VICKERS filter elements are renowned for their quality and efficiency in fluid power applications. Manufactured by Eaton Corporation, these filter elements are an integral part of VICKERS filtration products, designed to provide superior contamination control and extend the lifespan of hydraulic systems.
Product Overview:
High Efficiency: VICKERS filter elements are designed with high efficiency in mind. They are capable of removing a high percentage of particulate contamination, ensuring clean, efficient operation of the hydraulic system.
Broad Range: VICKERS offers a broad range of filter elements to suit various applications. This includes elements for pressure, suction, and return line filters, each designed to meet specific system requirements.
Advanced Media Technology: VICKERS filter elements employ advanced media technology. This includes glass fiber, wire mesh, and cellulose media, each offering unique benefits in terms of filtration efficiency and dirt-holding capacity.
Durability: VICKERS filter elements are built to withstand challenging operating conditions. They are resistant to pressure surges, system vibrations, and corrosive fluids, ensuring reliable performance and longevity.
Compatibility: VICKERS filter elements are compatible with a wide range of hydraulic fluids, including mineral oils, synthetic fluids, and water-glycol based fluids.
Easy Maintenance: VICKERS filter elements are designed for easy replacement and maintenance. Regular element replacement ensures optimal system performance and extends the service life of the hydraulic system.
In conclusion, VICKERS filter elements by Eaton Corporation are a reliable choice for maintaining cleanliness in hydraulic systems. They offer high efficiency, durability, and compatibility, making them suitable for a wide range of applications. Always remember to replace these elements regularly to ensure the best performance of your hydraulic system.
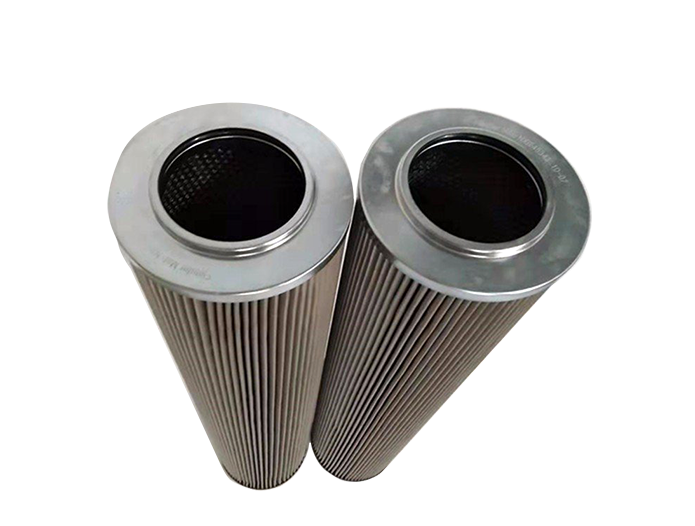
The high efficiency of VICKERS filter elements is achieved through a combination of advanced design and technology. Here's a closer look at how they work:
Multi-Layer Media Construction: VICKERS filter elements utilize a multi-layer media construction. This design allows for the effective capture of different sizes of particulate contamination, with larger particles captured in the outer layers and smaller particles in the inner layers. This multi-stage filtration process ensures a high level of cleanliness in the hydraulic fluid.
Advanced Media Material: The choice of media material is crucial in determining the efficiency of a filter element. VICKERS uses advanced media materials such as glass fiber, which has excellent filtration efficiency for small particles, and wire mesh, which is durable and effective for larger particles.
Optimized Flow Path: The flow path inside the filter element is optimized to ensure that the fluid spends a sufficient amount of time in contact with the filter media. This allows for maximum particulate capture and minimal pressure drop across the filter element.
Sealing Technology: VICKERS filter elements feature superior sealing technology. This ensures that all fluid passes through the filter media, preventing bypass and ensuring that contamination is effectively removed from the fluid.
