A cartridge dust collector is a highly efficient industrial dust management system that employs a cartridge as a filtration unit. Its primary role is to accumulate and segregate dust and other particulates from a variety of industrial environments. Offering a high filtration aftereffect and quick, hassle-free maintenance, the cartridge dust collector has become a favorite among industries seeking efficient and cost-effective dust management solutions.
The cartridge in these dust collectors is typically made of a pleated, non-woven, polyester-based media. This pleated design allows for a greater filtration surface area compared to conventional bag filters, resulting in higher filtration efficiency and less frequent filter replacements.
The operational principle of a cartridge dust collector is relatively straightforward. Dust-laden air is drawn into the collector, where heavier dust particles are immediately forced down into a collection bin due to gravity and inertia. The air then passes through the cartridge filter where the smaller particles are caught and accumulated. The clean air is then discharged back into the environment.
Another distinguishing feature of cartridge dust collectors is their self-cleaning mechanism. Many designs use a pulse-jet cleaning system, which uses short bursts of compressed air to dislodge accumulated dust from the cartridge surface, dropping it into the collection bin for hassle-free disposal. This self-cleaning feature extends the lifespan of the cartridge and enhances overall operational efficiency.
Cartridge dust collectors are highly versatile and can be used in a variety of industries, from metalworking and woodworking to food processing, pharmaceuticals, and more. They are especially popular in applications where high-efficiency filtration is necessary or where dust loading is high.
To sum up, a cartridge dust collector is a key asset for industries aiming to achieve superior dust control, efficient operation, and a safe and clean working environment.
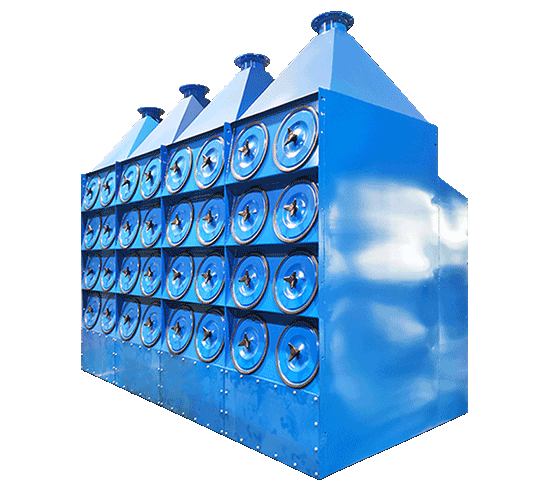
A cartridge dust collector is a vital piece of equipment for maintaining air quality in various industrial environments. Here's an in-depth look at how these innovative systems work:
Dusty Air Ingestion: The process begins when the dust-filled air is sucked into the inlet of the dust collector. This air could be drawn from a dedicated system, a specific process, or it might be ambient air from the overall environment.
Particle Separation: Once inside, the air is subjected to a reduction in velocity. As the speed of the air slows down, larger dust particles lose momentum and due to gravity, they fall into the dust bin or hopper located at the bottom of the collector. This process is known as inertial separation and takes care of a significant proportion of the coarser dust particles.
Cartridge Filtration: The still dusty air then reaches the cartridge filters. These filters are typically constructed from pleated, non-woven fabric designed to trap fine dust particles that managed to pass through the previous stage. As the air moves through these filters, the fine dust particles get caught in the fabric folds, while the cleansed air continues to move through.
Clean Air Discharge: After the air has been filtered, it is returned to the environment or recirculated within the facility. In some cases, it may go through an additional stage of filtration, especially if the collector is being used in industries where hyper-clean air is required, like pharmaceuticals or electronics.
Pulse-jet Cleaning: To ensure the longevity and efficacy of the cartridge filters, most cartridge dust collectors include a self-cleaning feature. A common type of cleaning mechanism is pulse-jet cleaning. In this system, short bursts of compressed air are periodically fired through the filters, dislodging accumulated dust and causing it to fall into the dust collection bin. This ensures that the filters remain unblocked so that the system's performance is consistently maintained over time.
