The Brush Type Self-Cleaning Filter is an innovative and efficient solution designed for optimal filtration in various applications. This product is a result of cutting-edge technology and high-quality materials, ensuring a robust and reliable filtration system.
The primary function of the Brush Type Self-Cleaning Filter is to remove solid impurities from the liquid. It does this through its unique self-cleaning mechanism. The filter brushes, which are part of the internal assembly, move across the filter screen, dislodging any accumulated particles. This self-cleaning process ensures that the filter maintains its efficiency and longevity, reducing the need for frequent maintenance and replacement.
The filter is crafted from durable materials, ensuring its resistance to corrosion and wear. It is capable of handling high-pressure and high-temperature environments, making it suitable for various industrial applications.
Furthermore, the Brush Type Self-Cleaning Filter is equipped with an automatic control system. This system triggers the cleaning process based on pressure differential or time, ensuring that the filter operates at its optimal capacity at all times.
In summary, the Brush Type Self-Cleaning Filter is a high-performance, low-maintenance solution for effective filtration. Its automatic cleaning feature, durability, and versatility make it an excellent choice for a wide range of applications.

The automatic cleaning process of the Brush Type Self-Cleaning Filter is triggered by either a pressure differential or a timer.
Pressure Differential: The filter is equipped with pressure sensors on both the inlet and outlet. These sensors monitor the pressure levels continuously. When the pressure differential (the difference in pressure between the inlet and the outlet) reaches a preset value, it indicates that the filter screen is becoming clogged with impurities. This triggers the automatic cleaning process. The brushes start to move across the filter screen, dislodging the accumulated particles and restoring the pressure balance.
Timer: The filter can also be set to clean at regular intervals, regardless of the pressure differential. This is particularly useful in applications where the liquid has a high solid content and the filter is likely to get clogged frequently. The timer can be adjusted according to the specific requirements of the application.
Once the cleaning process is triggered, the motor drives the brush assembly to rotate. The brushes sweep across the filter screen, removing the accumulated particles. These particles are then flushed out through the drain valve, ensuring that the filter remains clean and efficient.
In conclusion, the automatic cleaning process of the Brush Type Self-Cleaning Filter is a smart and efficient feature that ensures optimal filtration performance and extends the lifespan of the filter.
The Brush Type Self-Cleaning Filter operates on a unique and efficient principle that ensures optimal filtration and automatic cleaning. Here's a detailed description of its working principle:
Filtration Process: The unfiltered liquid enters the filter through the inlet. The liquid then flows through the filter screen, which is designed to capture solid impurities. The filtered liquid exits the filter through the outlet, leaving the impurities trapped on the inner surface of the filter screen.
Detection of Pressure Differential: The filter is equipped with pressure sensors at the inlet and outlet. These sensors continuously monitor the pressure levels. When the pressure differential (the difference between the inlet and outlet pressure) reaches a preset value, it indicates that the filter screen is getting clogged with impurities.
Triggering of Cleaning Process: Once the pressure differential reaches the preset value, the automatic cleaning process is triggered. Alternatively, the cleaning process can also be triggered at regular intervals set by a timer, regardless of the pressure differential.
Cleaning Process: The cleaning process involves the rotation of the brush assembly driven by the motor. The brushes move across the filter screen, dislodging the trapped particles. This process restores the pressure balance and ensures the continued efficiency of the filtration process.
Disposal of Impurities: The dislodged particles are carried by the flow of the liquid to the drain chamber. From here, they are flushed out through the drain valve, leaving the filter clean and ready for the next filtration cycle.
In a nutshell, the Brush Type Self-Cleaning Filter provides an efficient and effective filtration solution. Its automatic cleaning feature ensures that the filter operates at its optimal capacity at all times, reducing the need for manual cleaning and maintenance.
The Brush Type Self-Cleaning Filter is a sophisticated piece of equipment designed to filter impurities from various types of liquids. Its major components and their functions are as follows:
Filter Housing: This is the outer structure that holds all other components. It is usually made of robust materials like stainless steel to withstand the pressure of the liquid flow and the harsh environment of industrial applications.