Regular Maintenance: Lastly, the efficiency of VICKERS filter elements is maintained through regular replacement and maintenance. Over time, filter elements can become clogged with captured particles, reducing their efficiency. Regular replacement ensures that the filter element is always operating at its peak efficiency.
In summary, the high efficiency of VICKERS filter elements is achieved through advanced design, superior media materials, optimized fluid flow, effective sealing, and regular maintenance. These elements are designed to provide the highest level of cleanliness in hydraulic systems, ensuring their efficient operation and longevity.
The multi-layer media structure of filter elements plays a crucial role in achieving high-efficiency particle capture. Here's a detailed explanation of how this structure works:
Layered Filtration: The multi-layer media structure operates on the principle of layered filtration. This means that each layer of the media is designed to capture particles of a specific size range. The outer layers are typically designed to capture larger particles, while the inner layers are designed to capture smaller particles. This tiered approach to filtration ensures that particles of all sizes are effectively captured, enhancing the overall filtration efficiency.
Depth Filtration: Another aspect of the multi-layer media structure is depth filtration. Instead of simply capturing particles on the surface of the media, the multi-layer structure allows for the capture of particles within the depth of the media. This increases the total filtration area, allowing for a higher volume of fluid to be filtered without a significant increase in pressure drop.
Graduated Density: The density of the filter media typically increases from the outer layers to the inner layers. This graduated density design ensures that larger particles are captured before they can block the pores of the inner layers, which are designed to capture smaller particles. This extends the life of the filter element and maintains its efficiency over time.
Material Selection: The choice of media material for each layer is also important. Materials such as glass fiber, cellulose, and synthetic media are used, each with its own specific filtration properties. The selection of these materials is based on their ability to capture particles of specific sizes, their compatibility with the fluid being filtered, and their resistance to degradation.
Sealing and Support: The layers of the filter media are sealed and supported to ensure that all fluid passes through the media and that the layers maintain their structural integrity. This ensures that the filtration process is not compromised by bypass or media failure.
In conclusion, the multi-layer media structure of filter elements achieves high-efficiency particle capture through a combination of layered filtration, depth filtration, graduated density, careful material selection, and effective sealing and support. This design ensures that particles of all sizes are effectively captured, maintaining the cleanliness of the hydraulic fluid and the efficiency of the system.
The working principle of VICKERS filter elements is a combination of robust design, advanced filtration technology, and efficient operation. Here is a detailed explanation:
Filtration Process: The primary function of a VICKERS filter element is to remove particulate contamination from the hydraulic fluid. This is achieved through the filtration process, where the fluid is passed through the filter media, and particles are captured and retained within the media.
Multi-Layer Media Structure: The filter media in a VICKERS filter element is structured in multiple layers. Each layer is designed to capture particles of a specific size range, with larger particles being captured in the outer layers and smaller particles in the inner layers. This multi-layer structure maximizes filtration efficiency and extends the life of the filter element.
Advanced Media Material: VICKERS filter elements utilize advanced media materials such as glass fiber and wire mesh. Glass fiber has excellent filtration efficiency for small particles, while wire mesh is durable and effective for larger particles. The choice of media material is crucial in determining the efficiency and lifespan of the filter element.
Optimized Flow Path: The flow path inside the filter element is optimized to ensure that the fluid spends a sufficient amount of time in contact with the filter media. This allows for maximum particulate capture and minimal pressure drop across the filter element.
Sealing Technology: VICKERS filter elements feature superior sealing technology. This ensures that all fluid passes through the filter media, preventing bypass and ensuring that contamination is effectively removed from the fluid.
Maintenance and Replacement: Over time, the filter element can become clogged with captured particles, reducing its efficiency. Regular maintenance and replacement of the filter element ensure that it always operates at peak efficiency, maintaining the cleanliness of the hydraulic fluid and the efficiency of the hydraulic system.
