exceeding 99%. They can effectively capture finely divided dust particulates that may otherwise escape into the atmosphere, thus making them an excellent solution for pollution control.
Versatility: Due to their design, bag filters can handle a wide range of dust loads, particle sizes and applications, ranging from extremely fine to coarse particulates. With various fabric filter options available, they can be customized to suit specific needs.
Low Operating Cost: As the system employs fabric bags that are replaceable and often have a long service life, the day-to-day running cost of these systems is relatively low.
Heat and Moisture Tolerance: Certain fabric materials used in bags can withstand high temperature and moisture, making baghouses suitable for applications in harsh environments.
Recoverable Product: The baghouse dust collectors provide an opportunity for the collected dust to be reclaimed and put back into the process or sold as a by-product, reducing the waste and providing financial benefits.
Proven Technology: Baghouse dust collectors have been in use for many years, offering reliable and proven performance, backed by a robust design that can hold up well over time despite being in challenging conditions.
Regulatory Compliance: Baghouses can help manufacturers meet stringent regulations for dust emissions, aiding in adherence to environmental standards.
These key features and benefits are why the baghouse dust collector is the preferred choice for many industries. Ultimately, they offer effective pollution control, creating safer workplaces, and contributing positively to the environment.
Baghouse dust collectors assist businesses in adhering to environmental regulations in several ways:
Emission Control: Baghouse dust collectors are highly efficient in capturing dust particles, with efficiency levels often exceeding 99%. This enables businesses to reduce their particulate emissions to levels that comply with local, national, and international standards, thus aiding in pollution control.
Reduced Waste: These systems also allow for the collection and reprocessing of particulate materials, which would otherwise be discarded as waste. Reusing or selling these by-products not only decreases waste but also provides an opportunity for additional revenue.
Cleaner Workplaces: By removing dust and particulates from the air, baghouse dust collectors contribute towards providing a healthier work environment. This aids in adherence to occupational health and safety requirements, besides promoting environmental responsibility.
Noise Reduction: Some baghouse dust collectors are designed in a way that muffles noise produced by industrial processes, contributing to a less disruptive effect on the surrounding environment.
Energy Efficiency: Modern baghouses are designed with energy efficiency in mind. By re-circulating filtered air back into the facility, they can reduce the amount of energy required to heat or cool incoming air, thus reducing the carbon footprint.
By integrating a baghouse dust collector into their operations, businesses can better comply with environmental regulations, reduce potential penalties or fines, and contribute to environmental sustainability. It's an invite to both ecological responsibility and economic efficiency.
A baghouse dust collector consists of several main components, each serving a critical role in the overall operation of the system. Here's a thorough rundown:
Dust Hopper: Located at the bottom, the dust hopper is the collection point for the dust and particulate matter that the collector removes from the air. It often has a funnel-shaped design which enables easy removal of collected dust.
Collection Bags/Filter Bags: The heart of the system, these bag-shaped filters are designed to capture dust particles while allowing clean air to pass through. They can be crafted from various fabric materials to suit different applications.
Bag Cages: These support structures present inside the filter bags help maintain their shape, ensuring they don’t collapse under the pressure of air being sucked through them.
Pulse-Jet Mechanism: Used in pulse-jet baghouses, this mechanism sends a sudden burst of high-pressure air down into the filters at regular intervals to remove dust caked on their surface, maintaining their efficiency.
Cleaning Mechanism: In addition to the pulse-jet mechanism, other cleaning mechanisms such as reverse-air or shaker might be used, depending on the baghouse design, to dislodge accumulated dust from the filters over time.
Inlet and Outlet: The inlet directs contaminated air into the baghouse while the outlet allows the cleaned air to exit the system.
Fan System: This draws in the air containing dust particles and pushes out the filtered, clean air. The size and power of the fan depend upon the volume of air the system is required to handle.
Control System: Modern baghouse dust collectors may feature an automated control system, equipped with sensors and timers, to monitor the cleaning process and other operations, providing real-time data for efficient functioning.
These components work together to ensure the baghouse dust collector efficiently removes dust and particulates from industrial emissions, helping to maintain cleaner air and a safer working environment.
Certainly, the filter bags of a baghouse dust collector, also known as fabric filters, are made from a variety of materials. The choice of fabric material depends on the nature of the dust particles, the operating temperature, and the chemical composition of the gases passing through the collector. These materials include:
Polyester: This is a popular choice due to its excellent stability, good air permeability, and fair price. It is suitable for treating dry, non-corrosive gases at normal temperatures.
