Ultrafiltration equipment is designed to purify and separate substances in a liquid mixture. It utilizes ultrafiltration, a membrane filtration process which separates particles based on size. Through the usage of a semipermeable membrane, it can effectively remove particles, macromolecules, and substances from water that can't be eliminated using traditional filtration processes.
The design of ultrafiltration equipment is tailored to cater for various applications across many sectors. These sectors include the pharmaceutical industry, the food and beverage industry, the chemical industry and water treatment facilities.
Key components of ultrafiltration equipment include the ultrafiltration module, a pump to ensure water pressure, and a controller to monitor and control the equipment’s operation. The equipment's performance can be highly efficient due to the advancements in technology, leading to a high removal rate of substances, excellent filtrate quality, and a long lifespan of the membrane.
Ultrafiltration equipment offers various advantages such as: low energy consumption, easy operation and maintenance, and being environmentally friendly due to it not requiring chemicals for operation.
In conclusion, ultrafiltration equipment plays a vital role in industries that require precise and efficient filtration processes. Its design and advantages make it preferable for many applications, contributing towards safer and purer products and end-results.

Working Principle of Ultrafiltration Equipment
The fundamental working principle of ultrafiltration equipment centers around the concept of membrane filtration. It utilizes a semipermeable membrane to separate particles and substances based on their size.
The process begins when the mixture to be filtered is pressurized and passed over the ultrafiltration membrane. This membrane is composed of microscopic pores that allow the flow of water molecules and smaller particles while preventing larger particles, colloids, and macromolecules from passing through.
The driving force behind this separation process is pressure. By applying pressure on the feed solution, water and dissolved solutes with smaller molecular weight are able to cross the membrane and get collected as permeate. Substances with a molecular weight larger than the membrane's cut-off, such as bacteria, viruses, and high molecular weight solutes, are retained on the membrane surface or within the membrane's pores. They get collected as retentate or concentrate.
The major advantage of this process is its selectivity, determined by the membrane pore size. A user has the flexibility to choose the membrane according to the degree of filtration required.
It is also important to note that the ultrafiltration process does not involve any phase transition, which implies that it operates at relatively low temperatures, making it suitable for heat-sensitive materials.
In brief, ultrafiltration equipment leverages the concept of membrane filtration under pressure to achieve the effective separation of substances, delivering high-quality filtration results.
Impact of Membrane Choice on Ultrafiltration Results
The selection of the membrane in ultrafiltration equipment is pivotal to the effectiveness of filtration and the overall quality of the outcome. The key factors to consider when choosing a membrane include its pore size, material, and surface properties.
Pore Size: Pore size is a crucial factor in determining what substances the membrane will separate. Larger pore sizes allow for higher flow rates but less specific separation, whereas smaller pores enable more precise separation but at a slower rate. Selecting the correct pore size ensures that you are filtering out the desired particles while allowing the required substances to filter through.
Material: The material of the membrane can impact its durability, chemical resistance, and compatibility with the mixture being filtered. Some materials may react with particular solutes, altering the filtration results. Therefore, it's essential to choose a membrane material appropriate for the specific substance being filtered.
Surface Properties: This includes hydrophobicity or hydrophilicity and charge properties of the membrane surface. Hydrophilic membranes tend to have lower fouling tendencies and are beneficial for filtering biological compounds that could build up on the membrane's surface. In some applications, charged membranes can enhance the separation process by rejecting co-ions and selectively passing counterions.
In conclusion, the selection of the membrane in ultrafiltration equipment is instrumental in achieving optimal filtration performance. It is important to take into consideration the specific requirements of the task in order to choose the most suitable membrane. This decision will directly impact the effectiveness of separation, speed of filtration, and the quality of the end result.
Components and Functionality of Ultrafiltration Equipment
Ultrafiltration equipment is mainly composed of several key parts working in unison to facilitate the filtration process. Below are the main components and their respective functions:
Feed Pump: The feed pump is responsible for applying pressure to the feed solution, which forces it against the surface of the membrane. The amount of pressure applied determines the rate at which the filtration process takes place.
Filtration Chamber: The filtration chamber houses the membranes used for ultrafiltration. It is usually designed to withstand high pressure, and it's where the actual filtration process takes place.
Membrane Module: This consists of the ultrafiltration membrane itself. The selected membrane is typically a thin layer of material with a specific pore size that allows only particles of a certain size to pass through.