In conclusion, the working principle of VICKERS filter elements involves a combination of advanced design, superior media materials, optimized fluid flow, effective sealing, and regular maintenance. This ensures that they provide the highest level of cleanliness in hydraulic systems, contributing to their efficient operation and longevity.
A VICKERS filter element is a critical component in maintaining the cleanliness and efficiency of hydraulic systems. It is composed of several key parts, each playing a specific role in the filtration process. Here's a detailed breakdown of its components and their functions:
Filter Media: This is the heart of the filter element, responsible for capturing and retaining particulate contamination. VICKERS filter elements typically use advanced media materials such as glass fiber and wire mesh, which offer high filtration efficiency and durability.
Support Structure: Surrounding the filter media is a support structure, often made from metal or plastic. This structure provides the necessary strength to the filter element, preventing it from collapsing under the hydraulic pressure.
End Caps: The filter media and support structure are enclosed by end caps. These caps are typically made from metal or durable plastic and are designed to ensure a tight seal within the filter housing, preventing any bypass of unfiltered fluid.
Center Tube: Inside the filter element is a center tube which provides additional support to the filter media and serves as a conduit for the filtered fluid to exit the filter element.
Sealing Gasket: This component ensures a tight seal between the filter element and the filter housing, preventing any leakage or bypass of unfiltered fluid.
In terms of functionality, the VICKERS filter element performs several key roles:
Particle Removal: The primary function of the filter element is to remove particulate contamination from the hydraulic fluid. This is achieved through the filter media, which captures and retains particles of various sizes.
Protection of Hydraulic Components: By removing particulate contamination, the filter element protects sensitive hydraulic components from wear and damage, thereby extending their lifespan and reducing maintenance costs.
Maintaining Fluid Cleanliness: The filter element plays a crucial role in maintaining the cleanliness of the hydraulic fluid. Clean fluid is essential for the efficient operation of the hydraulic system and reduces the risk of system failure.
Ensuring System Efficiency: By maintaining fluid cleanliness and protecting hydraulic components, the filter element contributes to the overall efficiency of the hydraulic system.
In conclusion, a VICKERS filter element is composed of several key components, each playing a crucial role in the filtration process. Its primary functions include particle removal, protection of hydraulic components, maintaining fluid cleanliness, and ensuring system efficiency.
VICKERS filter elements play a vital role in protecting the key components of hydraulic systems. Here's how:
Removal of Contaminants: The primary function of VICKERS filter elements is to remove particulate contaminants from the hydraulic fluid. These contaminants, if left unchecked, can cause wear and tear on the hydraulic components, leading to system inefficiency and potential failure.
Prevention of Abrasion: By capturing and retaining these particles, the filter elements prevent them from circulating within the system where they could cause abrasion and damage to sensitive components such as pumps, valves, and actuators.
Maintaining Fluid Cleanliness: Clean hydraulic fluid is essential for the optimal operation of a hydraulic system. VICKERS filter elements ensure the cleanliness of the fluid by removing contaminants, thereby reducing the risk of component contamination and system failure.
Reducing System Downtime: By protecting the hydraulic components from wear and damage, VICKERS filter elements reduce the need for maintenance and repairs, thereby minimizing system downtime.
Extending Component Lifespan: By maintaining the cleanliness of the hydraulic fluid and preventing wear and tear on the components, the filter elements contribute to extending the lifespan of the hydraulic components.
Ensuring System Efficiency: Clean hydraulic fluid and well-maintained components result in a more efficient hydraulic system. By ensuring the cleanliness of the fluid and the integrity of the components, VICKERS filter elements contribute to the overall efficiency of the hydraulic system.
In conclusion, VICKERS filter elements protect the key components of hydraulic systems by removing contaminants, preventing abrasion, maintaining fluid cleanliness, reducing system downtime, extending component lifespan, and ensuring system efficiency.
VICKERS filter elements come in a variety of specifications, tailored to specific applications and system requirements. Here are some general technical parameters and specifications:
Material: VICKERS filter elements are typically made from advanced materials such as glass fiber, stainless steel wire mesh, and paper. These materials offer high filtration efficiency and durability.
