A Bag Filter is an efficient filtration device that purifies liquid by trapping solid particles when fluid passes through a filter bag under pressure. It has significant processing capacity, precision filtration, and is easy to install and replace while being compact and corrosion-resistant. Its use is extensive in various industries like food, beverage, pharmaceutical, and electronics for liquid purification. As for its functioning, it traps impurities when fluid flows in under pressure and discharges clean fluid. The choice of a Bag Filter depends on its quality, specifications, filtration accuracy, and material. Regular maintenance, including filter bag replacement and proper cleaning, is necessary for its optimal performance. In essence, Bag Filters are acclaimed for their exceptional filtration and vast applicability.
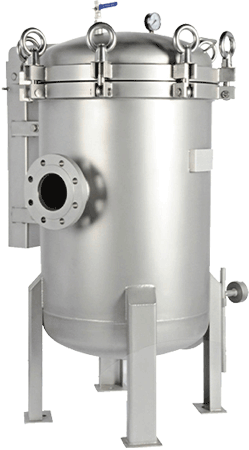
Bag Filters, often referred to as Baghouse Filters, are known for their superior quality, versatility, and efficiency in the filtration industry. They have gained a remarkable reputation due to these unique features:
High Efficiency: One of the most significant advantages of bag filters is their high efficiency. They can remove up to 99.99% of dust particles, even as small as one micron. This makes them incredibly useful for applications that require stringent particle control.
Wide Range of Applications: Bag filters can be used in a variety of industries, including food and beverages, pharmaceuticals, electronics, and chemicals, for the removal of solid particles from liquids. They are particularly beneficial in industries that require high purity or particle-free fluids.
Cost-Effective: Due to their high durability and longevity, bag filters are cost-effective investments. Their reliable performance reduces maintenance expenses over time, promoting cost savings.
Easy Operation and Maintenance: Bag filters are user-friendly. They are easy to install and operate. Additionally, their maintenance involves simple bag replacement, which can be performed swiftly without requiring substantial downtime.
Space Efficiency: Given their compact design, bag filters require less space compared to other filtration devices.
Versatile Filtration Grades: Bag filters offer a wide range of filtration grades, from coarse to fine, making them adaptable to various filtration requirements.
Exceptional Durability: Bag filters are made from robust and high-quality materials that resist corrosion and handle harsh environments effectively, enhancing their lifespan.
Environmentally Friendly: Through efficient filtration, bag filters contribute to environmental protection. They minimize the amount of debris released into the environment, aiding in pollution control.
In conclusion, Bag Filters are an excellent filtration solution thanks to their efficiency, versatility, cost-effectiveness, and environmental friendliness, making them a preferred choice across various industries.
Bag Filters, often referred to as Baghouse Filters, are known for their superior quality, versatility, and efficiency in the filtration industry. They have gained a remarkable reputation due to these unique features:
High Efficiency: One of the most significant advantages of bag filters is their high efficiency. They can remove up to 99.99% of dust particles, even as small as one micron. This makes them incredibly useful for applications that require stringent particle control.
Wide Range of Applications: Bag filters can be used in a variety of industries, including food and beverages, pharmaceuticals, electronics, and chemicals, for the removal of solid particles from liquids. They are particularly beneficial in industries that require high purity or particle-free fluids.
Cost-Effective: Due to their high durability and longevity, bag filters are cost-effective investments. Their reliable performance reduces maintenance expenses over time, promoting cost savings.
Easy Operation and Maintenance: Bag filters are user-friendly. They are easy to install and operate. Additionally, their maintenance involves simple bag replacement, which can be performed swiftly without requiring substantial downtime.
Space Efficiency: Given their compact design, bag filters require less space compared to other filtration devices.
Versatile Filtration Grades: Bag filters offer a wide range of filtration grades, from coarse to fine, making them adaptable to various filtration requirements.
Exceptional Durability: Bag filters are made from robust and high-quality materials that resist corrosion and handle harsh environments effectively, enhancing their lifespan.
Environmentally Friendly: Through efficient filtration, bag filters contribute to environmental protection. They minimize the amount of debris released into the environment, aiding in pollution control.