Pressure Gauge: This is used to monitor the pressure applied to the feed solution. It is essential to ensure that the pressure remains within the optimal range for effective filtration.
Retentate and Permeate Outlets: The retentate outlet is where the unfiltered solution (containing particles too large to pass through the membrane) is expelled from the system. The permeate outlet, on the other hand, is where the filtered solution (particles that have passed through the membrane) exits the system.
Backwash and Cleaning System: Backwash function helps to remove fouling from the membrane surface, thus increasing its lifespan and efficiency. The cleaning system is used to cleanse the membrane periodically, ensuring the ultrafiltration equipment continues to function optimally.
Control System: This component helps in monitoring and controlling the operation of the ultrafiltration equipment. It may include sensors for measuring pressure, flow rate, and temperature, and controls for adjusting these parameters.
In conclusion, the ultrafiltration equipment's core function is to separate particles from a solution based on their size. From applying the necessary pressure to managing the filtered and unfiltered solutions, every key component of an ultrafiltration system plays a vital role in ensuring the system's efficiency and effectiveness. To ensure long-term efficient operation, maintenance and cleaning of the components are equally vital.
The Role of a Cleaning System in Maintaining the Efficiency of Ultrafiltration Equipment
The cleaning system within ultrafiltration equipment is crucial for its long-term efficient operation. This system is responsible for removing the buildup of particles or substances that adhere to the membrane surface over time, a phenomenon known as fouling. This build-up can affect the membrane's permeability and reduce the overall performance of the ultrafiltration equipment.
The cleaning system generally operates in two modes: backwashing and chemical cleaning.
Backwashing: This is a regular cleaning process executed after certain intervals, typically when the trans-membrane pressure reaches a threshold value indicating significant fouling. In this process, permeate is forced back through the membrane in the direction opposite to the standard filtration flow. This action dislodges deposited contaminants on the membrane surface, restoring the membrane's permeability and filtration capacity.
Chemical Cleaning: This is performed less frequently than backwashing, usually when the backwash cycles are incapable of restoring the membrane's performance. During chemical cleaning, cleaning agents are used to dissolve stubborn fouling substances that backwashing cannot remove. The type of cleaning agents used depends on the nature of the fouling materials and the membrane's chemical compatibility.
Through these processes, the cleaning system ensures the membrane retains its initial operational parameters such as flux, pressure, and rejection rate, ultimately maintaining the device's overall efficiency and longevity of service. Regular maintenance and timely cleaning should be performed to ensure that the ultrafiltration equipment continues to deliver optimal performance.
In conclusion, an efficient cleaning system in ultrafiltration equipment is indispensable for mitigating membrane fouling, thereby ensuring the system's high operational efficiency. Regular monitoring, backwashing, and more thorough chemical cleanses help to maintain the ultrafiltration equipment's filtration capacity and prolong its useful life.
Advantages and Benefits of Ultrafiltration Equipment
Ultrafiltration equipment offers a variety of significant advantages for numerous industries, especially pertaining to water purification, wastewater treatment, and various process separations in the food and beverage industry. Here are the main advantages and benefits of using ultrafiltration equipment:
High Removal Efficiency: Ultrafiltration equipment can effectively remove most particulate matter, bacteria, viruses, and even high molecular weight dissolved organics owing to the small pore size of the membrane. This ensures that the resulting filtered fluid is of high quality and purity.
Energy Efficiency: As a pressure-driven process, ultrafiltration uses less energy compared to other separation technologies such as evaporation methods and offers a cost-effective means of filtration with lower running costs.
Versatility: Ultrafiltration equipment can be deployed in a wide range of applications ranging from industrial waste treatment to pharmaceutical production and potable water purification. This not only highlights its versatility but also increases its adaptability in different industrial settings.
Environmentally Friendly: Ultrafiltration doesn't involve the use of harmful chemicals, making it an environmentally friendly purification method. The process reduces environmental pollution, ensuring environmental sustainability.
Compact Design: Ultrafiltration systems have compact designs that occupy less space and ease installation. They can be integrated seamlessly into existing plants due to their modular nature and flexibility in configuration.
Continuous Operation and Automation: With rigorous but routine maintenance, ultrafiltration systems can function continuously for extended periods. Also, they can be automated, which reduces the need for constant monitoring and human intervention, thereby reducing labor costs.