Filtration Accuracy: The filtration accuracy of VICKERS filter elements can range from 3μm to 200μm, depending on the specific model and application.
Working Pressure: These filter elements are designed to operate under a wide range of pressures, typically from 10bar to 210bar.
Working Media: VICKERS filter elements are suitable for use with various working media, including hydraulic and lubrication fluids.
Working Temperature: These filter elements can operate within a broad temperature range, typically from -30°C to +100°C.
Sealing Material: The sealing gaskets used in VICKERS filter elements are usually made from materials like nitrile and Viton, with other materials available on request.
Dimensions: The dimensions of VICKERS filter elements can vary greatly depending on the specific model. For example, some models have an outer diameter (OD) of 3.990", an inner diameter (ID) of 2.900", and a length of 6.690".
End Caps: The end caps of some models are made from corrosion-resistant steel or aluminum.
Please note that these are general specifications and the exact technical parameters can vary depending on the specific model of the VICKERS filter element. Always refer to the manufacturer's data sheet for precise information.

VICKERS filter elements offer a host of advantages and strengths that make them a top choice for hydraulic system filtration. Here are some of the key benefits:
High Filtration Efficiency: VICKERS filter elements are known for their high filtration efficiency. They can effectively filter out particulate contaminants, ensuring the cleanliness of the hydraulic fluid. This helps to protect the key components of the hydraulic system and ensure its efficient operation.
Durable and Reliable: Made from advanced materials such as glass fiber, stainless steel wire mesh, and paper, VICKERS filter elements are highly durable and reliable. They can withstand a wide range of pressures and temperatures, making them suitable for use in various hydraulic systems.
Extended Component Lifespan: By maintaining the cleanliness of the hydraulic fluid and preventing wear and tear on the components, VICKERS filter elements contribute to extending the lifespan of the hydraulic components. This reduces the need for frequent component replacement, resulting in cost savings.
Reduced System Downtime: By protecting the hydraulic components from wear and damage, VICKERS filter elements help to minimize system downtime. This ensures the smooth and continuous operation of the hydraulic system, improving productivity.
Versatility: VICKERS filter elements are versatile and can be used with various working media, including hydraulic and lubrication fluids. This makes them suitable for a wide range of applications.
Easy Maintenance: VICKERS filter elements are designed for easy maintenance. They can be easily replaced when necessary, reducing maintenance time and effort.
Cost-Effective: While offering high performance and durability, VICKERS filter elements are also cost-effective. They provide excellent value for money by reducing maintenance costs and extending the lifespan of the hydraulic system components.
In conclusion, the advantages and strengths of VICKERS filter elements lie in their high filtration efficiency, durability, reliability, ability to extend component lifespan, reduce system downtime, versatility, easy maintenance, and cost-effectiveness.
VICKERS filter elements are versatile and find usage across a wide array of industries due to their high efficiency, reliability, and durability. Here are some of the primary sectors where they are applied:
Manufacturing Industry: In manufacturing plants, VICKERS filter elements are used in hydraulic systems of various machinery and equipment for efficient operation and longer lifespan.
Construction Industry: Heavy-duty machinery such as excavators, loaders, and cranes that are used in the construction industry often employ hydraulic systems. VICKERS filter elements play a crucial role in maintaining the optimal operation of these systems.
Oil and Gas Industry: In the oil and gas industry, VICKERS filter elements are used in hydraulic systems for drilling, extraction, and refining processes. They ensure the cleanliness of hydraulic fluids, thereby preventing wear and tear on crucial components.
Aerospace Industry: Hydraulic systems are essential in aircraft for controlling flight surfaces, landing gear, brakes, and more. VICKERS filter elements ensure these systems are free from contaminants, thus ensuring safe and efficient operation.