In conclusion, Bag Filters are an excellent filtration solution thanks to their efficiency, versatility, cost-effectiveness, and environmental friendliness, making them a preferred choice across various industries.
A Bag Filter, also known as a Baghouse Filter, comprises various essential components each with a specific function to ensure optimal performance. Below is a detailed breakdown of the key components:
Filter Bags: This is the heart of the filter system and comes in different materials, sizes, and shapes. Their purpose is to capture the solid particles from the inflowing fluid. The bag's material and pore size are selected based on the type of liquid, the nature of the contaminants, and the filtration requirements.
Bag Housing: The bag housing encloses the filter bags, supporting mechanisms, and inflow and outflow ports. It is usually made of corrosion-resistant materials such as stainless steel to endure diverse environmental conditions.
Inlet and Outlet Ports: These are paths for the fluid to enter and exit the filtration system. The inlet port allows the fluid to flow into the filter housing, while the outlet allows the filtered liquid to exit.
Bag Support and Sealing Mechanisms: The bag support provides structural integrity to the filter bag, preventing it from collapsing under the flow pressure. The sealing mechanism ensures a leak-proof operation by tightly securing the filter bags in their place.
Dirt Collection Chamber: This part collects the particles filtered out from the fluid. The solid waste collected can be periodically removed from this chamber.
Cleaning Mechanisms: Certain bag filters include mechanisms for automatic cleaning or bag replacements, such as pulse-jet cleaning, to enhance the filter's efficiency and extend the service life.
Pressure Gauge: This component is used to monitor the pressure drop across the filter, providing an indication of when the filter bag needs to be replaced.
In summary, each part of a bag filter plays a crucial role in maintaining its efficiency and operational integrity, ensuring effective filtration performance tailored to specific user requirements.
The technical specifications of a bag filter vary greatly according to specific applications and requirements. However, there are some standard parameters that define a bag filter's capabilities. Here's a detailed overview:
Size: This represents the physical dimensions of the filter housing including height, diameter and the volume it can accommodate.
Material: The material for both the filter bag and the bag housing needs to be specified. Stainless steel is a common choice for the housing thanks to its durability, while bags can be made from many materials including polyester, polypropylene, nylon, and more, chosen based on the compatibility with the fluid being filtered.
Efficiency: This indicates the degree of filtration provided by the bag filter. It's also referred to as the filter's "micron rating". A lower micron rating means a smaller pore size, which captures smaller particles, thus increasing filtration effectiveness.
Flow Rate: This shows how much fluid can move through the filter per unit of time. This is crucial to match the filter's capability to the systems demand.
Pressure Drop: This refers to the pressure loss that occurs as the fluid passes through the filter. A lower pressure drop means less energy is required for the fluid to flow through the filter.
Operating Pressure: The maximum allowable pressure at which the filter can safely operate.
Operating Temperature: The range of temperatures the filter bag material can withstand.
Sealing Mechanism: The means by which the bag filter is sealed to prevent leakage. This could be an ‘O’ ring or a bead seal style.
Ports: The number of inlet and outlet ports and their location (side, top or bottom) and dimensions.
Bag Capacity: Defines the amount of particles a filter bag can hold before needing to be replaced.
Understanding these technical specifications and parameters is crucial when choosing a bag filter system to ensure it meets the exact requirements of any specific application and environment.
A Bag Filter, also commonly known as a Baghouse Filter, operates on a relatively straightforward principle. Below, the working process of a bag filter is described:
Ingestion of Inflow: Unfiltered fluid is directed into the bag filter system through the inlet port. The design of the filter housing ensures the fluid flows in such a way that it evenly permeates the outer surface of the filter bag.
Filtration Process: As the fluid travels from the outside of the bag towards the inside, solid particles are trapped within the bag material, more specifically, by the fine mesh of the bag material. The size of the particles that can be trapped, also defined as the micron-rating of the filter, is determined by the pore size of the bag material.
Collection of Filtered Fluid: The filtered fluid collects inside the bag, essentially within the internal space confined by the filter bag. Due to the differential pressure created by the influent stream, the liquid is forced to exit through the inner side of the bag.
Discharge: The clean, filtered fluid then exits the system through the outlet port, leaving behind the solid particles contained by the filter bag.
