A bag filter, also known as a baghouse or fabric filter, is an air pollution control device that removes particulates or gases released from commercial processes or combustion for electricity generation. They are widely used in various industries due to their efficiency in handling large volumes of gas.
Product Overview:
Design and Function: Bag filters consist of a series of fabric bags, also known as filter media, which are housed within a structure called a baghouse. As the dirty gas stream passes through these bags, the particulate matter is captured on the bag's surface, allowing clean air to pass through.
Types of Bag Filters: There are several types of bag filters, including pulse-jet, reverse-air, and shaker baghouses, each with its own method of cleaning the bags to maintain their filtering efficiency.
Material of Construction: The bags in a bag filter can be made from various materials, including polyester, polypropylene, aramid, and PTFE, depending on the application's specific requirements.
Applications: Bag filters are used in a wide range of industries, including power generation, steel mills, pharmaceutical production, chemical and petrochemical plants, and food manufacturers. They are particularly effective at controlling emissions in industries that produce large amounts of dust and other particulates.
Environmental Impact: By removing particulates and gases from industrial emissions, bag filters contribute to cleaner air and a healthier environment. They play a crucial role in helping industries meet environmental regulations regarding air pollution.
Efficiency: Bag filters are highly efficient, capable of removing particulates as small as 1 micron in size. They can achieve emission control efficiency up to 99%, depending on the application and the type of bag filter used.
In conclusion, bag filters are an essential tool in controlling industrial air pollution. Their versatile design, high efficiency, and wide range of applications make them a valuable asset in promoting cleaner air and a healthier environment.
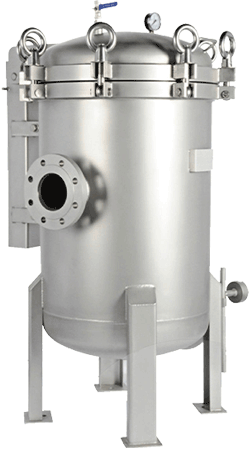
The efficiency of a bag filter is influenced by several factors:
Filter Material: The type of material used in the filter bag can significantly impact the filter's efficiency. Certain materials are better suited for certain types of particulates and gases, and the choice of material can also affect the filter's durability and resistance to wear and tear.
Particle Size: The size of the particles that need to be filtered can also affect the efficiency of the bag filter. Generally, bag filters are more effective at capturing larger particles. However, advancements in filter technology have made it possible to capture smaller particles as well.
Airflow Rate: The rate at which air flows through the filter can influence its efficiency. If the airflow rate is too high, it can lead to higher pressure drop and lower filtering efficiency. On the other hand, if the airflow rate is too low, it may not be able to capture all the particles.
Cleaning Method: The method used to clean the filter bags can also impact their efficiency. Some cleaning methods can damage the filter bags or reduce their ability to capture particles, while others can improve their efficiency by removing accumulated particles.
Operating Conditions: The efficiency of a bag filter can also be affected by the conditions in which it operates, such as temperature, humidity, and the presence of corrosive or abrasive substances in the air.
Maintenance: Regular maintenance and replacement of worn-out filter bags can greatly affect the efficiency of a bag filter. Neglecting maintenance can lead to decreased performance and efficiency over time.
In conclusion, the efficiency of a bag filter is influenced by a variety of factors, from the material of the filter bag to the conditions in which it operates. Understanding these factors is crucial for optimizing the performance of a bag filter.
The choice of material for a bag filter plays a significant role in its filtering efficiency. Here's how:
Particle Capture: Different materials have varying degrees of success in capturing particles. Some materials are better at trapping larger particles, while others are more effective with smaller particles. The choice of material can significantly influence the filter's ability to capture and retain particles of different sizes.
Durability: The material's durability can affect the filter's lifespan and, consequently, its efficiency over time. Some materials are more resistant to wear and tear, ensuring the filter maintains a high level of efficiency for a longer period.
Resistance to Conditions: The material's resistance to different operating conditions, such as temperature, humidity, and chemical exposure, can also impact the filter's efficiency. Some materials can withstand harsh conditions better than others, ensuring the filter remains efficient in various environments.
Air Permeability: The material's air permeability can impact the filter's airflow rate, which is a critical factor in its efficiency. Materials with high air permeability allow for a higher airflow rate, which can enhance the filter's efficiency by allowing it to process more air in less time.
