Demineralized water equipment, often referred to as a demineralizer or deionizer, is designed to remove all minerals and salts from water through a process called ion exchange. Producing demineralized water is crucial for various commercial and industrial applications where the presence of these substances can affect product quality or equipment performance.
In essence, a demineralizer consists of at least two tanks: a cation exchange unit filled with negatively charged resin and an anion exchange unit filled with positively charged resin. As feed water passes through the cation exchange unit, positively charged ions such as calcium and magnesium are attracted to the resin, replacing them with hydrogen ions. The water then flows into the anion exchange unit where negatively charged ions like chloride and sulfate are replaced with hydroxide ions. These hydroxide and hydrogen ions subsequently combine to form pure water.
Demineralized water equipment offers a reliable solution for various industries such as pharmaceuticals, power generation, food and beverage, and cosmetics, where high purity water is essential. It also finds applications in laboratories for various forms of testing and research.
Key benefits of using demineralized water include protection of equipment from scale and corrosion, improved product quality in industries where purity of raw materials is essential, and enhanced efficiency in heating and cooling systems.
However, it's important to note that while demineralizers efficiently remove a wide range of minerals and salts, they do not remove most bacteria, dissolved organics, or particles. This means that in applications where these contaminants are of concern, demineralized water equipment often operates in conjunction with microfilters, ultrafilters, or reverse osmosis systems.
From a maintenance perspective, the efficiency of a demineralizer relies on the quality of the resins, which eventually need to be regenerated using acid for the cation resin and caustic soda for the anion resin. The frequency of this regeneration process depends on the water quality and the degree of demineralization required.
In conclusion, demineralized water equipment plays a pivotal role in various sectors, providing a robust and efficient solution to meet their high purity water needs.
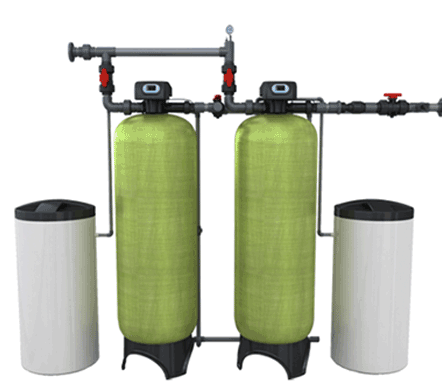
Demineralized water equipment, also known as Deionized water equipment, is used in a process that removes minerals and salts normally present in water. The operating principle of this equipment is based on the ion exchange process.
Water is passed through a column of ion exchange resins. The resins are small beads comprised of organic polymer chains that have charged functional groups built into the resin bead. There are two types of resins: Cation-exchange resins and Anion-exchange resins.
The Cation-exchange resins have negatively charged functional groups. These attract positive ions present in the water (like calcium, magnesium and sodium) and replace them with hydrogen ions.
On the other side, the Anion-exchange resins have positively charged functional groups. These attract negative ions present in the water (like chloride, sulfate and nitrate) and replace them with hydroxide ions.
The combination of hydrogen ions and hydroxide ions forms water molecules (H2O). Additionally, as all the negative and positive ions have been replaced from the water, the result is demineralized or deionized water, which is mostly pure with minimal mineral or salt content.
To continue this process efficiently, once the resins become saturated with ions, they need to be regenerated. The Cation resins are regenerated using Hydrochloric acid (HCl) and Anion resins are regenerated using Sodium Hydroxide (NaOH). These strong chemicals strip the accumulated ions from the resins, replenishing the resins' capacity to extract ions from the water.
This is a continuous process which ensures a consistent supply of pure, mineral-free water for various applications in industries such as power plants, pharmaceuticals, and food processing, among others.
Demineralized water equipment, also known as Deionized water equipment, is used in a process that removes minerals and salts normally present in water. The operating principle of this equipment is based on the ion exchange process.
Water is passed through a column of ion exchange resins. The resins are small beads comprised of organic polymer chains that have charged functional groups built into the resin bead. There are two types of resins: Cation-exchange resins and Anion-exchange resins.
The Cation-exchange resins have negatively charged functional groups. These attract positive ions present in the water (like calcium, magnesium and sodium) and replace them with hydrogen ions.
On the other side, the Anion-exchange resins have positively charged functional groups. These attract negative ions present in the water (like chloride, sulfate and nitrate) and replace them with hydroxide ions.
