The Natural Gas Filter Element is an integral part in maintaining a clean and seamless flow of natural gas in various applications. Specifically, this element is responsible for sieving out particulates like dust, dirt, or other impurities inherently present in natural gas. The enduring role it plays in gas pipelines and equipment cannot be understated; it's designed to safeguard the optimal operation of downstream machinery, warding off potential malfunctions or damages that excessive contaminants may potentially cause.
Constructed with extraordinary precision from premium quality materials such as stainless steel or anodized aluminium, Natural Gas Filter Elements are designed to withstand the harsh pressures and temperature variations that are so often synonymous with the processes of natural gas extraction and transportation. Moreover, their high level of efficiency means they also protect machinery from damages due to impurities, ensuring a longer life span for the equipment and reducing the frequency of maintenance or servicing needs.
Their inclusion is instrumental across a myriad of natural gas based applications encompassing pipelines, power plants, gas lift studies, compressor stations and gas gathering systems, to name a few.
In essence, the Natural Gas Filter Element acts as a sentinel for multiple gas-infrastructure and operations, and its vital contributions extend from safeguarding individual machinery to ensuring the overall quality of natural gas that is used across a wide spectrum of industrial and residential applications.

The working principle of a Natural Gas Filter Element operates on the crux of separation and filtration, facilitating the extraction of purified natural gas free from contaminants that could potentially impair the functioning of hardware or diminish the quality of the end product.
When natural gas, holding an assortment of impurities like dust, dirt, and oil particles, is introduced into the system, it first encounters the Natural Gas Filter Element. The construction of the filter element, commonly involving layers of fine wire mesh or synthetic filter media, allows the gas to pass through while obstructing the larger and smaller contaminant particles.
This process is often referred to as surface filtration where particles larger than the chosen filter pores are retained on the surface of the filter. On the other hand, smaller particles are captured within the media depth, a principle known as depth filtration. The accumulated particles create a filter cake on the surface that enhances the filtration efficiency as the process continues.
The filtered gas is then allowed to flow downstream for further use or processing, while the trapped contaminants remain within the filter. Periodic maintenance includes cleaning or replacing the filter element to ensure its utmost operational efficiency.
Therefore, through the effective interplay of design and function, the Natural Gas Filter Element ensures that the natural gas flowing through the system is void of detrimental particles, thereby safeguarding machinery, ensuring optimum performance, and contributing to a superior quality product. It stands as a boon in crucial gas-based infrastructures ensuring smooth, efficient, and contaminant-free operations.
The Natural Gas Filter Element constitutes a vital part of natural gas filtration systems due to its purposeful structural components and functional features. Each element of its design contributes to its overall efficiency, longevity and robustness.
The Natural Gas Filter Element typically involves three primary parts:
Filter Media: This is the heart of the filter element. Filter media can range from pleated paper to woven wire mesh or synthetic materials, all specially designed to filter out contaminants of different sizes. The filter media's role is to allow the natural gas to pass through while trapping dust, dirt, oil, and other harmful particles within its layers.
Support Structures: To withstand the varying pressures of the natural gas flow, a support structure often surrounds the filter media. This structure can be cylindrical or conical and is usually made from stainless steel or an anodized aluminum frame to provide strength and resilience without obstructing the flow of gas.
Sealing Components: To prevent unfiltered gas from bypassing the filter media, top-quality sealing components are used. These might include o-rings, gaskets, or end caps. These seals ensure that all incoming gas is directed through the filter media, thus ensuring the integrity of the filtration process.
In terms of functionality, a Natural Gas Filter Element performs several important roles.
Firstly, it facilitates the complete and effective filtration of natural gas, removing dust, dirt, oil and other contaminants. This efficiently safeguards and improves the overall performance of downstream machinery and systems.
Secondly, it contributes to the longevity of the systems it serves by significantly reducing wear and tear caused by these impurities.
Finally, its presence vastly improves the quality of the output gas, ensuring it is free from destructive contaminants, thereby making it safe for use in various operations and residential purposes.
