The wind power industry filter system is an essential component in wind energy generation, designed to optimize the efficiency and longevity of the wind turbines. This system works by removing dirt particles from the air, operating fluids, or surface water that could potentially impair the functioning of the turbine.
The primary function of this system is to ensure the clean operation of the wind turbines, thus reducing the risk of mechanical breakdowns and costly repairs. It accomplishes this through a series of filtration processes that remove harmful contaminants before they can reach the sensitive parts of the turbine.
The filter system is typically composed of several different types of filters, each designed to remove a specific type of contaminant. These may include air filters to remove airborne particles, fluid filters to clean the operating fluids, and water filters to purify any surface water used in the turbine.
In addition to improving the operational efficiency of the wind turbines, these filter systems also contribute to the sustainability of the wind power industry. By ensuring the clean operation of the turbines, they help to minimize the environmental impact of wind power generation.
In summary, the wind power industry filter system is a critical tool in the wind energy sector, helping to maximize the performance of wind turbines and contribute to the growth and sustainability of the industry.

The filter system improves the operational efficiency of wind turbines in several ways.
Protection from Contaminants: The primary function of the filter system is to remove contaminants that could potentially damage the turbine. This includes airborne particles, such as dust and dirt, as well as contaminants found in operating fluids or surface water. By filtering out these contaminants, the system protects the sensitive parts of the turbine, reducing the risk of mechanical breakdowns and costly repairs.
Maintaining Optimal Conditions: The filter system helps to maintain the optimal conditions necessary for the turbine to function efficiently. For instance, clean air is essential for the turbine's cooling system to work effectively. By removing airborne particles, the air filter helps to ensure that the cooling system can operate at its best, preventing overheating and improving the overall efficiency of the turbine.
Reducing Wear and Tear: By removing contaminants, the filter system also reduces the wear and tear on the turbine's components. This can extend the lifespan of the turbine, reducing the need for replacement parts and maintenance, and thereby improving the cost-efficiency of the operation.
Enhancing Energy Production: Finally, by ensuring the clean operation of the turbine, the filter system can enhance the energy production of the wind turbine. A clean, well-maintained turbine can operate more efficiently, generating more energy and thereby increasing the overall productivity of the wind power operation.
In summary, the filter system plays a crucial role in improving the operational efficiency of wind turbines, protecting them from contaminants, maintaining optimal operating conditions, reducing wear and tear, and enhancing energy production.
The Wind Power Industry Filter System operates on a fundamental principle of removing contaminants that could potentially impair the performance and longevity of wind turbines. Here's a detailed explanation of its working principle:
Air Filtration: The air filter is the first line of defense. It's designed to remove airborne particles such as dust, dirt, and other environmental pollutants that could damage the turbine's components. The air is drawn into the system, passed through the filter media where contaminants are trapped, and then clean air is released into the turbine. This process ensures that only clean air enters the turbine, reducing the risk of damage to the turbine blades and other components.
Fluid Filtration: The fluid filtration process is crucial in maintaining the turbine's hydraulic and lubrication systems. Operating fluids, such as oil and hydraulic fluid, are passed through a filter that removes any particles or impurities. This process ensures that the fluids used in the turbine are clean, which is vital for the smooth operation of the turbine's moving parts and reducing the risk of mechanical breakdowns.
Water Filtration: Some turbines use surface water for cooling purposes. The water filter system is designed to purify this water by removing any pollutants or contaminants. The water is passed through a filter media that traps these impurities. The clean water is then used in the cooling system, ensuring that it operates efficiently and that no harmful particles are introduced into the turbine.
Regular Maintenance: To ensure the effectiveness of the filter system, regular maintenance is crucial. This includes replacing the filters regularly and checking the system for any potential issues. This ensures that the filter system continues to operate efficiently and effectively, protecting the turbine and improving its overall performance.
In essence, the Wind Power Industry Filter System works by removing harmful contaminants from the air, operating fluids, and water used in the turbine. This not only protects the turbine's components but also ensures its efficient operation and longevity.
The filtration system plays a vital role in protecting the turbine blades and other components from damage. Here's how it does this:
Air Filtration: The air filter is designed to remove airborne particles such as dust, sand, and other environmental pollutants. When these particles enter the turbine, they can cause abrasion and erosion on the turbine blades, significantly reducing their efficiency and lifespan. By filtering out these contaminants, the air filter protects the blades and other components from this type of damage.