Aramid (Nomex): Aramid offers excellent resistance to high temperatures, abrasion, and a wide variety of chemicals. It's often used in high-temperature applications.
Polypropylene: With excellent resistance to most acids and alkalis, polypropylene lends itself well to applications dealing with chemically hostile conditions.
Polytetrafluoroethylene (PTFE or Teflon): This material is used for its excellent performance in highly corrosive environments and its ability to withstand high temperatures.
Fiberglass: Known for its high-temperature tolerance, fiberglass is often used where temperatures exceed the limits of typical synthetic materials.
Polyacrylonitrile (PAN or Acrylic): This fabric offers good hydrolysis resistance in wet applications and can handle a fair amount of organic solvents and oxidizing agents.
The proper choice of material for the filter bags enhances the performance of a baghouse dust collector and extends its operational lifespan. Therefore, an understanding of different filter media and their compatibilities with specific applications is crucial.
Let's dive into the working principle of a baghouse dust collector:
Ingestion: The dust-laden air enters the dust collector through the inlet. This contaminated air can be derived from various industrial processes such as cutting, grinding, or blasting.
Separation: As the air passes through the system, larger, heavier dust particles begin to separate due to gravity and inertial forces, falling into the dust hopper at the bottom of the collector.
Filtration: The smaller particles, carried with the air stream, reach the filter bags. These bags, made from various materials depending on specific needs, act as a sieve. The dust particles are captured on the surface of the bags while clean air passes through the fabric and exits through the outlet on the top.
Purge cycle: Over time, a layer of dust, known as a dust cake or filter cake, builds up on the surface of the filter bags. Once this layer becomes too thick, it can start to restrict the flow of air. At this point, the dust needs to be dislodged from the filter surface. Depending on the design of the baghouse, this could be done using a variety of techniques like pulse-jet cleaning, shaker, or reverse-air cleaning.
Clean-air exhaust: The cleaned, dust-free air is then released into the atmosphere through the outlet. Optionally, it can be recycled back into the facility for energy conservation purposes.
Dust disposal: The dust that has been collected in the dust hopper can then be manually or automatically removed from the system for disposal.
So, in essence, a baghouse dust collector works by drawing contaminated air in, passing it through filters to remove the dust, and then exhausting the clean air back out, while retaining the dust for proper disposal. This process aids in air purification, ensuring a safer working environment in industries.
The technical specifications and product parameters of baghouse filter systems can vary greatly depending on the specific needs of a facility. However, below are some general specifications that might apply:
Size and Dimensions: Baghouse filters can range in size from small, portable units to large, stationary units. The size is determined by factors such as air volume, dust load, and physical size constraints of the facility. This can be defined in terms of the number of filter bags (which can range from tens to thousands) or the total filter area (square feet, or square meters).
Filter Bag Material: The type of fabric used in the filter bags plays a huge role in determining the efficiency and durability of the baghouse system. Common materials include polyester, polypropylene, Nomex, PTFE, fiberglass, and more. The material is chosen based on factors such as the nature and temperature of the dust, and the desired filtration efficiency.
Cleaning Mechanism: As mentioned earlier, common cleaning mechanisms are pulse-jet, shaker, and reverse-air. Efficiency of the cleaning process will affect the system’s operating pressure and thus energy consumption.
Filtration Efficiency: This depends on the type of dust and filter material, but a good baghouse filter should have an efficiency rating of above 99%.
Airflow and Pressure Drop: Given in cubic feet per minute (CFM) or cubic meters per hour (m³/h), this measures the volume of air the filter can clean. The pressure drop is a measure of how much resistance the air meets while passing through the filter.
Temperature Resistance: Depending on the dust source, baghouse filters may need to handle high temperature gases. The maximum operating temperature is dictated by the material of the filter bags.
Installation and Maintenance Considerations: Some Baghouse filters are custom made to fit existing system, and others require dedicated space. The frequency of filter replacement and ease of maintenance also contribute to total cost of ownership.
Remember that not all baghouse filters are the same. The best choice of dust collector varies based on the specific situation of a facility, such as type and volume of the dust, the temperature and moisture level of the air, and local regulations on emissions etc. It is always recommended to work with an experienced professional when designing and selecting a baghouse filter system.
The installation and maintenance costs of dust collectors significantly impact the Total Cost of Ownership (TCO). Here's how they contribute:
Installation Costs: These include costs related to purchasing the dust collector, transporting the device, setting it up, and integrating it with the existing system. Initial size, design, and infrastructure adjustments also add up to the installation cost.