Ease of Cleaning: Some materials are easier to clean than others. This can affect the filter's efficiency as a cleaner filter allows for better airflow and particle capture.
In conclusion, the choice of bag filter material can significantly impact its efficiency in various ways. It's crucial to choose a material that suits the specific requirements of the application for the best results.
The durability of the material used in a filter directly influences its lifespan. Here's how:
Wear and Tear: Materials that are more durable are better equipped to withstand the constant flow of particles that pass through the filter. Less durable materials may become worn or damaged over time, reducing their effectiveness and shortening the filter's lifespan.
Resistance to Environmental Conditions: Durable materials are typically more resistant to environmental conditions such as heat, moisture, and chemical exposure. This resistance can prolong the filter's lifespan by preventing damage from these conditions.
Maintenance and Cleaning: Durable materials can often withstand more rigorous or frequent cleaning, which is essential for maintaining the filter's performance over time. Materials that are less durable may degrade faster with regular cleaning, reducing the filter's lifespan.
Particle Accumulation: Over time, particles accumulate in the filter, which can cause damage if the material is not durable enough. More durable materials can withstand this accumulation better, maintaining their performance and extending the filter's lifespan.
Pressure Resistance: Filters are often subject to significant pressure from the flow of air or liquid. Durable materials are better able to resist this pressure without deforming or breaking, which can also extend the filter's lifespan.
In summary, the durability of the filter material is a key factor in determining the filter's lifespan. More durable materials can resist wear and tear, withstand environmental conditions, tolerate cleaning and maintenance, resist particle accumulation, and withstand pressure, all of which contribute to a longer filter lifespan.
A bag filter, also known as a fabric filter, is a device used to remove particulates from gas or air released from commercial processes or combustion for electricity generation. Here's how it works:
Particle Capture: The main principle of a bag filter is the interception and collection of particles from the gas or air stream passing through it. The bag filter is made of a fabric bag (filter medium) and a supporting cage, which keeps the bag open during filtration.
Filtration Process: In operation, the dirty air is drawn into the bag filter and directed towards the fabric bags. The particulate matter in the air is trapped on the surface of the fabric, while the clean air passes through the fabric and exits the filter.
Particle Accumulation: Over time, particles accumulate on the surface of the bag, forming a layer known as a filter cake. This layer actually improves the filtration efficiency as it acts as an additional barrier for incoming particles, causing them to adhere to the cake rather than the fabric itself.
Cleaning Mechanism: To maintain the bag filter's efficiency, the accumulated particles need to be removed regularly. This is done by a process called reverse pulse jet cleaning where compressed air is blown through the bag, dislodging the particles and allowing them to fall into a hopper for disposal.
Filter Replacement: Over time, the fabric bag will wear out and need to be replaced. The frequency of replacement depends on the durability of the fabric, the type of particles being filtered, and the frequency of cleaning.
In conclusion, a bag filter works by drawing air through a fabric bag, trapping particles on the surface, and periodically cleaning the bag to maintain its efficiency. The filter's effectiveness can be enhanced over time as particles accumulate on the surface, forming a filter cake that aids in additional filtration.
A bag filter, also known as a fabric filter or baghouse, is a versatile piece of equipment used in a wide array of industries for air pollution control. The main components of a bag filter and their functions are as follows:
Filter Bags: These are the heart of the bag filter system. The filter bags, made from various materials depending on the application, trap and separate particles from the gas stream. The quality and type of material used in the filter bags directly affect the system's efficiency and the life of the filter.
Bag Cages: These are metal structures designed to support the filter bags and prevent them from collapsing under the pressure of the incoming gas stream. They also help in maintaining the shape of the bags during the cleaning process.
Hopper: Located at the bottom of the bag filter, the hopper is designed to collect the particulate matter that has been separated from the gas stream. The particles fall into the hopper due to gravity after being shaken off the filter bags during the cleaning process.
Pulse Cleaning System: This is an essential part of a bag filter system. It uses compressed air to clean the filter bags. The sudden release of air causes a shock wave to travel up the filter bag, dislodging the accumulated dust cake which then falls into the hopper.
Inlet and Outlet Ducts: These are the channels through which the gas stream enters and exits the bag filter. The inlet duct directs the dirty gas stream into the bag filter, and the outlet duct carries the clean gas out of the system.