Filter Screen: This is the core component where the actual filtration happens. The filter screen is a mesh-like structure with tiny holes that allow the liquid to pass through while trapping solid impurities. The size of the holes can vary depending on the specific filtration requirements.
Pressure Sensors: These are located at the inlet and outlet of the filter. They continuously monitor the pressure levels of the incoming and outgoing liquid. When the pressure differential reaches a preset value, it triggers the automatic cleaning process.
Brush Assembly: This consists of a set of brushes attached to a rotating shaft. When the cleaning process is triggered, the brush assembly rotates, and the brushes sweep across the filter screen, dislodging the trapped particles.
Motor: This is the driving force of the brush assembly. It rotates the brush assembly when the cleaning process is triggered.
Drain Chamber and Valve: The dislodged particles are carried by the liquid flow to the drain chamber. They are then flushed out through the drain valve, ensuring that the filter remains clean and ready for the next filtration cycle.
Control Unit: This is the brain of the filter. It receives signals from the pressure sensors, controls the operation of the motor, and manages the opening and closing of the drain valve. It can also be programmed to trigger the cleaning process at regular intervals.
In summary, the Brush Type Self-Cleaning Filter is a smart and efficient filtration solution. Each component plays a crucial role in ensuring optimal filtration performance, automatic cleaning, and minimal maintenance.
The Brush Type Self-Cleaning Filter is a versatile device that can be used in a variety of applications involving different types of liquids. Here are some examples:
Water Treatment: The filter can be used in both municipal and industrial water treatment plants to remove solid impurities from water. This includes prefiltration for reverse osmosis systems, where the filter can protect the delicate RO membranes from damage caused by larger particles.
Electro-Chlorination Systems: In these systems, the filter can be used to ensure that the electrolysis process is not affected by solid impurities in the brine solution.
Energy Production: The filter can be used to protect the seals of Pelton, Francis, or Kaplan turbines in hydroelectric power plants. By filtering out solid particles, the filter can prevent damage to the turbines and improve their efficiency.
Food and Beverage Industry: The filter can be used to remove solid impurities from various types of beverages and liquid food products, ensuring their quality and safety.
Chemical Industry: The filter can be used in various chemical processes where a clean liquid is required. This includes the production of paints, dyes, resins, and many other chemical products.
Oil and Gas Industry: The filter can be used to remove solid impurities from crude oil, natural gas, and other petroleum products. This can improve the efficiency of downstream processes and extend the life of the equipment.
In summary, the Brush Type Self-Cleaning Filter is a highly versatile device that can be used in a wide range of applications involving various types of liquids. Its automatic cleaning feature makes it particularly suitable for applications where continuous operation is required.
The Brush Type Self-Cleaning Filter holds numerous advantages and strengths that make it a sought-after choice in many industries. Here are some of the key benefits:
Continuous Operation: The self-cleaning feature of the filter allows for continuous operation without the need for frequent manual cleaning. This not only saves time but also reduces the risk of operational downtime.
High Filtration Efficiency: The brush type self-cleaning filter is capable of removing a wide range of particle sizes, ensuring a high level of purity in the filtered liquid. This makes it suitable for applications where high filtration efficiency is required.
Reduced Maintenance: The automatic cleaning process reduces the need for regular maintenance, which can save costs and manpower. The robust design of the filter also contributes to its long lifespan, further reducing the total cost of ownership.
Versatility: The filter can be used with a wide variety of liquids, making it suitable for a broad range of applications in different industries. It can handle everything from water to oil, beverages, and chemical solutions.
Improved Product Quality: By ensuring a high level of purity in the filtered liquid, the brush type self-cleaning filter can contribute to the production of high-quality products. This is particularly important in industries like food and beverage, pharmaceuticals, and chemicals where product quality is paramount.
Environmentally Friendly: The filter's self-cleaning process reduces waste as it only disposes of the particles it filters out. This makes it a more environmentally friendly option compared to disposable filters.