In summary, the Natural Gas Filter Element, through its distinct structure and function, signifies an irreplaceable asset in natural gas applications for ensuring a clean, efficient, and safe production process.
Typically, the filter media used in a Natural Gas Filter Element falls into one of three categories – glass fiber, cellulose, and activated carbon materials, each fit for a unique function.
Glass Fiber: This is often the first choice when it comes to coalescing liquids. The properties of glass fiber media help separate and filter out liquid droplets from the natural gas stream. The intersections of the fibers capture the liquids, allowing the gas to pass through while retaining the liquid element.
Cellulose: Known for its impressive particulate removal properties, cellulose is a common filter media for gas filter elements. Derived from plant cells, cellulose is a versatile, affordable, and biodegradable medium. The structure of cellulose media is such that micro-particles can get trapped within the media matrix, providing effective particulate filtration.
Activated Carbon Materials: In circumstances where the removal of oil vapor and hydrocarbons from natural gas is required, activated carbon materials are utilized. The high porousness of activated carbon allows for a large surface area that can adsorb volatile organic compounds and other gaseous impurities.
Each of these materials has their own unique properties, and their usage in the filter media of a Natural Gas Filter Element depends on the specific filtration requirements. Sometimes, a combination of these materials may be used to address multiple filtration needs simultaneously.
Cellulose as a filter medium in gas filter elements presents several distinctive filtering properties -
Impressive Particulate Capture: Cellulose is naturally adept at capturing particles due to the network of fibers that comprise its structure. These fibers create a complex web that effectively intercepts and traps particulate matter, providing efficient particulate removal from the gas stream.
Depths Filtration: In contrast to other materials that provide surface-level filtration, cellulose offers depth filtration. Meaning, particles are not only captured on the medium surface but also within the depth of the filter medium, providing a comprehensive filtration solution.
High Dirt Holding Capacity: Cellulose has a high dirt holding capacity which means it can filter a substantial amount of particulates before it needs replacement or cleaning.
Affordability and Biodegradability: Compared to synthetic materials, cellulose is a cost-effective filter medium with the added environmental benefit of being biodegradable.
Variable Pore Size: The pore size in a cellulose filter media can be adjusted during the manufacturing process to meet specific filtration size requirements, providing versatility in its use.
Water Insoluble: Cellulose materials are generally water-insoluble, enabling them to function efficiently in moist environments without disintegrating.
However, it's worth noting that, like all materials, cellulose also has limitations. The organic nature of cellulose makes it susceptible to microbial growth and decay, requiring careful management, particularly in humid environments. Moreover, cellulose may not be as efficient as synthetic materials like glass fiber when filtering ultra-fine particles. Therefore, its use is primarily recommended for applications that demand particle size of moderate range.
A Natural Gas Filter Element provides several notable advantages and strengths, making it an essential component in many industrial applications. Here's an understanding of its key advantages and strengths:
Improved Air Quality: One of the most significant advantages of a Natural Gas Filter Element is the remarkable air quality it ensures. By effectively removing particles and contaminants, it ensures that clean natural gas is delivered for consumption, contributing to the overall health and safety of the end-users.
Protection for Downstream Equipment: By removing particulates, liquids, and other contaminants from the gas stream, the filter element helps protect downstream equipment from potential damage or wear, essentially extending the longevity of the equipment and reducing maintenance costs.
Versatility: Natural Gas Filter Elements have broad versatility. As they're available with varying filter mediums - like cellulose, glass fiber, activated carbon materials - to cater to specific filtration requirements, they can be used across diverse applications.
Efficient Operation: With the right filter element in place, natural gas systems can operate more efficiently. The absence of contaminants reduces pressure drop, decreases the risk of corrosion, and minimizes potential disruptions in the flow.
Economic Value: While the upfront costs of a high-quality Natural Gas Filter Element may seem high, these costs can be quickly offset by the longevity of the element, the protection it provides to downstream equipment, and the efficient operation it enables.
Environmental Advantage: Cleaner natural gas means less pollutant emissions into the environment, making Natural Gas Filter Elements an eco-friendlier option.