This step-by-step process allows cartridge dust collectors to efficiently remove particulates from the air, ensuring that the air quality within industrial environments is kept clean and safe for employees and the machinery in operation. It's worth noting that the precise sequence of steps could vary between different models and makes of cartridge dust collectors, but the basic principles remain the same.
A cartridge dust collector is a powerful industrial tool, designed to filter and purify the air in a variety of manufacturing settings. It is composed of several key components, each playing a significant role in the process. Here's a breakdown of these parts and their respective functions:
Inlet: This is where the dust-laden air enters the dust collector. Depending on the design, the system may have one or multiple inlets to accommodate different volumes and sources of dusty air.
Body Shell: The body or shell of the cartridge dust collector is the main structure that houses internally all other components. It's typically built from durable materials like steel to withstand industrial conditions and pressures.
Dust Hopper: Located at the lower part of the dust collector, the dust hopper serves as a reservoir for the collected dust particles. It is generally sloped towards the bottom, facilitating the movement of the particles towards the disposal system.
Disposal System: This is typically a dust drum or a rotary airlock that is located under the hopper. Its role is to allow the removal of the dust particles from the system without letting outside air infiltrate it.
Cartridge Filters: These are the heart of the dust collector system. Usually cylindrical and made from pleated, non-woven fabric, they serve to trap and hold the dust particles as the air moves through them. They are significantly more efficient in dust collection than traditional filters due to the higher surface area they offer.
Cleaning System: Many cartridge dust collectors feature an automatic cleaning system to maintain the functionality of the filters. The most common type is a pulse-jet cleaning system that emits bursts of compressed air, dislodging dust from the filter surfaces.
Outlet: This is the exit path for the air after it has been filtered. The cleaned air is typically returned to the environment or recirculated within the industrial facility.
Control System: This is the brain of the dust collector. It regulates the operation of the entire system, including starting and stopping the fan motor and triggering the cleaning system. Many control systems are now digitally enabled, offering real-time monitoring and adjustment capabilities.
Together, these components work in harmony to ensure the cartridge dust collector effectively removes dust and other particulates from the air, contributing to healthier, safer, and more productive industrial environments.
A cartridge dust collector is a preferred choice for air filtration in many manufacturing and industrial environments due to its unique design and numerous advantages. Let's delve into the key benefits and distinctive qualities that these systems offer.
High Filtration Efficiency: The most notable advantage of cartridge dust collectors is their high filtration efficiency. The cartridge design incorporates pleated, non-woven fabric that provides a larger surface area compared to traditional filters. Hence, they can trap more dust particles, including fine dust, resulting in better air quality.
Space-Saving Design: The compact size and design of a cartridge dust collector make it a suitable choice for facilities with space constraints. Although they are smaller, they offer similar or even higher dust collection capacity compared to conventional dust collectors.
Easy to Maintain: The cartridge filters are typically easy to replace, requiring minimal downtime. Furthermore, many cartridge dust collectors feature a self-cleaning system which helps to extend the life cycle of the filters and reduces maintenance efforts.
Energy Efficient: The design of the cartridge dust collector allows for effective and efficient operation. The use of pulse-jet cleaning reduces energy costs associated with continuous air pressure systems used in other types of collectors.
Versatility: Cartridge dust collectors are versatile and can be used in various industries like metalworking, woodworking, pharmaceuticals, food processing, and more. They can handle different types of dust, including toxic and combustible dust.
Customizable: Many manufacturers offer custom-built cartridge dust collectors. This means you can have a system made specifically for your needs, considering factors like dust type, volume, available space, and desired air quality.
Improved Worker Health and Safety: By efficiently removing dust and other potential pollutants from the air, cartridge dust collectors contribute to healthier and safer work environments. This could lead to improved productivity and decreased health-related absences.