Fluid Filtration: The fluid filters in the system protect the turbine's components by removing impurities from the operating fluids. Particles in the oil or hydraulic fluid can cause wear and tear on the moving parts of the turbine, including the gearbox and bearings. By filtering out these particles, the fluid filters help to prevent this wear and tear, extending the lifespan of these components.
Water Filtration: If the turbine uses surface water for cooling, the water filter system is designed to remove any pollutants or contaminants from this water. These impurities can cause corrosion and other types of damage to the turbine's components. By providing clean water for the cooling system, the water filter helps to protect these components from such damage.
Regular Maintenance: Regular maintenance of the filter system is also crucial for protecting the turbine's components. This includes replacing the filters regularly to ensure they continue to remove contaminants effectively, and checking the system for any potential issues. Regular maintenance helps to ensure that the system continues to protect the turbine effectively, reducing the risk of damage and breakdowns.
In summary, the filtration system protects the turbine blades and other components by removing harmful contaminants from the air, operating fluids, and water used in the turbine. This not only prevents damage but also ensures the efficient operation and longevity of the turbine.
The Wind Power Industry Filter System is a comprehensive setup designed to safeguard the performance and longevity of wind turbines. Here's a detailed breakdown of its components and their functions:
Air Filter: The air filter is designed to remove airborne particles such as dust, sand, and other environmental pollutants. It ensures that only clean air enters the turbine, reducing the risk of damage to the turbine blades and other components. This is crucial for maintaining the efficiency and lifespan of the turbine.
Fluid Filter: The fluid filter is responsible for maintaining the purity of the operating fluids, such as oil and hydraulic fluid. It removes any particles or impurities that could cause wear and tear on the moving parts of the turbine, including the gearbox and bearings. This process is vital for the smooth operation of the turbine's moving parts and reducing the risk of mechanical breakdowns.
Water Filter: If the turbine uses surface water for cooling, the water filter system purifies this water by removing any pollutants or contaminants. This ensures that the cooling system operates efficiently and that no harmful particles are introduced into the turbine.
Filter Housing: The filter housing provides a protective casing for the filters, ensuring they are securely held in place and can effectively perform their filtration tasks. It is usually made from durable materials to withstand the harsh conditions in which wind turbines often operate.
Filter Media: The filter media is the material that actually traps and removes the contaminants from the air, fluids, or water. It's typically made from materials like synthetic fibers, cellulose, or wire mesh, depending on the specific requirements of the filter.
Seals and Gaskets: These components ensure a tight fit between the filter and its housing, preventing any unfiltered air, fluid, or water from bypassing the filter and entering the turbine.
Pressure Gauges and Indicators: These components monitor the performance of the filter system. They can indicate when a filter is becoming clogged and needs to be replaced, helping to ensure the system continues to operate effectively.
In essence, the Wind Power Industry Filter System comprises of various components working together to remove harmful contaminants from the air, operating fluids, and water used in the turbine. This not only protects the turbine's components but also ensures its efficient operation and longevity.
The technical specifications and specifications of the Wind Power Industry Filter System can vary greatly depending on the specific model and manufacturer. However, I can provide some general parameters that are often considered:
Filter Efficiency: This refers to the percentage of contaminants that the filter can remove from the air, fluid, or water. It's typically measured in microns, with a smaller micron rating indicating a higher efficiency.
Flow Rate: This is the volume of air, fluid, or water that can pass through the filter in a specific amount of time. It's usually measured in cubic feet per minute (CFM) for air filters and gallons per minute (GPM) for fluid and water filters.
Operating Pressure: This is the pressure at which the filter system can operate effectively. It's typically measured in pounds per square inch (PSI).
Operating Temperature: This is the range of temperatures at which the filter system can operate effectively. It's usually given as a range, for example, -40 to 80 degrees Celsius.
Filter Life: This is the expected lifespan of the filter before it needs to be replaced. It can vary greatly depending on the specific filter and operating conditions.
Filter Housing Material: This is the material from which the filter housing is made. It needs to be durable and resistant to the conditions in which the wind turbine operates.
Filter Media Material: This is the material from which the filter media is made. It can vary depending on the specific requirements of the filter, but common materials include synthetic fibers, cellulose, and wire mesh.
Seal Material: This is the material from which the seals and gaskets are made. It needs to be able to create a tight seal between the filter and its housing, and resistant to the operating fluids and temperatures.