Disposal of Waste: Once the filter bag has reached its holding capacity, the filtration process is halted, and the bag needs to be replaced. The solid particles are usually disposed of along with the used filter bag.
Filter Bag Replacement: Once the bag is completely filled with trapped particles and becomes less efficient or non-operational, it can be manually or automatically removed, and a new filter bag is installed.
In short, a bag filter operates through a simple yet effective principle of separation using a filter media, ensuring that the fluid passing through it is clean and clear of all undesired particulate matter. Continual maintenance and bag replacements ensure long-term, efficient operation.
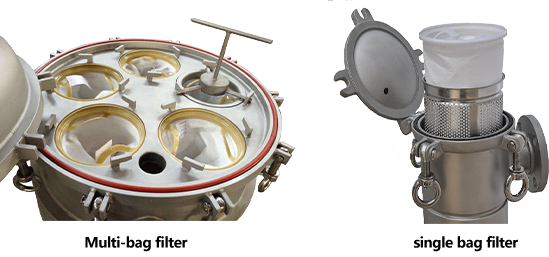
The necessity to replace the filter bag in a baghouse filter depends on a variety of factors. Here are some key indicators that suggest it may be time to replace the filter bag:
Increased Pressure Drop: A significant increase in the pressure difference across the filter is typically the first indicator that the filter bag needs replacement. This indicates that the bag is clogged with particulate matter, hindering the normal flow of fluid.
Decreased Filtration Efficiency: If you notice that more particulates are making their way through the filtration system, it may be because the filter bag is worn or damaged, allowing some contaminants to bypass it. This not only results in decreased filtration efficiency but can also cause downstream equipment to wear out more easily due to the increased particulate load.
Visible Wear and Tear: Regular inspections of filter bags can reveal visible signs of wear and tear, such as holes, abrasions, or thinning material, which suggest that it's time for a replacement.
Scheduled Maintenance: Filter bags should be replaced as part of regular, scheduled maintenance to avoid unexpected failures. The frequency of this may depend on the type of application, the nature of the fluid being filtered, and the environment in which the filter is operated.
Systematic Testing: Many industries also carry out systematic testing of the filter bag. If test results reveal that the bag's performance has decreased below the acceptable level, it should be replaced.
Time-Based Replacement: Finally, some industries operate on a time-based replacement schedule, particularly if the filter bag is used in applications with very high particulate loads or where filter failure can have serious consequences.
In conclusion, the exact timing of when to replace a filter bag in a bag filter system can vary widely depending on the specific filtering application. Regular monitoring and maintenance can extend the bag's life and ensure the filtration system continues to function efficiently and effectively.
Bag filters, also known as baghouse filters, are utilized in numerous applications across various industries due to their efficiency, cost-effectiveness, and simplicity in design. Below are some key industries and applications where bag filters are extensively used:
Mining Industry: Bag filters are employed in the mining industry to control airborne dust and particulates, thus reducing environmental impact and improving the health safety of miners.
Cement Industry: They are used in cement plants to capture dust particles emitted during various stages, including milling, crushing, and packing, ensuring cleaner air circulation and minimizing the risk of dust explosions.
Food and Beverages Industry: In the food and beverage industries, bag filters are used to filter out impurities from liquids, ensuring the safety and quality of the end products. This includes applications in brewing, dairy, sugar, and oil processing.
Waste Management: Bag filters play an integral role in waste treatment plants, helping to remove particles from wastewater and reduce air pollution in waste incineration processes.
Chemical and Pharmaceuticals Industry: These industries require high cleanliness standards, hence the need for effective filtration solutions. Bag filters help remove particulate contaminants during the manufacturing process of drugs and chemicals.
Power Generation: In power plants, especially coal-fired ones, bag filters are used to reduce the particulate matter emissions, thus controlling air pollution.
Oil and Gas Industry: Bag filters assist in the filtration of drilling fluids, cutting oils, and fracturing fluids, contributing towards efficient operations and reduced environmental impacts.
Metalworking Industry: In metalworking and manufacturing processes where creating a polished final product is essential, bag filters can be used to filter out metal shavings, dust, and other particulates.
