The Duplex filter, also known as a double basket filter, is a type of industrial filter designed for continuous and efficient filtration of fluid in a system. Essentially, it is composed of two filtering elements housed in separate chambers. This unique design allows for continuous operation as one filter can be serviced while the other is in use, thus eliminating the need for system shutdown.
The main function of a Duplex filter is to remove impurities and harmful particles from fluids, improving the reliability and longevity of systems in various industries such as oil and gas, petrochemicals, water treatment, and shipbuilding. These industries often require continuous operations where system shutdown is highly undesirable. The Duplex filter, with its ability to switch between the two filters, caters to this need.
In operation, the incoming fluid enters the filter through the inlet and flows through one of the filter baskets where the impurities are trapped. Once the basket is full, the flow is automatically diverted to the second filter basket allowing the first to be cleaned or replaced without interrupting the flow or requiring system shutdown.
Manufactured from corrosion-resistant materials like stainless steel, Duplex filters are robust, offering long operational life with minimal maintenance. The filters can be customized with different filtration accuracy levels to meet specific industrial requirements.
To sum up, the Duplex filter, with its innovative design and superior performance, ensures uninterrupted workflow, enhances work efficiency, and reduces maintenance costs, making it an indispensable piece of equipment in several industries.

The Duplex Filter is composed of several key components with specific functions, each contributing to its overall performance and efficiency.
Housing - The housing is a robust frame that encloses all other components of the filter. It is typically made of strong and corrosion-resistant materials like stainless steel for durability and long service life. Housing is designed to withstand the pressure of the fluid and the operating environment.
Filter Baskets - The filter consists of two independent filter baskets. These are the main working parts of the filter where the actual filtration occurs. They trap and retain the solid impurities present in the fluid. The use of two baskets allows one to be serviced while the other remains in operation ensuring continuous filtration.
Switching Valve - The filter incorporates a switching valve mechanism that controls the fluid flow between the two filter baskets. When one of the filter baskets gets filled with impurities, the switching valve reroutes the fluid flow to the other filter basket, allowing for uninterrupted operation.
Seals and Gaskets - These components ensure that the filter is leak-proof. They are often made from reliable materials like rubber or silicone to resist temperature changes and chemical corrosion.
Inlet and Outlet Ports - These are the points where the fluid enters and exits the filter. The design and positioning of these ports ensure optimal fluid flow and minimize pressure losses.
Pressure Gauges - These gauges, usually located on the housing, indicate the pressure differential between the inlet and the outlet. This differential can be used to determine when a basket is full and needs to be replaced or cleaned.
Together, these components enable the Duplex Filter to maintain a continuous, reliable filtration process, extend the lifetime of equipment, enhance performance, and reduce operational costs.
The working principle of a Duplex Filter is unique as it offers a solution to maintain a continuous filtration process.
Initial Phase: In its initial state, the dirty fluid enters the Duplex Filter via the inlet pipe. The fluid is then routed to one of the two filter baskets. Which one is in use is determined by the position of the switching valve.
Filtration in Progress: When fluid is flowing through one of the filter baskets, the solid particles in the liquid are captured & retained, and the cleaned fluid flows out from the outlet.
Switching Procedure: During the filtration process, a differential pressure gauge, which measures the drop in pressure between the filter's inlet and outlet, monitors the filter's performance. When the pressure difference reaches a pre-set point, it indicates that the current filter basket is saturated with trapped particles and a switch to the other basket is required.
Auto-switching and Cleaning: The control mechanism then operates the switching valve, rerouting incoming fluid to the second filter basket, hence continuing the filtration process uninterrupted. Concurrently, the first filter basket can be taken out for cleaning, maintenance or replacement in a safe and dry condition, without needing to stop the entire operation.
Cycle Repeats: The cycle repeats when the second filter basket becomes full. The switching valve diverts the flow back to the now-clean first filter basket, and the second filter basket can be cleaned or replaced.
By employing this switchable dual-filter design, the Duplex Filter ensures a constant filtration process, eliminating the need for system shutdowns for maintenance, thereby enhancing productivity and improving overall system reliability.
The Duplex Filter is a valuable and essential tool in various industries due to its unique features and significant advantages.
Characteristics of a Duplex Filter:
Dual Filter Design: The defining feature of a Duplex Filter is its twin filter baskets, which make continuous operation possible.
High Capacity: Depending upon the size and specific model chosen, Duplex Filters can handle large volumes and high pressures of fluid.
Diverse Material Options: Housing and internal components can be made from various materials, tailored to specific operational needs or environmental conditions.
Manual or Automatic Switching: While most Duplex Filters feature a manual switching valve, some advanced versions feature an automatic switching system based on predetermined conditions.
Advantages of Using a Duplex Filter:
Continuous Operation: The most significant advantage of using a Duplex Filter is its uninterrupted filtration, critical in many industrial applications where a pause in operations can be costly.