Dimensions: These are the physical dimensions of the filter system, including its length, width, and height. They need to be suitable for the space available in the wind turbine.
These are just some of the technical parameters and specifications that can be considered when evaluating a Wind Power Industry Filter System. The specific values for these parameters can vary greatly depending on the specific model and manufacturer.
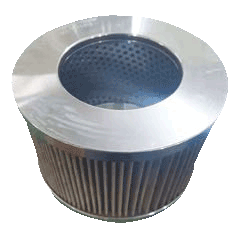
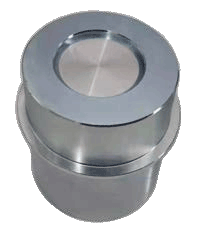
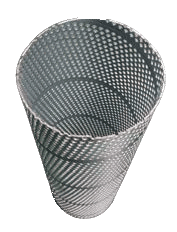
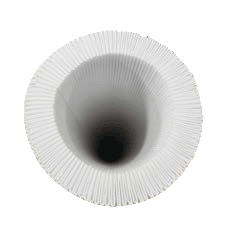
Protection filter Bypass valve assembly Thickened helical endoskeleton Fine filter layer
The Wind Power Industry Filter System offers numerous advantages and benefits that contribute to the efficient operation and longevity of wind turbines. Here are some of its key strengths:
Improved Efficiency: By removing airborne particles, impurities in operating fluids, and contaminants in cooling water, the filter system ensures that the turbine operates at its peak efficiency. This leads to a higher power output and better performance.
Extended Lifespan: The filtration system helps to extend the lifespan of the turbine's components by preventing wear and tear, abrasion, erosion, and other types of damage. This not only reduces the need for repairs and replacements but also lowers the overall maintenance costs.
Reduced Downtime: With a robust filtration system, the chances of unexpected breakdowns due to contaminated inputs are significantly reduced. This minimizes downtime and ensures a consistent power generation.
Environmentally Friendly: By ensuring that only clean air is released from the turbines and that all operating fluids are kept clean, the filter system contributes to the environmental sustainability of wind power operations.
Flexible and Adaptable: The filter system can be tailored to suit the specific needs of each wind turbine, taking into account factors such as the local environment, the type of turbine, and the specific operating conditions.
Cost-Effective: While there is an upfront cost involved in installing a filtration system, the long-term savings in terms of reduced maintenance costs and extended component lifespans can make it a cost-effective investment.
Easy Maintenance: Most filter systems are designed for easy maintenance, with simple procedures for replacing the filters and checking the system's performance. This can save time and effort in the long run.
In summary, the Wind Power Industry Filter System offers a range of advantages that can enhance the performance, reliability, longevity, and environmental sustainability of wind turbines. It's a vital component of any wind power operation, helping to ensure that the turbines operate efficiently and effectively for as long as possible.
The filtration system plays a crucial role in ensuring the environmental friendliness of wind turbines. Here's how:
Air Quality Control: The filtration system removes airborne particles and contaminants from the air that is used in the turbine's operations. This prevents the release of these contaminants into the environment, thereby reducing air pollution.
Fluid Management: The filtration system also cleans the operating fluids (such as hydraulic and lubricating oils) used in the turbine. This ensures that any waste or used fluids are free from harmful contaminants before they are disposed of, reducing the risk of soil and water pollution.
Noise Reduction: Some filtration systems also help to reduce the noise produced by the turbine's operations. This minimizes noise pollution, which can be a concern especially for wind farms located near residential areas.
Energy Efficiency: By maintaining the efficiency of the turbine's operations, the filtration system helps to maximize the conversion of wind energy into electrical energy. This reduces the need for other, potentially less environmentally friendly sources of power.
Longevity of Components: By preventing wear and tear and other types of damage, the filtration system extends the lifespan of the turbine's components. This reduces the need for replacements, which in turn lowers the environmental impact associated with the production of replacement parts.
In these ways, the filtration system contributes significantly to the environmental sustainability of wind power operations. It helps to ensure that wind turbines not only produce clean, renewable energy, but also operate in a manner that minimizes their impact on the environment.
The Wind Power Industry Filter System has a wide range of applications across various industries. Here are some key sectors where it is extensively used:
Renewable Energy Industry: The most obvious application is within the renewable energy sector, specifically in wind farms and wind power plants. These facilities use the filtration system to ensure the efficient operation and longevity of their wind turbines.