Energy Efficiency: The filter operates on a low power motor, making it an energy-efficient choice. This can contribute to lower energy costs and a smaller environmental footprint.
In conclusion, the Brush Type Self-Cleaning Filter combines efficiency, versatility, and cost-effectiveness, making it an excellent choice for a wide range of filtration applications.
The energy consumption of the Brush Type Self-Cleaning Filter is relatively low, making it an energy-efficient choice for various applications. Here's why:
Low Power Motor: The filter operates on a low power motor that is only activated during the cleaning cycle. This intermittent operation keeps overall energy consumption low.
Efficient Design: The filter's design is optimized for efficient operation. The brush mechanism dislodges particles effectively, ensuring that the cleaning cycle is quick and consumes minimal energy.
Reduced Pumping Energy: By maintaining a clean filter surface, the filter reduces the energy required for pumping the liquid through the filter. This can result in significant energy savings, especially in applications with high flow rates.
Lower Maintenance Energy: The automatic cleaning feature of the filter reduces the need for manual cleaning. This not only saves labor but also the energy that would be used in manual cleaning processes.
Energy Recovery: In some designs, the energy from the backwash water can be recovered and reused, further reducing the overall energy consumption.
In conclusion, the Brush Type Self-Cleaning Filter is a highly energy-efficient filtration solution. Its low energy consumption contributes to its cost-effectiveness and makes it a sustainable choice for various applications.
The cleaning cycle of a Brush Type Self-Cleaning Filter varies depending on several factors. Here's a detailed explanation:
Contaminant Load: The primary factor that determines the cleaning cycle is the load of contaminants in the fluid being filtered. High contaminant loads will require more frequent cleaning cycles.
Filter Size and Type: The size and type of the filter also impact the cleaning cycle. Larger filters or those designed for more challenging applications may have longer cleaning cycles.
Filter Setting: Most Brush Type Self-Cleaning Filters have adjustable settings that allow the cleaning cycle to be set according to specific needs. This could range from several times a day to once every few days.
Operating Conditions: The operating conditions, such as flow rate and pressure, can also affect the cleaning cycle. Higher flow rates or pressures may require more frequent cleaning.
In general, a Brush Type Self-Cleaning Filter is designed to initiate its cleaning cycle when the pressure drop across the filter reaches a preset level, indicating that the filter is becoming clogged with particles. The cleaning cycle is then automatically activated, and the filter is cleaned within a few minutes without interrupting the flow of fluid.
It's important to note that the exact cleaning cycle for a specific filter should be determined in consultation with the filter manufacturer or a qualified engineer, taking into account the specific application and operating conditions.
The Brush Type Self-Cleaning Filter is a highly efficient and advanced filtration system. Here are the technical parameters and specifications:
Service Pressure: The filter operates effectively within a service pressure range of 0.2 to 2.5MPa, accommodating a variety of application requirements.
Filter Element Material: The filter elements are typically made from robust and corrosion-resistant materials like 304, 316L, and 2205. These materials ensure the longevity and reliability of the filter.
Diameter Specifications: The diameter of these filters can range from DN50 to DN600, allowing for a wide range of flow rates.
Cleaning Time: The cleaning cycle of these filters typically ranges from 20 to 60 seconds, ensuring that the filter surface is quickly cleared of particles without interrupting the fluid flow.
Filtration Precision: These filters offer a filtration precision range from 50 to 5000 microns. This wide range allows for precise tuning to meet specific filtration requirements.
Maximum Operating Pressure: The maximum operating pressure is around 10Bar, which allows for use in high-pressure applications.
Working Temperature: The filter can operate effectively in temperatures ranging from 0 to 65 degrees Celsius.
Backwashing Flow: The backwashing flow is around 50 to 70 cubic meters per hour, ensuring that the filter is thoroughly cleaned during each cleaning cycle.
Backwashing Water Consumption: Each backwashing cycle consumes about 200 to 300 liters of water, which is less than 0.5% of the effluent.