Environmental Compliance: With increasingly stringent regulations on industrial emissions, using a high-efficiency dust collector like the cartridge model helps businesses meet environmental standards and avoid potential fines or legal complications.
In conclusion, a cartridge dust collector offers features and benefits that make it a superior choice for businesses requiring efficient and cost-effective air filtration solutions. Its design, performance, and versatility make it a sound investment for maintaining clean, safe, and compliant industrial operations.
When selecting a cartridge dust collector for an industrial environment, it's crucial to understand the technical parameters and specifications associated with the equipment. Note that these parameters can vary significantly depending on the model and manufacturer. Here's a general look at some key technical specifications you might encounter:
Airflow/Capacity: Measured in cubic feet per minute (CFM), this indicates the volume of air that the dust collector can process within a minute. Depending on the facility's requirements, this can range from a few hundred to several thousand CFMs.
Filter Area: This is the total surface area of the cartridge filters within the collector, typically measured in square feet. A larger filter area translates to more dust collection capacity.
Filtration Efficiency: Expressed as a percentage, this shows how effectively the dust collector can remove dust particles from the air. Higher efficiency values indicate that the collector can remove a greater number of small particles.
Dust Load: Denoted in grains per cubic foot (gr/ft³), it signifies the amount of dust in the air input to the dust collector. It's important to note this when selecting a dust collector as more dust load requires a system with a higher capacity.
Static Pressure: Measured in inches of water column (in. w.g.), this figure represents the resistance to airflow in the dust collector system. Understanding the static pressure can help in selecting the right fan and motor for the dust collector.
Power Requirements: This refers to the electrical requirements needed to operate the dust collector. It includes aspects such as voltage, frequency, and phase.
Disposal System Capacity: This indicates the volume of dust that can be collected before the disposal system (dust bin or drum) needs to be emptied.
Noise Level: Given in decibels (dB), this value portrays how loud the dust collector operates. This is especially important when considering worker comfort and safety regulations.
Dimensions and Weight: The physical size and weight of the dust collector can affect where it can be installed and how easy it is to transport or move.
Material and Construction: This specifies the materials used to construct the dust collector and its resistance to various environmental conditions, impacts, or corrosion.
Remember, every application has unique demands and these specifications should be tailored accordingly. Consulting with a manufacturer or industry expert can be highly beneficial when evaluating these technical parameters for a cartridge dust collector.
The filter area of a cartridge dust collector significantly impacts its dust collection capability. Here's a detailed look at how the filter area influences the dust collecting performance in English.
Efficiency: A larger filter area allows for more efficient dust collection. The more surface area available on the filter, the more dust particles it can trap at a given time, leading to improved overall efficiency in dust collection.
Longer Operational Time: With increased filter surface area, there is more space for dust to accumulate before reaching filter saturation. This means that the dust collector can operate for longer periods before requiring filter cleaning or replacement.
Lower Air-to-Cloth Ratio: A larger filter area results in a lower air-to-cloth ratio, which in turn can result in increased particle removal efficiency. A lower air-to-cloth ratio means the volume of air per unit of filter material is reduced, allowing the filter to capture more particles effectively.
Slower Filter Clogging: Filters with larger surface areas take longer to clog because it takes more time for enough dust particles to accumulate and block the filter's surface.
Cleaner Air: A bigger filter area essentially implies a greater capacity to capture dust particles, leading to cleaner air output from the dust collector.
Less Strain on the System: When a filter has a larger surface area, it allows for better airflow with less resistance, reducing the strain on the system's fan and motor and leading to potentially longer equipment life.
Enhanced Pulse Cleaning: In self-cleaning dust collectors, a larger filter surface area provides a better response to pulse cleaning. This means that the filter can be cleaned more effectively, extending its life and improving the overall performance of the dust collector.
In brief, the filter area of a cartridge dust collector plays a critical role in the system's dust collection effectiveness. It can affect the efficiency, running time, maintenance frequency, system longevity, and overall performance of the dust collector.