Manufacturing Industry: Companies that manufacture wind turbines also use these filter systems during the production process. They help to ensure that the components are free from contaminants, which can improve the quality and reliability of the final product.
Marine Industry: Offshore wind farms, which are becoming increasingly common, also use these filtration systems. They are particularly important in these environments due to the presence of salt and other corrosive elements in the sea air.
Utility Companies: Utility companies that operate wind turbines as part of their energy mix also use these filtration systems. They help to ensure the reliable operation of the turbines, which can be a significant factor in the stability of the power grid.
Maintenance and Repair Services: Companies that provide maintenance and repair services for wind turbines also use these filtration systems. They can be an important tool for diagnosing and resolving issues related to contamination.
Research and Development: In the R&D sector, the filter system is used for developing and testing new wind turbine designs. The system's ability to provide clean, controlled operating conditions can be invaluable in these settings.
In summary, the Wind Power Industry Filter System is a versatile tool that has applications across a range of industries. Its ability to enhance the performance and reliability of wind turbines makes it a valuable asset in any sector where these machines are used.
Installation and maintenance of the Wind Power Industry Filter System are critical aspects of ensuring its optimal operation and longevity. Here's a detailed look at these processes:
Installation:
Site Assessment: Before installation, a thorough assessment of the wind turbine's setup is necessary. This includes understanding the specific requirements of the turbine, the environmental conditions, and the potential contaminants that the filter system needs to tackle.
Choosing the Right Filter System: Based on the assessment, the appropriate filter system is selected. This includes choosing the right size, type, and specifications of the filter to match the turbine's requirements.
Installation Process: The filter system is then installed in the appropriate location within the wind turbine, usually in close proximity to the air intake or the fluid systems. This process should be carried out by a trained professional to ensure correct installation.
System Testing: After installation, the filter system should be tested under operational conditions to ensure it is functioning correctly and efficiently.
Maintenance:
Regular Inspection: The filter system should be inspected on a regular basis to check for any signs of wear and tear or damage. This includes checking the filter media for clogs or tears, and the housing for any leaks or cracks.
Cleaning and Replacement: Depending on the type of filter and the operating conditions, the filter media may need to be cleaned or replaced periodically. This should be done according to the manufacturer's instructions to ensure the continued efficiency of the system.
System Checks: In addition to the filter itself, the overall system should also be checked regularly. This includes checking the seals and gaskets for leaks, and the pressure and flow rates to ensure they are within the specified range.
Record Keeping: Keeping detailed records of all maintenance activities can help to identify trends or issues, and can be useful for planning future maintenance activities.
Professional Service: For complex issues or major maintenance activities, professional service may be required. This ensures that the work is carried out correctly and safely, and can help to prolong the life of the filter system.
By following these steps for installation and maintenance, the Wind Power Industry Filter System can provide reliable and efficient service, helping to maximize the performance and lifespan of the wind turbine.
The regular inspection of a Wind Power Industry Filter System is crucial to ensure its optimal functioning and longevity. Here are the key aspects that should be checked during a routine inspection:
Filter Media: The filter media is the main component that removes contaminants from the air or fluids. Regular inspections should check for any signs of clogging, damage, or wear and tear. If the filter media is reusable, it may need to be cleaned; if it's disposable, it may need to be replaced.
Seals and Gaskets: These components ensure that the system is airtight and that there are no leaks. They should be checked for any signs of damage or wear that could lead to leaks.
Housing: The housing protects the filter media and other components of the system. It should be checked for any signs of damage, corrosion, or leaks.
Pressure and Flow Rates: The pressure and flow rates of the system should be monitored to ensure they are within the specified range. Any significant changes could indicate a problem with the system.
System Performance: The overall performance of the system should be assessed. This includes checking the efficiency of the filtration process, as well as any changes in the operation of the wind turbine that could be related to the filter system.
Safety Features: Any safety features, such as pressure relief valves or alarms, should be checked to ensure they are functioning correctly.
Documentation: All inspections should be documented, including the date, the person conducting the inspection, the results of the inspection, and any actions taken. This can help to identify trends or issues over time.
By conducting regular inspections and addressing any issues promptly, the Wind Power Industry Filter System can continue to function efficiently and effectively, helping to enhance the performance and lifespan of the wind turbine.