The combination of hydrogen ions and hydroxide ions forms water molecules (H2O). Additionally, as all the negative and positive ions have been replaced from the water, the result is demineralized or deionized water, which is mostly pure with minimal mineral or salt content.
To continue this process efficiently, once the resins become saturated with ions, they need to be regenerated. The Cation resins are regenerated using Hydrochloric acid (HCl) and Anion resins are regenerated using Sodium Hydroxide (NaOH). These strong chemicals strip the accumulated ions from the resins, replenishing the resins' capacity to extract ions from the water.
This is a continuous process which ensures a consistent supply of pure, mineral-free water for various applications in industries such as power plants, pharmaceuticals, and food processing, among others.
Demineralized water equipment or Deionized water equipment is a comprehensive system and each part of it plays a crucial role in producing purified water. Following are the main components of such equipment and their individual functions:
Pretreatment System: This is the first part of the demineralization process where raw water is pre-treated to remove suspended solids, organic materials and other impurities. Generally, it includes a filtration system (like sand filters or activated carbon filters), and a softening system to reduce water hardness. It ensures that the ion exchange resins are protected from fouling or premature exhaustion.
Deionizer Unit (Ion Exchange Column): This is the heart of the demineralized water equipment containing the ion exchange resins. It comprises of two types of resin columns: the cation exchange resin column and the anion exchange resin column. The cation column replaces positive ions in water (like calcium or magnesium) with hydrogen ions, while the anion column replaces negative ions (like chloride or sulfate) with hydroxide ions to form water molecules.
Chemical Dosing System: This part of the equipment is used for backwashing, regenerating, and disinfecting the pretreatment system and the ion exchange resins. It usually releases hydrochloric acid (for cation resins) and sodium hydroxide (for anion resins) to regenerate the exhausted resins, making them ready for the next cycle of ion exchange.
Control System: An advanced control system monitors the whole process. It schedules regeneration cycles, controls chemical dosing and flow rates, alarms for any malfunction, and ensures the finished water meets the required standards.
Storage and Distribution System: After purification, water is stored in water storage tanks and then distributed through a distribution system. These parts ensure a continuous supply of demineralized or deionized water whenever required.
Waste Disposal System: The system also includes a waste disposal mechanism to handle the concentrated waste stream produced during the regeneration process. This stream contains high levels of salts and acids or bases, and needs to be treated or disposed of responsibly.
In conclusion, Demineralized water equipment is a holistic system that brings together various processes and operations to achieve one aim, the production of high-quality, mineral-free water from raw, impure water.
These are general components and functions and may slightly vary depending on the specific design and requirements of the equipment.
Demineralized water equipment holds notable advantages that make it an essential fixture in many industries. Let's delve into the advantages and strengths of this equipment:
High-Quality Output: The primary advantage of demineralized water equipment is its ability to produce high-purity water. It effectively removes nearly all mineral ions such as cations like sodium, calcium, iron, and copper, and anions such as chloride and sulfate.
Wide Range of Applications: Deionized water produced by this equipment has a wide range of uses across diverse fields like pharmaceuticals, power plants, electronics, manufacturing industries, food and beverages industries, laboratories, and many more.
Preventative Measures: The use of demineralized water helps to prevent scaling and corrosion in boilers and heat exchangers, contributing to equipment longevity and reduced maintenance costs.
Cost-Effective Solution: Once installed, the operating cost of demineralized water equipment is relatively low compared to buying bottled deionized water. Furthermore, it provides a long-term solution for businesses that require a consistent and reliable supply of high-purity water.
Environmentally Friendly: The equipment operates on chemical ion exchange which does not produce harmful emissions. Furthermore, by treating water on-site, companies can reduce their carbon footprint from the transport of water supplies.
Flexibility: The system can be designed and scaled according to the specific needs and capacity requirements of a business, making it a highly adaptable solution.
Simple Maintenance: Typically, the maintenance for this equipment involves periodic regeneration of the resins using acid and alkali, which is a straightforward procedure.
Saves Energy: Demineralized water has excellent cooling properties. It is used as a coolant in many industrial processes, potentially saving energy by improving the efficiency of cooling systems.
It is important to note that while demineralized water equipment offers several benefits, it's crucial to conduct regular checks and maintenance to ensure the system keeps functioning optimally.
Yes, the relatively low operating cost of demineralized water equipment can also apply to small businesses. However, the feasibility and cost-effectiveness depend on several factors unique to each business.