Operational Costs: These are ongoing costs that include electricity consumption, compressed air usage (for pulse jet dust collectors), or other power needs. Costs of periodic checks and inspections to ensure everything runs as it should also come under operational costs.
Maintenance Costs: Regular maintenance is a crucial aspect of dust collector ownership. This encompasses everything from minor routine services to major system repairs and parts replacement if required. Notably, the filter bag replacement is a significant portion of maintenance costs. The frequency of maintenance and the associated downtime should also be considered.
Downtime Costs: These include losses incurred due to production disruptions during maintenance and filter change intervals. Moreover, if the collector malfunctions, the associated downtime could significantly impact overall productivity.
Disposal Costs: The dust that has been collected needs to be disposed of. This is a variable cost depending on the volume and type of the waste and local regulations for waste disposal.
Replacement Costs: At the end of the dust collector’s lifecycle or if an upgrade is necessary, substantial costs may arise from having to purchase and install a new system, or to upgrade the existing one.
To reduce the TCO, it's crucial to choose a dust collector that not only fits the initial budget but is also cost-effective to operate and maintain in the long run. Factors like durability, energy consumption, ease of maintenance, and the life cycle of filter bags play significant roles in determining the total cost of ownership over the dust collector's lifespan. It's also worth considering warranties and after-sale services that could potentially mitigate any unexpected costs.
The performance and applicability of baghouse dust collectors can vary greatly under different conditions. Let's consider a few scenarios:
High Dust Load Conditions: Baghouse dust collectors excel in high dust load conditions, such as woodworking facilities, grain processing plants, or cement production. The units are designed to handle significant dust volumes without compromising efficiency. However, in extraordinarily high dust situations, a pre-cleaning device might be installed before the baghouse to enhance the lifespan of the filter bags.
High-Temperature Conditions: If the dust source generates high temperature gases, such as metalwork or some types of chemical manufacturing, a high-temperature resistant bag material (like Nomex or fiberglass) would be essential to avoid bag degradation. Moreover, some baghouse designs can handle high-temperature applications by incorporating heat-resistant elements in their construction.
Moisture-Rich or Sticky Dust Conditions: In scenarios where the dust particles are moist or sticky, such as food processing or certain chemical productions, special care must be taken to avoid filter bag clogging. Proper selection of filter material and regular bag cleaning can help maintain efficiency under such conditions.
Fine or Toxic Dust Conditions: Baghouse collectors are very effective in capturing fine, airborne dust particles, which are a common byproduct in many industries including pharmaceuticals, mining, and some chemical processes. When dealing with toxic or harmful dust, fully enclosed baghouse designs provide excellent containment of the hazardous particulates.
Space-Restricted Conditions: For facilities with limited space, compact baghouse designs are available which leverage high-efficiency filter material to achieve impressive dust collection capability within a small footprint. This is beneficial in urban environments or when retrofitting existing buildings.
Emission Regulation Requirements: Especially in regions with strict environmental regulations, a high-performance baghouse dust collector can ensure compliance with air quality standards. This is particularly important for industries like fossil fuel power plants, waste incineration facilities, and any large-scale industrial operations that emit significant amounts of particulates.
It's always important to note that the specific performance of a baghouse dust collector will rely heavily on proper selection, installation, and maintenance. Always work with an experienced professional to ensure the system is properly tailored to the specific needs and conditions of the facility.
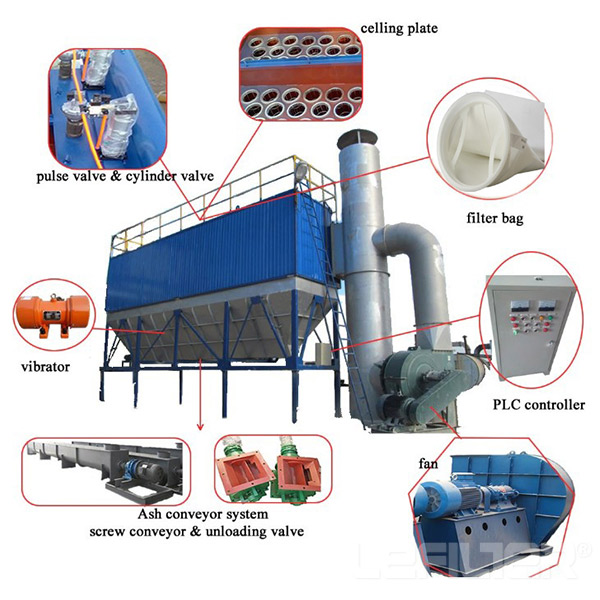
Baghouse dust collectors are versatile systems that have found wide applications across various industries due to their efficiency and adaptability. Here are some key industrial sectors where these systems are commonly used:
Woodworking: Sawdust and wood chips generated during woodworking processes can pose significant health risks and create a major fire hazard. Baghouse dust collectors efficiently trap these particles, ensuring a cleaner and safer workplace.
