Ultrafiltration Equipment is a key component in the field of water purification and fluid processing. Using the principle of size exclusion, it separates unwanted particles, impurities, and large molecules from a liquid.
The main feature of our Ultrafiltration Equipment is its cutting-edge membrane technology. The semipermeable membrane, which is the heart of the equipment, only allows smaller molecules to pass through it, while larger particles are trapped and discarded. This results in a filtrate of high quality, without the presence of any undesirable elements. The membrane is also characterized by a high durability, ensuring that the equipment can withstand high volumes and long hours of operation without losing its filtration effectiveness.
Our ultrafiltration systems are designed to be energy-efficient and environmentally friendly. Unlike conventional methods, our equipment does not rely heavily on chemicals for the filtration process. This results in not only reduced operating costs but also minimizes the impact on the environment.
The versatility of the Ultrafiltration Equipment is another significant advantage. This device is applicable to various sectors, including pharmaceutical, food and drink, chemical, and environmental industries. It can efficiently handle different types of liquids, irrespective of their composition and viscosity. Furthermore, the membrane is resistant to a broad pH range, making it suitable for processes involving acidic or alkaline fluids.
Our Ultrafiltration Equipment is also user-friendly when it comes to installation and operation. While delivering high-level performance, it is designed to be simple to install and operate. In the unlikely event of any problems arising, we provide clear troubleshooting steps and maintenance guidelines to ensure smooth functioning.
One of the cornerstones of our offering is the comprehensive after-sales support that we extend to our customers. We understand that purchasing such sophisticated equipment is a significant investment, and we assure our customers that we stay with them throughout their journey. Our after-sales service includes timely maintenance checks, prompt resolution of any issues, and ongoing technical support. Moreover, we offer flexible pricing options, making our product accessible to a wide range of customers.
To sum up, our Ultrafiltration Equipment is a high-performing, economical, and environmentally friendly solution for liquid filtration needs. With its robust design, superior filtration technology, user-friendly operation, and comprehensive after-sales support, it offers immense value to any operation it forms a part of. Quality, reliability, and customer satisfaction are at the core of our offerings, and we aim to continue delivering best-in-class filtration solutions with our Ultrafiltration Equipment.

specific features of Ultrafiltration Equipment:
High-Efficiency Filtration: With an enhanced semi-permeable membrane, our Ultrafiltration Equipment operates with the principle of size-exclusion, effectively removing microscopic impurities, solid particles, and macromolecules, thus ensuring a high quality filtered output.
Advanced Membrane Technology: Manufactured using advanced membrane technology, our ultrafiltration systems offer remarkable durability, capable of operating at optimum levels for extended periods. The membranes can effectively withstand PH changes, high temperatures, and pressures.
Energy-Efficiency and Environmental Friendliness: These systems showcase superior energy efficiency, minimizing the impact on the environment. They operate on low energy and without the need for chemicals, which not only reduces operational costs, but also minimizes waste production.
Versatility and Wide Application: Ultrafiltration Equipment holds a wide range of industry applications, including for use in chemical sectors, environmental industries, and the pharmaceutical and food and beverage sectors. Its versatility enables it to purify and filter a diverse array of liquids effectively.
Automated Control System: The systems are outfitted with automated controls to ensure constant monitoring of the operation. This automation allows for easy adjustment of filtration settings, and the provision of troubleshooting procedures helps to achieve an efficient, smooth, uninterrupted process.
Ease of maintenance: Designed for convenient operations and maintenance, the system’s modules can be quickly and easily cleaned or replaced. This easy maintenance characteristic ensures that the systems are always working at their optimal level.
Built-in Monitoring System: Our Ultrafiltration Equipment is also equipped with a state-of-the-art monitoring system that consistently checks the operational parameters of the equipment, helps to prevent faults, and alerts the user if timely maintenance is necessary.
Comprehensive After-Sales Support: We offer a strong after-sales support network, providing customers with prompt responses to inquiries, maintenance checks, replacement parts and ongoing technical advice.
Our Ultrafiltration Equipment is a combination of performance, reliability, and efficiency; striking a balance between advanced technology and user-friendly functionality. The equipment is designed and built with the end-user in mind, making it an incredible addition to any industry that requires fluid filtration.
Certainly, here's a detailed and original explanation of the working principle of Ultrafiltration Equipment:
At its core, Ultrafiltration (UF) is a pressure-driven purification process that separates particulate matter from soluble compounds using an ultrafine membrane media. It is capable of excluding particles ranging in size from 0.001 to 0.1 microns, allowing only clean water and dissolved minerals to pass through.
The process starts with the introduction of the feed liquid, also known as the 'influent', into the system. The influent can be anything from drinking water to industrial effluent.
The high-pressure influent is guided towards the ultrafiltration membrane. This membrane, which is a thin layer of material with microscopic pores, acts as the barrier between the impurities and the filtrate. The pore size of the membrane can be adjusted according to the specific application to achieve the desired level of filtration.