Initially, the installation cost of a demineralization system may be somewhat high, as it involves investment in the equipment and its setup. Nonetheless, once installed, the cost to operate and maintain the system tends to be quite manageable.
The cost of chemicals for regeneration, maintenance labor, and power are the primary operational costs after installation. Comparatively, these recurring costs are often lower than purchasing bottled demineralized water, especially if the business has a consistent demand for high-purity water.
The real benefit for small businesses is the continuous availability of demineralized water when they need it, without having to depend on external suppliers. This can enhance operational efficiency and facilitate better planning and utilization of resources. Furthermore, small businesses can better control the quality of the water, ensuring it meets their specific requirements.
Still, it's important for small businesses to conduct a cost-benefit analysis before opting for an on-site water demineralization system. Depending on the scale of their operations and the extent of their need for high-purity water, alternative water purifying solutions might be more economically feasible. For instance, for very small-scale operations or occasional need for demineralized water, purchasing bottled water may still be the more cost-effective route.
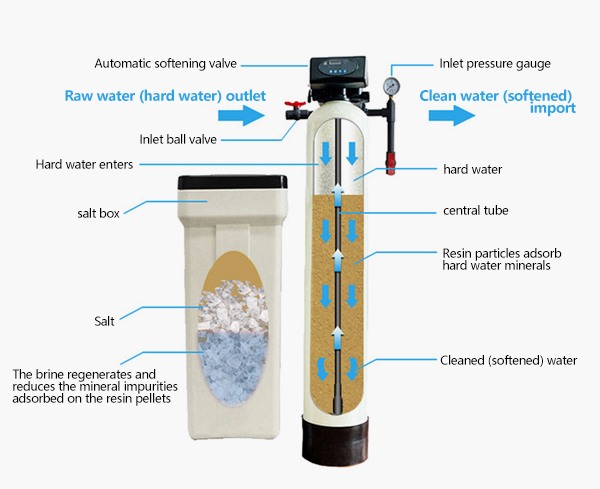
While the exact specifications and parameters can vary depending on the manufacturer and model of the demineralized water equipment, many systems share some common features. Here is an example of possible specifications and parameters of demineralized water equipment:
Model: Specific model names or numbers will depend on the manufacturer. For instance, Model eDM-5 is a type of demineralized water system.
Flow Rate: This parameter indicates the volume of water that the equipment can treat per unit of time. For instance, it can range from 50 to 80 liters per hour or more based on the system's capacity.
Space Requirement: The size of demineralized water equipment can vary widely. Some models are very compact, with space requirements of around 1m x 1m.
Power: Some models require no power, operating solely based on minimum inlet pressure which can be around 0.5 kg/cm2.
Output TDS (Total Dissolved Solids): This indicates the purity of the water produced. The output TDS is generally quite low, less than 10 for instance, indicating highly purified water.
Technology Used: Demineralized water equipment usually uses technologies such as ion exchange, electrodeionization, or membrane filtration technologies to remove mineral ions.
Capacity: The capacity of the equipment depends on its model and size. It can vary greatly, from handling a few liters per hour in small systems to thousands of liters per hour in industrial-grade systems.
It's important to note that when considering the purchase of such equipment, you need to consider the specific needs of your industry or application. You should also consult with a professional or the equipment manufacturer to ensure that the chosen equipment will meet your particular requirements.
Maintaining a demineralized water equipment system properly is crucial to ensure its efficiency and longevity. Here are some aspects that need to be considered when it comes to maintaining such systems:
Regular Cleaning: To prevent unwanted mineral build-up, ensure that the system is cleaned regularly. This also helps to maintain the cleanliness of the water.
Monitoring and Adjusting Parameters: It's vital to monitor key parameters such as pH, conductivity, and total dissolved solids (TDS). These parameters can indicate the performance of the system and help guide when adjustments are needed.
Preventive Maintenance: This includes regular inspections and performing tasks such as cleaning of control valves and verification of pressure gauges and flow meters. This proactive approach can prevent unexpected breakdowns and expensive repair costs in the future.
Seasonal Maintenance: Seasonal variations in water source quality may require adjustments to the system settings. Operators should be trained to understand seasonal variations in source water and adjust demineralization processes as needed.
Scheduled Resin Replacement: Ion-exchange resins, core to the demineralization process, do not last forever. Depending on the water quality and volume processed, you will eventually need to replace the resins. It's important to know when and how to do this.