Easy Maintenance: With a Duplex Filter, one filter basket can be taken offline for cleaning or replacement while the other continues to operate, thus reducing the downtime associated with maintenance.
Efficiency and Cost Savings: Continuous, efficient filtration prolongs the lifespan of the downstream equipment, reducing the need for frequent replacement or servicing. It saves both maintenance time and costs.
Versatility: With a variety of materials and sizes available, Duplex Filters can be used in many applications across several industries, including water treatment, oil and gas, food and beverage, chemical processing, and more.
The Duplex Filter, with its distinctive dual-basket design and advantages, proves to be a valuable asset in ensuring efficient uninterrupted operation in a range of industrial settings.
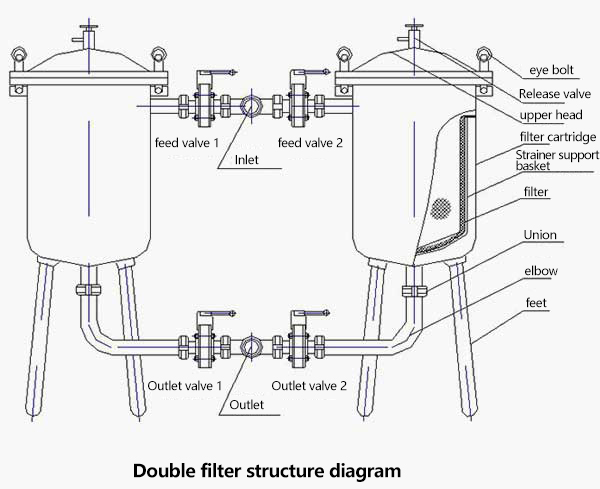
The technical parameters of Duplex Filters vary widely depending on the specific model and manufacturer. However, there are standardized parameters that universally apply. These include:
Filter Area: This refers to the total area available for filtration. A larger filter area provides a higher capacity for particle retention and hence, a longer filter life. The size selected will depend on the flow rate requirements.
Flow Rate: This parameter determines the volume of fluid that can be filtered per unit of time, and it is typically expressed in gallons per minute (GPM) or liters per minute (LPM). A high flow rate may result in lower filtration efficiency, therefore, it must be balanced with system requirements.
Operating Pressure: This is the maximum pressure at which the Duplex Filter can safely operate. It is typically expressed in pounds per square inch (PSI) or bar. A filter's operating pressure should be higher than the maximum pressure in the system.
Differential Pressure: This is the pressure difference between the inlet and outlet of the filter. An increase in this value generally indicates that the filter is becoming blocked and needs cleaning or replacement.
Filtration Rating: This is indicative of the filter's ability to retain specific sizes of particles, commonly expressed in micrometers or microns. Smaller micron ratings indicate finer filtration.
Material Composition: Duplex Filters can be made from a variety of materials including stainless steel, cast iron, carbon steel, bronze, etc. The selection depends on the fluid to be filtered and the environmental operating conditions.
Connection Size and Type: This relates to the size and type of the inlet and outlet connections of the filter (flanged, threaded, etc) and will be determined by the pipe size and type in your system.
These technical parameters combine to define the performance characteristics of the Duplex Filter. A clear understanding of these terms will help in the selection of the right Duplex Filter for specific industrial needs.
The choice of material for a Duplex Filter has a significant impact on its durability, performance, and ideal applications. Selection is often dictated by the properties of the fluid being filtered and the operating environment conditions. Here's a closer look at the impact of different materials:
Stainless Steel: Known for its strong resistance to corrosion, stainless steel is ideal for the filtration of fluids that may be corrosive. This material can also withstand high temperatures, making it suitable in hot process flows. However, stainless steel filters are usually more expensive.
Carbon Steel: Carbon steel has high strength and good wear resistance, making it a good choice for high-pressure environments. However, it is not as resistant to corrosion as stainless steel, so it is not the best option for corrosive fluids.
Cast Iron: Cast iron is a resilient material capable of withstanding rough operating conditions. While it offers good durability and cost-effectiveness, it lacks the corrosion resistance of stainless steel, making it less suitable for applications involving corrosive fluids.
Bronze: Bronze offers a favourable balance between resistance to corrosion and mechanical strength. It is a good choice for many general-purpose applications. However, it may not be suitable for very high pressures or temperatures.
Plastic: Some Duplex Filters are made from high-grade plastics. These are cost-effective options well-suited for low pressure and non-corrosive applications.
These are just a few examples of the materials commonly used in the manufacturing of Duplex Filters. It's important to bear in mind that various external factors such as ambient temperatures, pressures, mechanical stresses, and the nature of the filtered liquid all influence the material selected for a particular filter. Therefore, detailed knowledge of the application is crucial when making a selection. Always consult with filtration experts or the filter manufacturer to ensure the most suitable material is chosen for your specific needs.