Scalability: Ultrafiltration systems are designed to be scale-up or scale-down according to the required degree of filtration and system's capacity. This attribute makes ultrafiltration a feasible choice for both small-scale and large-scale applications.
In conclusion, ultrafiltration equipment provides valuable benefits, including energy and cost efficiency, versatile applications, an eco-friendly approach, compactness, continuous operation, and scalability. These advantages make it an attractive option for many industries looking for efficient and effective separation processes.
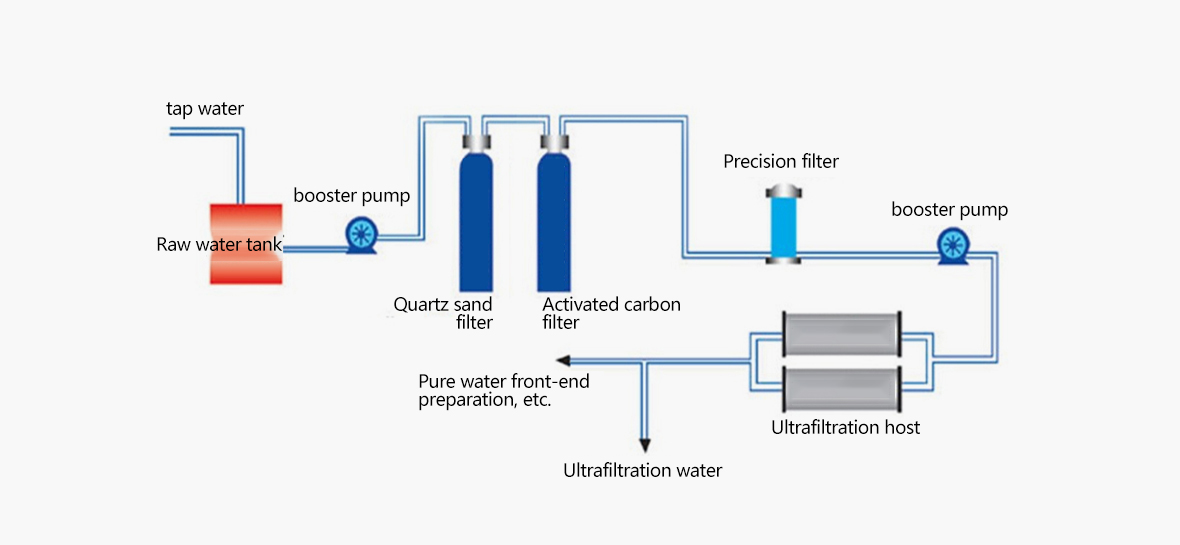
Technical Specifications and Parameters of Ultrafiltration Equipment
Technical specifications and key parameters of ultrafiltration equipment are crucial determinants of its performance and applicability in various industries. The following aspects cover a comprehensive view of the technical specifications and parameters involved:
Membrane Material: The material of the ultrafiltration membrane can vary, including polymeric such as polysulfone, polyethersulfone, and ceramics. Each offers different resistance to chemicals, temperature, and pollutants.
Pore Size: The pores of ultrafiltration membranes typically range in size from 0.1 to 0.01 micrometers. Smaller pore sizes can effectively remove more contaminants, but at the expense of slower filtration rates.
Trans-Membrane Pressure (TMP): This is the average pressure driving the filtration process. Typical values range between 1 and 3 bar, and it's directly proportional to the flow rate of the permeate.
Flux: This refers to the rate at which permeate passes through the membrane per unit area and unit pressure. It is an essential parameter for evaluating the efficiency of the membrane filtration process.
Recovery Rate: This indicates the percentage of the feed water that is converted into filtered water or permeate. A high recovery rate ensures less wastage and cost-effective operation.
Feed Water Quality: The quality of the incoming feed water greatly influences the performance of the ultrafiltration system. Parameters like Turbidity, Total Dissolved Solids (TDS), and microbial content can affect membrane fouling and the overall system efficiency.
Operational Temperature: Each membrane material has a specific temperature range within which it can operate. Usually, common polymeric membranes operate within a temperature range of 5-50 °C.
Cleaning & Maintenance: The frequency of backwashing and chemical cleaning required for the equipment often depends on factors such as feed water composition, operating pressure, and temperature.
System Configuration: Ultrafiltration systems can be designed in different configurations such as dead-end or crossflow mode, based on the feed water quality and application requirements.