Regular System Assessment: Constant performance assessment of the demineralization system is key to maintain efficiency. Services may include reviews of system controls, hardware examination, and process validation.
Professional Assistance: The system's complexity can sometimes require professional assistance for maintenance. Relying on experts for periodic inspection and maintenance can save costs associated with downtime or damaged components.
Remember, each device has its specific maintenance schedule and measures recommended by the manufacturer, which should be strictly adhered to for best results.
Demineralized water equipment is extensively used in various industries due to the purity of water it produces. These include, but are not limited to:
Power Generation Industry: Power plants often utilize demineralized water in steam turbines for producing electricity. The high purity of this water assures minimal damage to the equipment.
Pharmaceutical Industry: The pharmaceutical industry has stringent water quality standards. Demineralized water is commonly used in drug production processes, cleaning, and laboratory applications.
Healthcare and Hospitals: Demineralized water plays an essential role in maintaining high hygiene standards and equipment cleanliness in hospitals. This type of water is often used in sterilization processes.
Electronics Manufacturing: The electronics industry demands very high-purity water. Demineralized water is used in semiconductor manufacturing to rinse circuits and components, reducing the risk of contamination.
Food and Beverage Industry: In the food and beverage sector, demineralized water is often used to sanitize cooking vessels, processing machines, and other equipment to achieve food safety standards.
Chemical Industry: Demineralized water is used in various chemical manufacturing processes where high-purity water is required. It is often utilized in mixing and dilution processes in this industry.
Automobile Industry: Demineralized water is used in battery manufacturing and for the production of coolants and oils.
Laboratories: Research laboratories require high purity water for various applications, including chemical analysis, microbiological examinations, and various research activities.
Cosmetic Industry: Demineralized water is used in formulations for cosmetics and beauty products as it is free from unwanted minerals that might affect the quality or stability of the product.
Petrochemical and Refining Industries: High purity demineralized water is used in many processes in these industries such as chemical reactions and as a cooling agent.
The use of demineralized water equipment assures that the water used is free from unwanted minerals and other impurities. In many industries, this level of water purity is not just desirable, but essential for the successful and efficient operation of their processes.
Demineralized water equipment, also known as deionization equipment, plays an essential role in many industries when it comes to needing high-quality, mineral-free water. The procedure for installing and maintaining such equipment significantly depends on the specific model and design, but here are typical general steps:
Installation Process
Site Preparation: Choose an appropriate site for installation that can support the weight of equipment, and add any necessary support architecture.
Unpacking the System: Carefully remove the system and other components from their packaging and inspect for any possible damages occurred during transportation.
Equipment Placement: Position the equipment on the prepared site. Maintain adequate space at all sides for easy accessibility during maintenance.
Connecting Inlet and Outlet: Connect the system’s input to your water source and the output to your application. Be careful to connect the right pipes to the designated locations.
Electrical Connections: Ensure all electrical connections are carefully made to avoid any leakage or malfunctions. The power requirement may vary depending on the design of the system.
System Testing: Before full operation, conduct a system test to ensure all parts are functioning properly. Check for leaks and make sure all flows and pressures are within acceptable ranges.
Maintenance Routine
Regular Inspections: Conduct periodic inspections to detect any early signs of damage or malfunction in the system. This includes checking the pressure gauge, control valves, and other parts.
Monitoring Key Parameters: Regularly monitor important parameters, such as the pH, conductivity and TDS (Total Dissolved Solids). These can indicate system performance and help identify when adjustments or cleanings are needed.
Cleanliness: Ensure that the equipment and its components are cleaned at regular intervals. This aids in preventing mineral build-up and in maintaining the quality of the produced water.
Resin Replacement: Depending on the water quality and volume processed, the ion-exchange resins will eventually need replacement. It's crucial to be knowledgeable of the signs that indicate replacement is needed, and to know how to replace them properly.
Professional Check-ups: For complex systems, professionals should be brought in periodically for a more thorough examination. This can help maintain the system function optimally and avoid potential downtime caused by unexpected failures.
Documentation: Keep a log of maintenance activities, system performance metrics, and any issue noted. This helps in maintaining a consistent schedule and detecting patterns of recurring problems.
Adhering to a sound maintenance routine and conducting regular checks ensures the longevity, optimal functionality, and reliability of the demineralized water equipment.