Easy Maintenance and Replacement: A well-designed natural gas filter system allows for easy detection of dirty elements, simple extraction process and smooth replacement, reducing downtime.
Each of these advantages makes the natural gas filter element a valuable investment for industries utilizing natural gas, ultimately contributing to efficient, safe, and sustainable operations.
Natural gas filter elements play a crucial role in ensuring the cleanliness of natural gas. Here’s how they do it:
Particle Filtration: The primary function of any filter element is to sieve out solids or particulates from the gas. Filter media with fine pores trap dust, dirt, rust, and other particulate matter thereby preventing them from circulating through the system. This is essential for protecting equipment from damage and enhancing the overall efficiency of the gas system.
Coalescing Action: Some filter elements are designed to remove small liquid droplets that are usually hard to trap. Through a process known as coalescing, these droplets merge and form larger droplets on the surface of the filter, which then drain off. This is particularly useful for removing oil and water aerosols from natural gas.
Adsorption: Some natural gas filters incorporate activated carbon or other adsorbent materials. These materials have the ability to capture certain gases or contaminants at the molecular level, enabling the removal of impurities such as odorants, organic compounds, or sulfuric components, thereby ensuring high gas purity.
Layered Filtration: Some natural gas filter elements utilize multi-layered filtration technology. Each filter layer is designed to capture different sizes of particulates, from larger solids to ultra-tiny particles. The first layer might act as a pre-filter, collecting larger particles and extending the life of finer filter media downstream.
Regular Maintenance and Replacement: Lastly, the cleanliness of natural gas is ensured by regular maintenance and timely replacement of the filter elements. Even the best filter becomes less efficient as it collects contaminants. Regular checks and routine maintenance ensure the filter element continues to deliver high filtration efficiency.
Through these actions, natural gas filter elements ensure the cleanliness and purity of natural gas, improving its performance, reducing wear and tear on equipment, and enhancing safety and efficacy in various applications.
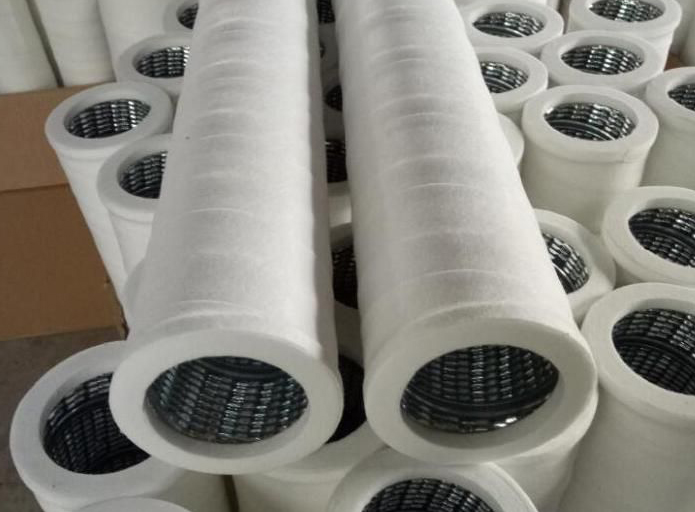
Natural gas filter elements vary in their technical specifications and dimensions based on application requirements and manufacturer design. However, here is a general overview of some characteristics and parameters you might find in these elements:
Size: The inlet and outlet ports can accommodate varying pipe sizes, often ranging from 3" to 10". Specific filter elements can be even larger or smaller, depending on the gas flow rate needed.
Pressure Capacity: Many natural gas filter elements can operate effectively under varying levels of pressure. For instance, some filter elements are designed to work under a maximum pressure of 6 bar while others might have a different pressure range depending on application demands and type of gas filtered.
Particle Filtration Size: Standard filter elements can reportedly remove particles up to 10 microns, although elements are available with 5 or 25 micron filtration capability as optional features.
Coalescing Elements: Some filter elements are designed specifically for coalescing, which is used for the removal of small liquid droplets from the gas stream.