Metalwork and Foundries: These industries generate substantial amounts of dust from grinding, sanding, and other fabrication processes. Baghouse systems, especially high-temperature resistant ones, are ideal for collecting these particles.
Pharmaceuticals: In this sector, dust can not only pose a health hazard, but also potentially contaminate products. Baghouse filters provide efficient, enclosed dust collection, which is crucial here.
Mining and Quarrying: Mining operations generate an enormous amount of dust, especially during the extraction and crushing processes. Baghouse systems can capture this dust, helping to protect workers’ health and the local environment.
Food Processing: Dust generated from grinding, mixing, baking, or packaging food products must be properly managed to ensure food safety. Baghouse dust collectors can effectively collect such dust, maintaining clean environments.
Chemical Processing: Dust particles in these industries can be highly toxic or even explosive. An efficient dust collection system like a baghouse can help maintain safety standards and avoid environmental contamination.
Cement Production: Production of cement involves grinding and heating processes that result in substantial dust generation. Baghouse systems efficiently manage this dust, reducing the impact on both workers and the environment.
Waste Processing: During waste treatment, especially incineration, significant amounts of particulates are released into the air. A baghouse dust collector can capture these particles, helping facilities meet emission regulations.
Agriculture: Grain processing generates dust which, besides being a health hazard, can also lead to combustible dust explosions. Baghouse systems effectively manage this risk.
Power Generation: Coal-fired power plants generate flue gas with high levels of pollutants. Baghouse filters can efficiently capture these particles, helping plants comply with environmental standards.
Each application of baghouse dust collectors may have unique requirements in terms of collector size, filter material, cleaning method, and more. Therefore, the ideal system will vary based on the specific needs and constraints of each individual operation.
Regular maintenance and upkeep of a baghouse dust collector are vital to ensure it operates efficiently and maintains its full dust-collecting capacity. Here are some detailed steps:
Inspection of Filter Bags: Regularly inspect the filter bags for wear and tear, holes, or any premature failure. Damaged bags should be replaced promptly to ensure the efficiency of the dust collector. It's also a good practice to keep a stock of filter replacements on hand for quick changes.
Cleaning of Filter Bags: Cleaning frequency depends on the dust load and types of dust particles. Pulse jet baghouses regularly clean the bags with a pulse of compressed air. However, sometimes manual shaking or a total bag replacement might be necessary if dust cake develops or cleaning mechanisms fail.
Checking of Pressure Drop: Monitor the pressure drop across the baghouse. A pressure drop that's too high or too low can be a sign of issues like filter leaks, dust cake formation, hole in bags, or problems with the cleaning mechanism.
Inspection of Baghouse Structure: Regularly check the dust collector's structural components including the housing, hoppers, and dust discharge systems. Look for cracks, leakages, and ensure that the discharge system is functioning properly to prevent dust re-entrainment.
Checking of Airlock Devices: Make sure that rotary valves or other airlock devices are functioning properly. A malfunctioning airlock can lead to the escape of dust back into the workplace or the re-entrainment of dust into the baghouse.
Inspection of Cleaning Systems: The cleaning mechanisms should be checked regularly for proper functioning. This includes the pulse-jet system, solenoids, diaphragm valves, or mechanical shakers in a shaker baghouse.
Monitoring of Dust Emissions: Regular monitoring of dust emissions from the baghouse outlet can help identify filter failure or inadequate cleaning.
Reviewing Operational Parameters: Regularly review the operational parameters such as air-to-cloth ratio, can velocity, and interstitial velocity. Deviations from optimal levels can lead to reduced efficiency or increased bag wear.
Scheduled Maintenance and Documentation: Establish a regular maintenance schedule based on the manufacturer’s recommendations and keep records of all inspections, cleanings, and part replacement for future reference.
Remember, preventive maintenance can minimize expensive repair costs and extend the life of your baghouse dust collector system. Be sure that maintenance and inspections are carried out by trained professionals to ensure the system operates at peak performance.