Cartridge dust collectors are versatile air pollution control devices that find applications across a broad spectrum of industries. They are crucial in environments where airborne dust, fumes, or particulate matters are generated and need to be removed swiftly and efficiently. Below are some industries where cartridge dust collectors are applied:
Manufacturing Industry: Within various manufacturing settings such as metalworking, woodworking, plastic, and chemical production, significant amounts of dust and particulates are generated. These can quickly lead to an unsafe working environment. Cartridge dust collectors are used extensively to clear the air and maintain air quality standards.
Pharmaceutical Industry: In pharmaceutical manufacturing, where product purity and cleanliness are critical, cartridge dust collectors help eliminate dust and particulate matter. They are also used to control potent and toxic compounds during tablet production or powder filling processes.
Food and Beverage Industry: Dust collectors play a crucial role in maintaining a safe and sanitary production environment. They collect flour, sugar, spice, and other food-related dust, ensuring the workplace cleanliness and protecting the quality of food products.
Electronics Industry: Soldering, laser marking, and various electronics manufacturing processes often produce fumes and fine dust. Cartridge dust collectors are employed to improve air quality and protect sensitive equipment from contamination.
Automotive & Aerospace Industry: These sectors utilize cartridge dust collectors in processes like sanding, blasting, welding, and painting where dust and fumes are generated. It helps protect workers and meet regulatory requirements.
Mining Industry: Mining and quarrying processes can generate large amounts of airborne particulate matter. Dust collectors reduce this dust significantly, improving air quality around these operations.
Energy & Power Industry: In coal-fired power plants, cartridge collectors are commonly used as part of the fly ash collection systems. Also, in the production of renewable energy like biomass power generation, dust collectors are used.
Construction Industry: Construction activities like drilling, cutting, and sanding could generate significant dust. Dust collectors help keep these work sites cleaner and safer.
Agricultural Industry: Agricultural processes like grain handling and milling could release substantial amounts of dust. This industry uses cartridge dust collectors to help reduce this dust and improve the safety and health of agricultural workers.
These are just a few examples of the diverse roles cartridge dust collectors play in many industries, ensuring cleaner, safer air and more efficient work environments. Their adaptability and efficiency in dust and fume extraction make them an ideal choice across sectors.
In the mining industry, cartridge dust collectors play a vital role in managing and reducing airborne particulate matter. Here's a detailed explanation of how cartridge dust collectors work to minimize dust particles in the air in the mining sector:
Dust Generation: During mining operations, substantial amounts of dust and particulates are generated from drilling, blasting, crushing, and loading activities. The generated dust includes elements dangerous to health, such as silica.
Dust Capture: Cartridge dust collectors are strategically placed at the sources of dust generation. The collectors use powerful fans to draw in dust-laden air from the mining operations.
Filtration: The dust laden air is then directed towards the cartridge filters. These cartridges contain various layers of specially engineered filter media that capture dust particles while allowing clean air to pass through. The layered media creates a tortuous path for the air to flow, trapping even the smallest dust particles in the process.
Cleaning and Disposal: Over time, the filters start to clog with dust particles, affecting the efficiency of the dust collector. To maintain efficiency, these cartridge filters are periodically cleaned using a pulse-jet cleaning system. The pulse-jet system releases a quick, high-pressure burst of air, dislodging the dust particles from the filters.
Maintenance: The dust particles dislodged from the filters are collected in a dust drawer or bin for safe disposal. It is a practice to replace cartridge filters periodically to ensure the system's optimal dust collection efficiency is maintained.
Air Return: The air free of dust particles is then either released into the environment or returned to the inside space, significantly reducing the overall particulate matter in the workspace's air.
By continuously filtering out dust and particulates from the air, cartridge dust collectors play a vital role in enhancing the quality of air in the mining area. They contribute significantly to maintaining compliance with health and safety regulations, protecting workers, and reducing environmental impact.