Materials and Construction: The materials used for the filter element could vary. Commonly used materials include cellulose, glass fiber, activated carbon among others, each catering to specific filtration requirements.
Design Standards: Filter element designs often conform to industry standards or certifications to ensure they can effectively filter natural gas and withstand the high pressure and flow rates commonly seen in natural gas pipelines and systems.
Please note that these are general characteristics and the specific technical specifications would differ from one manufacturer to another and are heavily influenced by the end-use and application of the filter element. Always refer to the manufacturer's data sheets or product catalog for accurate and detailed information regarding the specific filter element of interest.
The materials used in the construction of natural gas filter elements are crucial to their performance and efficiency. These materials must be able to withstand harsh conditions without compromising on their filtration capabilities. Depending on the design and purpose, a natural gas filter element may incorporate one or more of the following materials:
Cellulose Fiber: This material is often preferred for its excellent particle retention capabilities and affordability. Cellulose fiber filter elements also have the advantage of being bio-degradable, although their temperature and chemical compatibility may be limited compared to other materials.
Glass Fiber: Glass fiber is another widely used material in filter elements due to its high efficiency in particle retention. It’s designed to handle a large volume of gas, and its temperature resistance and compatibility with various chemicals also make it a strong choice.
Stainless Steel: Metal filters, particularly those made from stainless steel, are known for their robustness and longevity. These filters can operate effectively in high-temperature situations and in corrosive environments. Their reusable nature makes them cost-effective in the long run, although initially, they might be more expensive than other options.
Polyester: Thanks to its durability, polyester is another common choice for filter elements. It remains stable in a wide temperature range, which allows it to cater to different piping environments. Moreover, polyester mantles can sometimes be washable and reusable.
Activated Carbon: This material is commonly used in natural gas filters designed to remove odors, organic compounds or other unwanted gases. Activated carbon has excellent adsorption properties, allowing it to capture compounds at the molecular level.
Ceramic: For high temperature applications, ceramic-based filter elements may be used thanks to their thermal stability. Ceramic has excellent mechanical strength and can provide effective filtration for very small particles.
Remember that the choice of material heavily depends on the exact application and desired filtration characteristics. Always select filter elements based on the specific needs and demands of your system for the best results.
Natural gas filter elements are crucial components used in a wide range of industry applications. They are designed to remove impurities and contaminants from natural gas to ensure that it remains pure, functional, and safe for use. Let’s delve into the different industries where these elements can be applied, along with their common specifications.
Applications
Oil and Gas Industry: Natural gas filters are mainly used in the oil and gas industry. They ensure efficient removal of impurities before processing and transporting natural gas. They also help in protecting downstream equipment from damage caused by contamination.
Chemical Processing: The chemical industry often uses natural gas as a heat source or a raw material. Having a high-quality filter element in place will ensure the purity of the gas, thereby ensuring the quality of the end product.
Power Generation: Natural gas is frequently used in power plants. Natural gas filter elements are used to ensure that the gas is pure and efficient, thus enabling these power plants to produce electricity with a minimal environment footprint.
Industrial Manufacturing: These filters can be found in several types of industrial manufacturing processes such as metal working, where they are used to protect equipment and maintain the quality of end products.
Specifications
Particle Filtration Size: Filter element ratings are available from larger sizes down to very small sizes. Some filters can retain up to 93% of 0.01 micron particles.
Pressure Rating: Most high-quality natural gas filter elements are designed to withstand intense pressure. Many elements can sustain pressure levels up to 1440 psig, depending on the specific application and design.
Customizable: Depending on the specific application and industry requirements, these filter elements can be fully customized to suit these diverse needs.
Materials: Many different materials, including cellulose fiber, glass fiber, stainless steel, polyester, activated carbon, and ceramic, can be used to construct the filter element.
Impurities Removal Capacity: The capability of a natural gas filter element is also evaluated based on its ability to remove different impurities, such as liquid droplets, solid particulates, and even microscopic contaminants.
Design: Natural gas filter elements come in various designs to meet specific operating conditions like high-temperature, high-pressure, and corrosive environments.