Housing/Shell: This is the outer structure that houses all the components of the bag filter. It is usually made of robust material to withstand the pressure and temperature of the gas stream.
Access Doors: These are designed for easy access to the interior parts of the bag filter for maintenance, inspection, and replacement of filter bags.
In conclusion, a bag filter consists of several components, each performing a crucial role in the filtration process. The filter bags and cages are the primary filtering components, the hopper collects the dislodged particles, the pulse cleaning system ensures the filter bags are cleaned, and the housing protects all the components. The inlet and outlet ducts control the flow of the gas stream, and the access doors provide access for maintenance and inspection.
Bag filters, also known as fabric filters or baghouses, are widely used in various industries for their efficiency in air pollution control. Here are some of the key advantages and strengths of bag filters:
High Efficiency: Bag filters can achieve extremely high efficiency in particle removal, often exceeding 99%. They are effective at capturing both large and very small particulate matter, including dust, pollen, and smoke.
Versatility: Bag filters can be used in a wide range of applications, from power plants and industrial manufacturing to pharmaceutical production and food processing. They can handle different types and volumes of gas streams.
Adaptable to Different Particles: The filter bags can be made from different materials, allowing them to be tailored to the specific type of particles to be filtered. This makes bag filters suitable for a variety of industries and applications.
Low Operating Costs: While the initial investment for a bag filter can be high, the operating costs are relatively low. The filter bags can be cleaned and reused multiple times before needing replacement, reducing the overall operational cost.
Environmental Compliance: Bag filters help industries meet stringent air quality regulations. By effectively removing particulate matter from exhaust gases, they prevent harmful pollutants from being released into the atmosphere.
Energy Efficient: Unlike some air pollution control devices, bag filters do not require a large amount of energy to operate, making them more energy-efficient and cost-effective in the long run.
Durability: Bag filters are designed to withstand harsh conditions, including high temperatures and pressures, making them a durable solution for air pollution control.
In conclusion, bag filters offer numerous advantages, including high efficiency, versatility, adaptability, low operating costs, environmental compliance, energy efficiency, and durability. These strengths make them a preferred choice for many industries looking to control air pollution.
When considering a bag filter for an industrial application, it's important to understand the technical parameters and specifications that determine its suitability and performance. These can vary greatly depending on the specific application and manufacturer, but generally include:
Filter Area: This refers to the total area of the filter bags available for filtration. A larger filter area allows for greater capacity and efficiency.
Air-to-Cloth Ratio: This is the ratio of the volume of gas (in cubic feet per minute) entering the bag filter to the area of filter fabric (in square feet). This ratio is crucial in determining the filter's efficiency and the life of the filter bags.
Inlet Gas Temperature: The temperature of the gas stream entering the bag filter is crucial, as it affects the performance of the filter bags. Different materials can withstand different temperatures, so it's important to choose the right material for your application.
Particle Size Distribution: The size and distribution of the particles in the gas stream can affect the performance of the bag filter. Bag filters are more efficient at capturing larger particles, but they can also capture smaller particles with the right filter material and design.
Pressure Drop: This is the difference in pressure between the inlet and outlet of the bag filter. A lower pressure drop indicates a more efficient filter.
Construction Material: The material used to construct the filter bags and the baghouse itself can greatly affect the performance and lifespan of the bag filter. It should be chosen based on the nature of the gas stream and the particles to be filtered.
Cleaning Mechanism: The type of cleaning mechanism used (e.g., pulse-jet, reverse-air, shaker) can affect the efficiency and maintenance requirements of the bag filter.
These are just some of the technical parameters and specifications to consider when choosing a bag filter. It's important to work closely with the manufacturer or supplier to ensure the bag filter is suitable for your specific application.
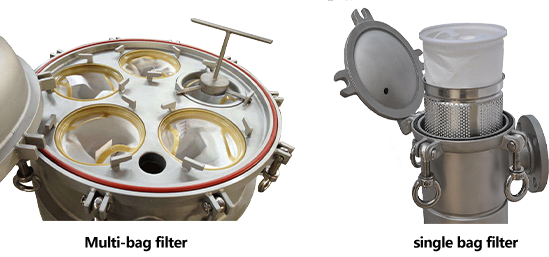
Bag filters, also known as fabric filters or baghouses, are versatile air pollution control devices used across a wide range of industries. Here are some of the key industries where bag filters find significant application:
Power Generation: In power plants, especially those using coal, bag filters are used to capture fly ash and other particulates from the flue gas before it is released into the atmosphere.