Agriculture: Bag filters are employed in agricultural applications for filtering water used in irrigation systems, ensuring the water's purity and health of crops.
Paint and Coating Industry: They help filter out impurities during paint manufacturing and in spray booth exhausts to capture excess paint particles.
In conclusion, bag filters find vast applications owing to their versatility, efficiency, and effectiveness in removing particulate matter from air, gas, and liquids, thereby covering a diverse array of industrial sectors.
Setting up and maintaining a bag filter system involves many steps which are crucial for ensuring its long-term, smooth functioning and consequent returns on investment.
Use of Bag Filters:
Installation: Start by making sure that the bag filter is installed correctly. It should be done by a trained professional who adheres to the manufacturer's guidelines.
Operation: During operation, ensure that the bag filter system isn't subjected to conditions beyond the ones it is designed for - fluid flow, chemical composition, temperature, and pressure - to prevent damage and inefficiency.
Monitoring: Regular monitoring of the bag filter's performance, particularly pressure drop across the filter and the quality of filtrate, helps to infer the filter's condition and anticipate when a replacement might be needed.
Maintenance of Bag Filters:
Cleaning: Regular cleaning of the filter bag is pivotal. Most bag filters are designed to be cleaned in place with a backward or reverse flow of fluid, which dislodges trapped particles. However, it is crucial to follow the manufacturer's instructions to avoid damaging the filter material.
Inspection: Regular visual examination of filter bags will help identify signs of wear and tear like abrasion or thinning material, or any visible damage such as holes, which suggest an immediate replacement.
Scheduled Replacement: Even without any clear signs of damage, age alone can reduce a filter bag's performance. Having an organized, regular schedule for filter replacement can be helpful, providing a balance between using the filter for as long as it's still performing efficiently and preventing an unexpected filter failure.
Documentation: Keeping a detailed record of filter replacements, performance over time, any damage or extraordinary events will assist in establishing an effective, tailored maintenance plan in the long run.
Training: Everyone involved in the operation of the filter system should be well-trained and familiar with the manufacturer's guidelines, as well as signs of potential problems with the system.
In conclusion, proper use and maintenance of a bag filter system is a balance between regular monitoring, preventive maintenance, and strategic planning. The key is to get the maximum use out of each filter bag without compromising the filtration system's overall performance.
Differences amongst filter bag materials primarily impact their efficiency, useful life, and suitability for specific applications. Here's how:
Cotton (Woven): This is a cost-effective solution for non-abrasive particulates in environments where chemical resistance and high temperatures aren't concerns. It's used in applications such as food industries and pharmaceuticals.
Polyester: This material is popular for its versatility. It has good resistance to most acids and alkalis, and it's also hydrophobic, meaning it repels water. This makes it suitable for diverse applications including pharmaceuticals, food and beverage, and chemical industries.
Polypropylene: Polypropylene has excellent water and chemical resistance, with high durability against most acids and alkalis. This makes it a great fit for applications such as water and wastewater treatment, and corrosive fluids filtration in chemical plants.
Nylon (Cerex®): Nylon has good abrasion resistance, making it suitable for high solid load applications where the particulates can wear the filter material over time. It is also effective in alkaline environments.
Acrylic (Homopolymer Acrylic Felt): This material performs well under wet and low pH conditions, making it an excellent choice for emissions control in power plants and other high humidity processes.
Aramid (Nomex®): Known for its heat and fire resistance, this material thrives under high temperatures up to 204°C. It's used in industries like asphalt production, cement kilns, and metal production where high temperatures are involved.
Fiberglass: Due to its high temperature resistance and efficiency in collecting small particles, fiberglass is often used in industries with hot gas filtration needs such as power generation, incinerators, and metal smelting processes.
Felt and Woven Wool: These materials excel in applications where high dirt-holding capacity is advantageous. They can accommodate large or heavy particles and are ideal for dust collection and dry processing applications.
To summarize, the choice of bag filter material greatly affects the performance outcome. The material should be chosen based on factors like the characteristics of the fluid, the desired filtration efficiency, the size and nature of particles, temperature, flow rate and other operating conditions. A well-chosen material can increase efficiency, prolong the lifespan of the filter bag, and thereby save money and resources over time.