It is essential to bear in mind that specific requirements for ultrafiltration processes differ depending on their application, hence the need to consider equipment parameters individually, respective to each industry's demands. Careful consideration and balancing of these parameters can result in an optimized, efficient ultrafiltration system.
Applications of Ultrafiltration Equipment across Various Industries
Ultrafiltration equipment has diverse applications across different sectors due to its versatile nature. Here's a comprehensive breakdown of its usage across notable industries:
Water and Wastewater Treatment: Ultrafiltration is commonly used to remove suspended solids, bacteria, viruses, and other particulates from water and wastewater. It serves as a pre-treatment step in the desalination process and can be used in both municipal water treatment and industrial wastewater treatment settings to produce high-quality effluent.
Food and Beverage: In the dairy industry, ultrafiltration is used for milk concentration and cheese whey processing. It's also employed in fruit juice production for clarity improvement and removal of bacteria, yeast, and enzymes, ensuring the juice is safe for consumption. Additionally, it is used in the wine and beer industry to achieve product stability and shelf life extension.
Pharmaceutical Industry: Ultrafiltration is used for protein concentration, antibiotics purification, and virus removal. The sterility of pharmaceutical products is essential, and ultrafiltration serves as an effective method to achieve this.
Chemical industry: Ultrafiltration systems have uses in paint recovery, in recirculating water from rinse tanks, in recovering precious metals from electroplating solutions and in the separation, concentration, and purification of various chemicals.
Electronics: In electronics and semiconductor manufacturing, ultrapure water is necessary. Ultrafiltration is used as a pre-treatment method to remove contaminants before the water undergoes reverse osmosis or deionization, providing the high purity level needed.
Power Generation: Ultrafiltration is used as a pre-treatment step for boiler feed water in thermal power plants, where it helps in reducing the load on downstream demineralization processes, thereby improving plant efficiency.
Textiles: Ultrafiltration units have a role in treating effluent generated in textile industries that is typically loaded with high concentrations of dyes and organic compounds, making it challenging to treat.
In conclusion, due to its versatile and efficient nature, ultrafiltration equipment finds applications in diverse industries, ranging from water treatment and food processing to pharmaceutical, chemical, electronics, power generation, and textile industries. The adaptability of these systems shows their practicality and necessity across numerous sectors.
Installation and Maintenance of Ultrafiltration Equipment
To ensure optimal performance of ultrafiltration equipment, a meticulous and correct installation process is essential, followed by regular and effective maintenance. Here's an in-depth guide.
Installation:
Site Selection: Choose a site that is protected from direct sunlight, frost, rainfall, and extreme weather conditions. Sufficient space should be available for easy access to the machine for maintenance and service.
Pre-Installation Checks: Inspect the equipment and parts for any transit damage before installation. Any identified issue should be addressed before proceeding with installation.
Connection to Feed Source: Connect the equipment to the water source after ensuring that the feed water meets the specified standards in terms of turbidity, TDS, etc.
System Assembly: Follow the user-manual provided by your manufacturer for system assembly. Different types and brands can have slightly different assembly instructions, and this should be done with caution to prevent damage.
Start-Up: After proper assembly, gradually initiate the system according to the manual. Monitor the system closely for any leaks or unexpected irregularities during the initial phase.
Maintenance:
Regular Cleaning/ Backwashing: Regularly scheduled cleaning, typically involving backwashing, is recommended to prevent membrane fouling. The frequency of cleaning depends on the system and feed water quality.
Chemical Cleaning: Over time, some particulates may accumulate on the membrane that cannot be removed by backwashing alone. Chemical cleaning should be carried out periodically using appropriate cleaning agents based on manufacturer guidance.
System Monitoring: Monitor system parameters like flowrate, pressure, and performance regularly to track any changes. This would help in identifying issues promptly and implementing remedial actions.
Replacement: Membrane elements and some other parts of the system will wear with time and need replacement. Replacement intervals must be strictly followed to prevent system performance degradation.
Troubleshooting: In case of system irregularities, professional assistance or a thorough check-up of the system may be necessary. Operators should have a basic understanding of common problems and in-house troubleshooting should be encouraged before escalating problems to the supplier or OEM.
Demonstrating a great understanding of your ultrafiltration system and offering it the required care will promote system continuity and potentially extend its lifespan. Understanding the critical processes and the associated components is the first step towards achieving this.