Cement Industry: Bag filters are extensively used in cement manufacturing plants to control dust emissions from various sources like crushers, mills, conveyors, and kilns.
Pharmaceutical Industry: In pharmaceutical production, bag filters are used to ensure clean and sterile air in the manufacturing process. They also help in controlling the emission of fine dust during the production of drugs.
Food and Beverage Industry: Bag filters are used in the food and beverage industry to control dust and other particulates during various processes like grinding, mixing, and packaging.
Metal and Mining Industry: In metal processing and mining operations, bag filters control the emission of dust and other harmful particulates, ensuring worker safety and environmental compliance.
Chemical Industry: Bag filters are used in chemical plants to control emissions from various processes, including reactors, dryers, and packaging lines.
Woodworking Industry: In woodworking facilities, bag filters control the dust generated during processes like cutting, sanding, and finishing.
Waste Management: In waste treatment facilities, bag filters are used to control the emission of dust and other particulates during waste processing and incineration.
In conclusion, bag filters play a crucial role in air pollution control across a wide range of industries. They not only help in maintaining a clean and safe working environment but also ensure compliance with environmental regulations.
Installing and maintaining a bag filter properly is crucial to its performance and longevity. Here are some steps and tips for bag filter installation and maintenance:
Installation:
Site Selection: Choose a location that allows for easy access for maintenance and inspection. The site should also be safe from any potential damage or interference.
Assembly: Depending on the size of the bag filter, it may need to be assembled on-site. Follow the manufacturer's instructions carefully to ensure correct assembly.
Connection: Connect the bag filter to the ductwork system. Ensure all connections are secure and airtight to prevent any leakage.
Testing: Once installed, run the system and check for any leaks or operational issues. Make any necessary adjustments before beginning regular operation.
Maintenance:
Regular Inspection: Regularly inspect the bag filter for any signs of wear or damage. This includes checking the filter bags for holes or tears, and the baghouse for any structural issues.
Cleaning: Depending on the type of bag filter, the filter bags will need to be cleaned periodically. This can be done using a variety of methods, including shaking, reverse air, or pulse jet cleaning.
Filter Bag Replacement: Over time, the filter bags will wear out and need to be replaced. Always replace with bags of the same material and size to ensure continued performance.
System Checks: Regularly check the entire system, including the ductwork and fan, for any issues. Any problems should be addressed immediately to prevent further damage or decreased performance.
Record Keeping: Keep detailed records of all maintenance activities. This can help identify any recurring issues and track the performance of the bag filter over time.
Remember, each bag filter system is unique and may have specific installation and maintenance requirements. Always follow the manufacturer's instructions and consult with a professional if you have any questions or concerns.
Ensuring a secure and airtight connection in a bag filter system is crucial to its overall performance and efficiency. Here are some steps you can follow to ensure the connections are safe and leak-free:
Proper Installation: The first step in ensuring a leak-free connection is proper installation. Make sure to follow the manufacturer's instructions carefully during installation. Ensure that all components are fitted correctly and securely.
Use of Seals: Using appropriate seals or gaskets at the connection points can help prevent air leakage. The type of seal used will depend on the specific application and operating conditions.
Regular Inspection: Regularly inspect all connection points for signs of wear or damage that could lead to leaks. This includes checking for cracks, loose fittings, or worn seals.
Leak Testing: Perform periodic leak testing to detect any leaks that may not be visible during a routine inspection. This can be done using various methods such as pressure testing, soap bubble testing, or using a handheld leak detector.
Proper Maintenance: Regular maintenance is key to maintaining a leak-free connection. This includes replacing worn or damaged components, tightening loose fittings, and replacing seals as needed.
Professional Assistance: If you are unsure about the integrity of the connection, don't hesitate to seek professional assistance. A professional can thoroughly inspect the connection, perform leak testing, and make any necessary repairs or adjustments.
By following these steps, you can ensure that your bag filter system remains secure and airtight, thereby maximizing its performance and efficiency.