Under the force of the pressure, the water molecules and small dissolved substances will pass through the ultrafine pores of the membrane. Larger particulate matters, bacteria, viruses, or any other contaminants are unable to pass through these pores and are retained, resulting in a concentrated solution known as 'retentate'.
The retained contaminants are then flushed out of the system, ensuring the membrane does not get clogged over time. This flush out process, referred to as backwashing, is an integral part of the maintenance of the system.
The clean, filtered liquid which successfully passes through the membrane is called 'permeate'. This permeate is collected and often subjected to further purification processes, such as disinfection, depending on the purpose of the filtrate.
In summary, the working principle of the Ultrafiltration Equipment is pretty simple and effective: it uses a pressurized system to force the water against a semi-permeable membrane, filtering out the unwanted substances while allowing the purified water to go through. The complete process ensures reliable and efficient filtration, making Ultrafiltration Equipment an excellent option for a wide range of applications.
The process of cleaning an ultrafiltration system, often referred to as the backwash process, generally takes about 20 to 30 minutes. This is essential to maintaining the system's effectiveness and longevity.
It's important to note that the exact length of time can vary depending on a variety of factors, including the size and design of the system, the type and concentration of impurities in the water, and the specific cleaning chemicals or procedures used.
During the cleaning process, the flow of liquid is reversed, flushing out accumulated impurities and preventing clogging of the membrane. This process typically also includes the use of certain chemicals to remove any stubborn or hard-to-eliminate contaminants.
After cleaning, the system can resume normal operation almost immediately. However, it's crucial to follow manufacturer's instructions for the cleaning process to ensure the effectiveness of the cleaning and the safety of the equipment.
Absolutely, let's dive into the key components of Ultrafiltration Equipment and their respective functions:
The Housing: The housing section provides a controlled environment for the filtration process. It's typically sturdy and corrosion-resistant to withstand high pressures as well as various elements present in the feed liquid.
Ultrafiltration Membrane: Undoubtedly, the most crucial part of the Ultrafiltration Equipment. The membrane's semi-permeable nature allows only water and minuscule solutes to pass, while larger molecules and particles are retained. Membranes can be ceramic, polysulfone, or a composite material, depending on the specific application.
Influent Pump: This is the mechanical component that supplies raw or pre-treated water with high pressure to the membrane. The pump ensures the necessary pressure to force the water against the membrane.
Pressure Gauges: These devices monitor the pressure of the influent and the filtrate. Changes in pressure can indicate issues like membrane clogging or pump failure. Thus, they play an essential part in the operation and maintenance of the equipment.
Backwash Pump: It is used to periodically reverse the flow and wash away the accumulated particles from the membrane surface. This process extends the lifespan of the membrane by preventing it from clogging or scaling.
Control Panel: It's the place from which the operator can control and monitor the entire filtration process. The panel often includes components like switches, indicators, and controllers to manage different parameters such as pressure, flow rate, and temperature.
Outlet Pipes: These are used for transporting the cleaned (permeate) and impure (retentate) water out of the system.
Chemical Dosing System: In some ultrafiltration systems, an automatic or manual system for dosing cleaning or disinfecting chemicals is included. This part helps clean the membrane efficiently and ensures purified water's safety.
To summarize, all components of the Ultrafiltration Equipment work in harmony to deliver an efficient filtration process. The result is high-quality water suitable for a variety of applications - from industrial use to potable water.
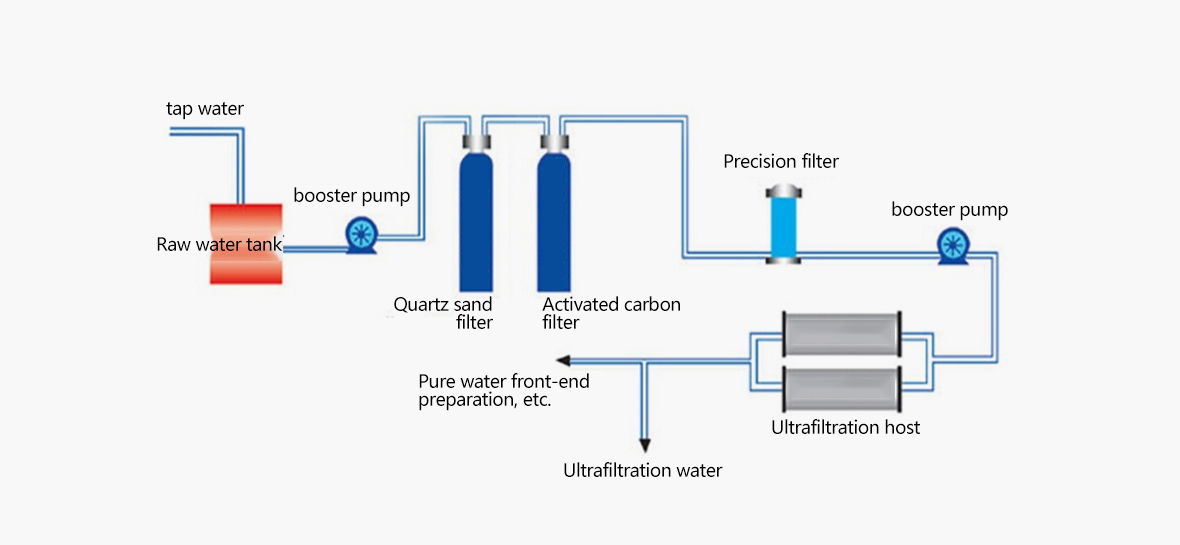
Ultrafiltration equipment can be utilized in a variety of industries, each with their unique needs and applications. Let's look at a few examples:
Water Treatment: This is perhaps the most common application of ultrafiltration. It aids in the removal of bacteria, viruses, and endotoxins, ensuring safe water for drinking and cooking. Additionally, it’s used in treatment of wastewater before it's released back into the environment.