Duplex filters, as a versatile industrial tool, come into play in coupling filtration tasks in a wide range of industries due to their effectiveness in processing large volumes of fluid without needing to halt for cleaning or filter element replacement. Here are some common applications:
Oil and Gas Industry: Duplex filters are regularly used in upstream, midstream, and downstream operations for the filtration of crude oil, natural gas, and other process fluids. They help reduce the presence of particulate matter that can cause equipment wear and tear.
Power Generation: In power plants, duplex filters are used to filter fuel oils, coolant oils, lubricants, and water used in various parts of the plant. They help ensure a smooth, efficient operation and reduced maintenance costs.
Chemical and Petrochemical Industry: These filters are applied in processing raw materials that need to be rid of impurities. They are also used to filter process fluids to guarantee product quality and prolong the lifecycle of other processing equipment.
Water Treatment: Duplex filters can be found in both industrial and municipal water treatment installations for the removal of particulates from wastewater before it is further treated or discharged.
Food and Beverage Industry: For the purposes of hygiene, safety, and process efficiency, duplex filters ensure that process water, raw ingredients, or finished products are free from unwanted particulates.
Maritime and Defense: Marine engines often use duplex filters for the filtration of fuel oil, lubricating oil, and seawater cooling systems. In military applications, they are used to filter fuels and other mission-critical fluids.
Manufacturing Industry: Whether it's the automotive, semiconductor, or textile industries, duplex filters find application in various manufacturing processes where pure filtrates are essential to guarantee product quality. They also protect machinery and reduces downtime.
In summary, duplex filters provide essential contributions wherever there’s a need to filter a large volume of fluids continuously with minimal interruption. Their capacity to switch from one filter to the other make them the choice for process-critical operations across diverse industries.
The role of Duplex Filters in the environmental sector is substantial and multifaceted. They contribute significantly towards ensuring cleaner and safer processes, and facilitating environmental protection measures. Here are a few key areas where their role is notable:
Water Treatment: The proper treatment of wastewater is crucial for protecting the environment from harmful pollutants. Duplex Filters come especially handy in industrial and municipal wastewater treatment plants, stripping the incoming wastewater of solid particulates before it undergoes further treatment. This ensures that no harmful particles are released back into the environment.
Emission Control: Many industrial facilities use Duplex Filters to remove particulates from their gaseous emissions. They help ensure the plant's emissions comply with environmental regulations and contribute to reducing air pollution.
Oil Spill Cleanup: In the unfortunate event of an oil spill, Duplex Filters can be used as a part of the cleanup processes. In an oil-water separation system, for example, the duplex filters can help to separate solid particulates from the oil, facilitating oil recovery and reducing environmental damage.
Recycling Processes: Many recycling plants, especially those dealing with plastic materials or waste oils, use Duplex Filters. They efficiently filter out contaminants, enabling the cleaner recycled output and reducing the environmental footprint of the production process.
Supporting Renewable Energy: In many biofuel production processes, particularly during feedstock preparation or final product purification, Duplex Filters ensure an efficient and clean flow, contributing to a more sustainable energy solution.
In summary, Duplex Filters, with their ability to filter out solid particulates from various types of fluids, play a significant role in the environmental industry. Their adaptive application aids in achieving cleaner processes, reducing environmental impact and promoting sustainability across industries. Hence, their use in the environmental sector is likely to increase in the coming years given the global emphasis on enhancing environmental conservation efforts.
Duplex Filters play a crucial role in the renewable energy sector, specifically in the preparation and purification stages of biofuel production.
Feedstock Preparation: Renewable energy sources, especially biofuels, are often produced from biomass, which can contain various kinds of impurities. These impurities can pose a significant challenge to the efficient production of biofuels. Duplex Filters play a critical role here by filtering out these impurities from the feedstock. The utilization of these filters maximizes the efficiency of the biofuel production process by ensuring that only clean, treated feedstock is sent for processing.
Biofuel Purification: After biofuels have been processed, they need to be purified before they can be used as a source of energy. Duplex Filters come in handy at this stage, helping to separate out any remaining impurities from the processed biofuels. This further improves the efficiency and effectiveness of biofuels as energy sources.
Reducing Downtime: One significant advantage of Duplex Filters is their dual basket design, which allows for the changeover of filter baskets without halting the process. This effectively reduces downtime in production processes, contributing substantially to boosting the productivity of renewable energy operations.
Sustainability: By making biofuel production processes more efficient and reducing waste, Duplex Filters also enhance the overall sustainability of renewable energy projects.
In essence, Duplex Filters are an integral part of the renewable energy sector. Their ability to ensure the quality and efficiency of biofuel production plays a significant role in supporting the implementation and scalability of renewable energy solutions. They continue to contribute to a more sustainable and green energy future.