Please note that these are typical specifications and can vary depending on the manufacturer and application requirements. Always verify with the manufacturer's product specifics to ensure the filter element is suitable for your application.
Installing and maintaining a natural gas filter element requires following precise steps to ensure safe and optimal use. Here is a detailed guide on the process.
Installation
Review Specifications: First, make sure the filter is suitable for your specific application by matching the specifications with your requirements.
Prep Work Area: Ensure the installation area is clean and free from dust or debris. This is especially important in gas filtration as contaminants can adversely impact the filtration process.
Install Filter Housing: Position the filter housing in your system according to your design or technical requirements. Make sure it is securely fastened and connected to the gas flow lines.
Install Filter Element: Place the filter element inside the housing carefully. Ensure that it is seated correctly within the housing, creating a tight seal.
Secure Lid: After placing the filter, secure the lid of the housing tightly. This is important to prevent any gas leakage.
Connection: Link the filter system to the gas supply line. Use appropriate fittings and connections to ensure a secure seal.
Check for Leaks: Once everything is set, slowly turn on the gas supply and check for any possible leaks. If found, turn off the gas supply immediately and troubleshoot.
Maintenance
Regular Inspection: Regularly checking the filter element for signs of wear or damage is crucial for maintaining its effectiveness. Look for buildup or discoloration, which might indicate accumulated particulates.
Cleaning/Replacing: Depending on the type of filter material, it may need to be cleaned or replaced periodically. For instance, stainless-steel filters can often be cleaned, while other types might need replacement.
Pressure Reading: Keep track of the pressure differential across the filter. An increasing pressure drop might indicate that the filter is getting clogged and needs cleaning or replacement.
Safety Measures: Always ensure that all safety measures are followed while performing any maintenance tasks. For instance, ensure the gas supply is shut off before opening the filter housing.
Record Keeping: A maintenance log should be kept for each filtration unit. This can help predict when future maintenance will be needed based on the history of the filter element.
Remember, the installation and maintenance guidelines provided here are general practices. The exact procedures depend on the specific product, application, and manufacturer's instructions. Always refer to the manufacturer's manual and adhere to their recommendations for the best results.
With the rising awareness of environmental conservation and the significance of clean energy, the use of natural gas filter elements is becoming increasingly influential in modern society. Here is an in-depth look into their environmental implications and societal impact.
Environmental Impact
Reduced Contamination: Natural gas filter elements help to purify natural gas by capturing impurities, significantly reducing the release of potentially harmful substances into the environment. This makes the use of natural gas a more eco-friendly choice for various applications.
Efficient Resource Use: By efficiently removing contaminants, these filters ensure the natural gas supply is clean and functional, thereby enabling an efficient and optimized use of this resource. This efficient use contributes to sustainability efforts by reducing wastage.
Lower Emissions: Compared to combustion of other fossil fuels, burning clean natural gas produces significantly less harmful emissions, contributing to cleaner air and a healthier environment.
Potential for Recycling: Certain types of natural gas filter elements, like those made of stainless steel or ceramic, can be cleaned and reused, reducing the need for producing new filters and thus lessening the environmental footprint of these products.
Societal Impact
Energy Security: With numerous industries, utilities, and homes relying heavily on natural gas, ensuring its purity for efficient use indirectly influences energy security. Constant supply of purified natural gas can help prevent potential energy crises.
Job Creation: The manufacturing, installation, and maintenance of natural gas filter elements can contribute to job creation in the associated industries. Moreover, as the demand for clean energy rises, so will the demand for these filters, leading to more job opportunities.
Public Health: By helping reduce harmful emissions from burning natural gas, these filter elements contribute to cleaner air, which is directly linked to better public health outcomes, lessening the burden on the healthcare system over time.
Technological Advancements: The development of more efficient and effective natural gas filter elements fuels technological advancements, promoting a culture of innovation and progress that can be beneficial for all of society.
In conclusion, natural gas filter elements play a significant role in societal progress and environmental preservation. By ensuring the cleanliness and safe use of natural gas, these components contribute to sustainable development and a brighter future.