Automotive Industry: In the automotive industry, hydraulic systems are used in various applications, including power steering and brake systems. VICKERS filter elements help to maintain the performance and safety of these systems.
Marine Industry: In marine applications, hydraulic systems are used for steering, stabilizing, and other critical operations. VICKERS filter elements ensure these systems operate efficiently and reliably.
Power Generation Industry: In power plants, hydraulic systems are used for controlling turbines, valves, and other key components. VICKERS filter elements help to maintain the efficiency and reliability of these systems.
Mining Industry: In mining operations, hydraulic systems are used in heavy machinery for extraction and transportation of minerals. VICKERS filter elements ensure these systems operate optimally, reducing downtime and maintenance costs.
In conclusion, VICKERS filter elements find extensive applications across various industries, ensuring the efficient operation of hydraulic systems and contributing to the overall productivity and safety of operations.
VICKERS filter elements play a crucial role in enhancing the efficiency of excavation and transportation machinery in the mining industry. Here's how:
Maintaining Hydraulic Fluid Cleanliness: Mining machinery is often exposed to harsh environments with a lot of dust and debris. VICKERS filter elements effectively filter out these particulate contaminants, maintaining the cleanliness of the hydraulic fluid. This prevents wear and tear on the hydraulic components, ensuring their efficient operation.
Reducing Component Wear and Tear: By keeping the hydraulic fluid clean, VICKERS filter elements prevent abrasive particles from causing wear and tear on the hydraulic components. This ensures the smooth operation of the machinery and reduces the need for frequent component replacement.
Preventing System Failure: Contaminants in the hydraulic fluid can lead to system failure, resulting in costly downtime. VICKERS filter elements help to prevent system failure by maintaining the cleanliness of the hydraulic fluid, thereby ensuring the continuous operation of the machinery.
Extending Component Lifespan: By preventing wear and tear on the components, VICKERS filter elements contribute to extending the lifespan of the hydraulic components. This reduces the need for frequent component replacement, resulting in cost savings and increased machinery uptime.
Improving System Efficiency: Clean hydraulic fluid ensures the efficient operation of the hydraulic system. This improves the overall efficiency of the machinery, enabling it to perform at its best and increasing productivity in the mining operations.
Reducing Maintenance Costs: By extending the lifespan of the hydraulic components and preventing system failure, VICKERS filter elements help to reduce maintenance costs. This contributes to the overall efficiency and cost-effectiveness of the mining operations.
In conclusion, VICKERS filter elements enhance the efficiency of excavation and transportation machinery in the mining industry by maintaining hydraulic fluid cleanliness, reducing component wear and tear, preventing system failure, extending component lifespan, improving system efficiency, and reducing maintenance costs.
VICKERS filter elements are integral parts of hydraulic systems, ensuring the fluid cleanliness and overall system efficiency. Here's a detailed guide on their installation and maintenance:
Installation:
Identify the Correct Filter: Before installation, ensure that the VICKERS filter element matches the specifications of your hydraulic system. This includes checking the filter's micron rating, flow capacity, and pressure rating.
Prepare the System: Before installing the filter element, ensure the system is clean and free from contaminants. This may involve flushing the system or cleaning the filter housing.
Install the Filter Element: Carefully place the filter element into the filter housing, ensuring it fits snugly and correctly. Avoid touching the filter media to prevent contamination.
Secure the Filter Housing: Once the filter element is in place, secure the filter housing. Ensure the housing is sealed properly to prevent leaks.
Check for Proper Installation: After installation, run the system and check for leaks or pressure drops. If any issues are found, they should be addressed immediately.
Maintenance:
Regular Inspection: Regularly inspect the filter elements for signs of wear or damage. This includes checking for tears in the filter media, deformities in the filter structure, or excessive contaminant buildup.
Monitor Pressure Drop: Monitor the pressure drop across the filter element. An increasing pressure drop indicates the filter element is becoming clogged and may need to be cleaned or replaced.