Food & Beverage: In dairy industry, for instance, ultrafiltration is used to concentrate proteins in milk and whey. This method also finds use in the wine and fruit juice sectors to stabilize and clarify the products.
Pharmaceutical Industry: Ultrafiltration is used for the purification and concentration of pharmaceutical products, removal of toxins, and water recycling. This ensures the high purity and quality necessary in this industry.
Electronics Manufacturing: In this field, ultrafiltration is used in the process of creating high-purity water – a key ingredient in electronics manufacturing.
Chemical Industry: It's utilized for the recovery of precious metals, separation of glycerin, removal of oils and fats, and treatment of effluents, to name a few.
Textile Industry: Ultrafiltration assists in treating dye bath effluents, recycling and reusing water, and reducing the salt effect of dye baths.
Bioengineering: In gene therapy and tissue engineering, ultrafiltration is used to concentrate and purify large biomolecules.
The application and function of ultrafiltration equipment in each industry significantly depend on the specific needs and standards of that industry. Despite the differences, its main goal remains the same – to purify and improve the quality of the end product or the resource being treated.
Certainly, let's discuss the key technical parameters of Ultrafiltration equipment.
Filtration Capacity: This refers to the amount of water that can be filtered in a given period. As filtration capacity is dependent on feed water characteristics and operational conditions, it can vary greatly.
Membrane Material: The membrane's material determines its durability, permeability, and resistance to various substances. Common types of membrane materials include polysulfone, polyethersulfone, and ceramic.
Membrane Pore Size: A critical parameter, it determines the filtration effectiveness. Most ultrafiltration systems have a pore size ranging between 0.001 to 0.1 microns.
Operating Pressure: Ultrafiltration typically operates at low pressures, often between 1-10 bar depending on the specifics of the filtration task.
Recovery Rate: It is the percentage of the feed water that gets converted into permeate (or purified water). A higher recovery rate indicates better water efficiency.
Pressure Drop: This refers to the decrease in fluid pressure that occurs as the fluid passes through the membrane. It's critical to maintain it at an appropriate level to ensure efficient operations.
Backwash Rate: In systems that utilize backwashing to clean the membranes, this rate refers to the percentage of filtered water used for this process.
Temperature Range: The range within which the equipment can operate effectively. Excessive heat can damage the membrane and other components.
pH Range: The range of pH the equipment is designed to handle. It's an essential factor for membranes since extreme pH levels can adversely affect their performance.
Turbidity Removal Efficiency: The proficiency of the system at removing suspended solids, measured as a percentage. It's an important criterion for assessing system performance.
Reject Concentration: It refers to the concentration of solids in the waste stream (also called the “concentrate” or “reject”).
Each of these parameters has an essential role to play in the efficiency and usefulness of ultrafiltration equipment, and depending upon the industry and unique process requirements, these parameters could be tailored to suit specific needs.
The choice of membrane material for ultrafiltration equipment is essential as it affects both the efficiency and longevity of the system. Here are some commonly used materials:
Polyethersulfone (PES): This is an extremely durable material known for its wide pH tolerance range, temperature resistance, and excellent mechanical strength. They are particularly suitable for biomedical and food and beverage applications due to their low protein binding characteristics.
Polysulfone (PS): These are robust, high-performance membranes known for their exceptional chemical compatibility and temperature resistance. They are widely used in pharmaceuticals, biotech processing, and food and beverage applications.
Polyvinylidene Fluoride (PVDF): PVDF membranes possess high chemical resistance and are mechanically robust. They are known for their superior performance under harsh conditions, and can be used in a range of applications including wastewater treatment and the food and beverage industry.
Polyacrylonitrile (PAN): PAN membranes offer excellent chemical and fouling resistance. They are commonly used in industries that require high-efficiency separation like dairy to remove bacteria and proteins.
Ceramic Membranes: These membranes are characterized by high mechanical stability, chemical and abrasion resistance as well as a high and constant flux. They are especially suitable for applications under extreme pH conditions or high temperatures.
Cellulose Acetate (CA): These are a type of organic membrane material known for their biocompatibility, making them favorable in the medical field. However, they are sensitive to pH changes and may be attacked by microbes.
Each material has its unique characteristics and selection depends on specific application requirements such as required filtration size, mechanical strength, chemical compatibility, temperature resistance, and cost-effectiveness.