Flow Rate: The flow rate can go up to 4000 cubic meters per hour, accommodating high flow rate applications.
These specifications make the Brush Type Self-Cleaning Filter a versatile and efficient solution for various filtration applications. However, it's important to consult with the manufacturer or a qualified engineer to determine the most suitable specifications for a specific application.
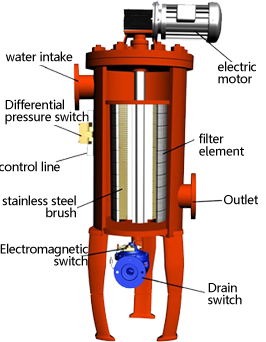
The Brush Type Self-Cleaning Filter is versatile and finds extensive application across various industries. Here's a detailed overview:
Agricultural Irrigation: The filters are used to remove solid particles from water, ensuring clean and safe water for irrigation purposes. This helps in maintaining soil health and promoting better crop growth.
Raw Water Treatment: These filters are crucial in the initial stages of water treatment processes where they help remove large particulates from raw water sources like rivers, lakes, or wells.
Industrial Recycled Water Filtration: Industries often recycle water for various processes. The filters help in removing impurities from the recycled water, making it safe for reuse.
Cooling Water Treatment: In industries where machinery is used, cooling water is often required to keep the machines from overheating. The filters help in cleaning the cooling water, ensuring the longevity and efficiency of the machines.
Paper Industry: The paper industry requires a large amount of water during the production process. The filters are used to ensure the water used is free from impurities, leading to higher quality paper products.
Plastic Industry: The plastic industry uses these filters to ensure the water used in cooling and other processes is clean, which contributes to the production of high-quality plastic products.
Power Industry: Power plants, especially thermal power plants, use a large amount of water for cooling purposes. The filters help in treating the water to ensure it is safe for use and does not harm the machinery.
Oil and Gas Industry: These filters are used in the oil and gas industry to filter out impurities from the water used in various processes, ensuring the efficient operation of equipment and the quality of the end product.
Chemical Processing: The filters play a crucial role in the chemical industry where they are used to filter out solid particles from liquids, ensuring pure and safe chemicals for use in various applications.
Automotive Industry: In the automotive industry, these filters are used in the treatment of water used in various processes like painting, cooling, and washing, ensuring the production of high-quality vehicles.
The above applications underline the versatility and efficiency of Brush Type Self-Cleaning Filters in various industrial applications. However, the specific use of these filters can vary based on the unique requirements of each industry.
The Brush Type Self-Cleaning Filter is relatively easy to install and maintain. Here's a detailed explanation:
Installation:
Positioning: The filter should be installed in a location that allows easy access for maintenance and inspection. It should also be installed in a way that the flow of fluid is in the direction indicated on the filter body.
Piping: The filter should be connected to the system piping using suitable fittings. The piping should be properly supported to avoid placing undue stress on the filter connections.
Electrical Connections: The filter's control system requires an electrical connection. This should be carried out by a qualified electrician in accordance with local electrical codes.
Initial Startup: Before starting the filter for the first time, ensure that the system is properly pressurized and that all connections are secure.
Maintenance:
Regular Inspection: Most Brush Type Self-Cleaning Filters only need to be inspected every six months. During this inspection, the internal brush mechanism should be checked to ensure it is rotating properly.
Cleaning: If the filter is not self-cleaning or if the self-cleaning mechanism is not functioning properly, the filter screen should be manually cleaned. This involves removing the screen and cleaning it with a suitable cleaning agent.
Replacement of Parts: Over time, some parts of the filter may wear out and need to be replaced. This includes the filter screen, seals, and the brush mechanism. Always use genuine replacement parts to ensure the continued efficient operation of the filter.
Troubleshooting: If the filter is not operating as expected, consult the troubleshooting guide in the filter's manual or contact the manufacturer for assistance.
Remember, while the Brush Type Self-Cleaning Filter is designed for easy maintenance, it's always important to consult the manufacturer's manual or a qualified engineer for specific installation and maintenance procedures.