Cleaning: Some VICKERS filter elements are cleanable. This involves removing the filter element from the housing and carefully cleaning it to remove trapped contaminants. However, this should only be done if the filter is designed to be cleaned and reused.
Replacement: Over time, filter elements will need to be replaced. This should be done according to the manufacturer's recommendations or when the filter element is no longer effectively filtering contaminants. When replacing the filter element, ensure the system is clean to prevent immediate contamination of the new filter.
Dispose of Used Filters Properly: Used filter elements should be disposed of properly to prevent environmental contamination.
In conclusion, proper installation and maintenance of VICKERS filter elements are crucial for the optimal operation of hydraulic systems. Regular inspection, monitoring, cleaning, and replacement of filter elements can ensure the longevity and efficiency of your hydraulic systems.
VICKERS filter elements contribute significantly to environmental protection and have a substantial social impact in various ways. Here's a detailed insight:
Environmental Impact:
Reducing Waste: VICKERS filter elements are designed for durability and long-term use, which reduces the need for frequent replacements and, consequently, the amount of waste produced.
Preventing Contamination: By effectively filtering out contaminants from hydraulic fluids, these filter elements prevent harmful substances from entering the environment, thereby reducing environmental pollution.
Energy Efficiency: VICKERS filter elements contribute to the overall efficiency of hydraulic systems. More efficient systems consume less energy, which helps to reduce carbon emissions and combat climate change.
Recyclability: Some VICKERS filter elements are made from materials that can be recycled once the filter reaches the end of its life cycle, further reducing environmental impact.
Social Impact:
Promoting Sustainable Practices: By offering a product that is durable, efficient, and recyclable, VICKERS encourages sustainable practices in industries that use hydraulic systems. This helps to raise awareness about the importance of sustainability and encourages other companies to adopt similar practices.
Supporting Economic Growth: By improving the efficiency of machinery, VICKERS filter elements help to increase productivity in various industries, contributing to economic growth.
Job Creation: The production, installation, and maintenance of VICKERS filter elements provide job opportunities in various sectors, including manufacturing, engineering, and technical services.
Improving Quality of Life: By reducing environmental pollution and promoting energy efficiency, VICKERS filter elements contribute to a cleaner, healthier environment, which ultimately improves the quality of life for communities.
In conclusion, VICKERS filter elements have a significant positive impact on the environment and society. They promote sustainability, support economic growth, and contribute to a cleaner, healthier environment.
VICKERS filter elements play a crucial role in promoting sustainable development in society. Their contribution can be seen in several ways:
Promoting Resource Efficiency: VICKERS filter elements are designed for durability and long-term use. This reduces the need for frequent replacements, promoting efficient use of resources and reducing waste.
Energy Efficiency: By maintaining clean hydraulic fluids, VICKERS filter elements help ensure the efficient operation of machinery. This leads to less energy consumption, which is crucial in reducing greenhouse gas emissions and combating climate change.
Reducing Environmental Impact: VICKERS filter elements effectively filter out contaminants, preventing them from entering the environment. This reduces environmental pollution and helps to preserve natural ecosystems.
Supporting Industry: VICKERS filter elements are used in a variety of industries, including manufacturing, construction, and transportation. By improving the efficiency and longevity of machinery in these sectors, VICKERS supports sustainable industrial development.
Creating Sustainable Jobs: The production, installation, and maintenance of VICKERS filter elements provide job opportunities in sustainable manufacturing and services. This supports social sustainability by promoting economic growth and providing stable employment.
Education and Awareness: By promoting the benefits of their environmentally friendly and efficient products, VICKERS helps to raise awareness about the importance of sustainable practices in industry.
In conclusion, VICKERS filter elements contribute to sustainable development by promoting resource and energy efficiency, reducing environmental impact, supporting sustainable industrial growth, creating jobs, and raising awareness about sustainability. Through these actions, VICKERS is helping to create a more sustainable future for society.