The Multi Cartridges Self-Cleaning Filter is a state-of-the-art filtration system designed for optimal performance and minimal maintenance. This innovative product is built with multiple cartridges, each serving a unique role in the filtration process.
The system operates by directing the flow of water or other fluids through a series of cartridges. Each cartridge is designed to catch and hold different types and sizes of particles, ensuring a thorough and comprehensive filtration process. The cartridges are arranged in a manner that allows for the maximum surface area to be exposed to the fluid, thereby increasing the efficiency of the filtration process.
One of the standout features of the Multi Cartridges Self-Cleaning Filter is its self-cleaning mechanism. This feature allows the system to automatically clean itself, eliminating the need for manual cleaning and significantly reducing maintenance time. The self-cleaning process is triggered when the system detects a certain level of particle accumulation on the cartridges. It then initiates a backwashing process, where the flow of fluid is reversed, effectively dislodging the trapped particles and flushing them out of the system.
In addition to its superior filtration and self-cleaning capabilities, the Multi Cartridges Self-Cleaning Filter is also designed for easy installation and operation. It is built with durable materials to withstand harsh environmental conditions and ensure a long service life.
In conclusion, the Multi Cartridges Self-Cleaning Filter is an advanced filtration solution that offers high efficiency, low maintenance, and long-lasting durability. It is an ideal choice for applications that require reliable and effective filtration.
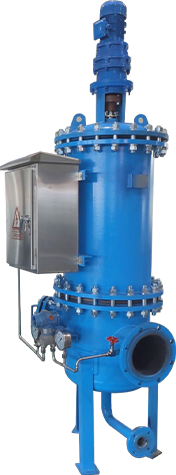
The operation of the Multi Cartridges Self-Cleaning Filter is a combination of sophisticated engineering and innovative design. Here's a detailed breakdown of how the multiple cartridges in this system work:
Inlet Flow: The process begins when the fluid enters the filter through an inlet. This fluid could be water, oil, or any other liquid that needs filtration.
Filtration Process: The fluid then flows through the multiple cartridges housed within the filter. Each cartridge is designed with a specific pore size to trap different types and sizes of particles. The cartridges work in tandem to ensure comprehensive filtration. The larger particles get trapped in the initial cartridges, while the smaller particles are caught by the subsequent cartridges. This sequential filtration process ensures a high level of purity in the filtered fluid.
Self-Cleaning Mechanism: Over time, the cartridges will accumulate particles, which could potentially clog the system. However, the Multi Cartridges Self-Cleaning Filter is equipped with a self-cleaning mechanism to prevent this. The system uses sensors to detect when the cartridges are reaching their particle capacity. Once this level is reached, the self-cleaning process is triggered.
Backwashing Process: The self-cleaning process involves a technique known as backwashing. In this process, the flow of the fluid is reversed, creating a backflow that dislodges the trapped particles from the cartridges. These particles are then flushed out of the system through a waste outlet.
Continuous Operation: Once the self-cleaning process is completed, the filter resumes its normal operation. This entire process is automatic, requiring no manual intervention. It ensures that the filter maintains its efficiency and performance, providing consistently high-quality filtration.
In conclusion, the multiple cartridges in the Multi Cartridges Self-Cleaning Filter work together to provide a thorough and efficient filtration process. The automatic self-cleaning feature ensures the system remains in optimal condition, providing reliable and effective filtration for a wide range of applications.
The detection of particle capacity in the cartridges of a self-cleaning filter is an integral part of its operation. This process is typically managed by a combination of sensors and software algorithms designed to monitor and respond to changes in the filter's performance. Here's a more detailed explanation:
Pressure Differential Monitoring: The most common method used to determine when a filter cartridge needs cleaning is by monitoring the pressure differential across the filter. Under normal operation, the pressure difference between the inlet and the outlet of the filter is relatively low. As the filter cartridges begin to accumulate particles, the flow of fluid through the filter becomes restricted, causing an increase in the pressure differential.
Sensors: The filter system is equipped with pressure sensors located at the inlet and outlet. These sensors continuously monitor the pressure levels and relay this information to the filter's control system.
Control System: The control system is programmed with a threshold value for the pressure differential. When the pressure differential exceeds this value, it is an indication that the filter cartridges have reached their particle capacity and need to be cleaned.
Triggering the Self-Cleaning Process: Once the control system receives this signal, it initiates the self-cleaning process. The backwashing cycle is triggered, and the accumulated particles are flushed out of the system.
Continuous Monitoring: After the self-cleaning process, the pressure differential should return to its normal range. The system continues to monitor the pressure levels, ready to initiate another cleaning cycle when necessary.
In summary, the detection of particle capacity in the cartridges of a self-cleaning filter is a dynamic process that relies on continuous pressure monitoring and intelligent control systems. This ensures the filter maintains optimal performance and longevity.
The Multi Cartridges Self-Cleaning Filter is a sophisticated piece of filtration technology designed to provide high-quality filtration while reducing maintenance requirements through its self-cleaning feature. Here's a detailed, original explanation of how it works:
Inlet Flow: The operation begins when the fluid enters the filter through an inlet. The fluid could be any liquid that requires filtration, such as water, oil, etc.
Filtration Process: The liquid then flows through a series of cartridges contained within the filter. Each cartridge is designed with a specific pore size to capture different types and sizes of particles. The cartridges work together to ensure thorough filtration. The larger particles are trapped by the initial cartridges, while the smaller particles are captured by the later cartridges. This sequential filtration process ensures that the filtered fluid is of high purity.
Particle Capacity Detection: As particles accumulate in the cartridges, it could potentially lead to clogging. To prevent this, the filter is equipped with pressure sensors that monitor the pressure differential across the filter. When the pressure differential exceeds a set threshold, it indicates that the cartridges have reached their particle capacity and triggers the self-cleaning mechanism.
Self-Cleaning Mechanism: The self-cleaning process involves a technique known as backwashing. In this process, the flow of fluid is reversed, creating a backflow that dislodges the trapped particles from the cartridges. These particles are then expelled from the system through a waste outlet.
Continuous Operation: Once the self-cleaning process is complete, the filter returns to its normal operation. This entire process is automatic and requires no manual intervention. This ensures that the filter consistently performs at a high level of efficiency, providing high-quality filtration.
In conclusion, the Multi Cartridges Self-Cleaning Filter is an advanced filtration system that provides efficient and thorough filtration. Its automatic self-cleaning feature ensures the system remains effective and reliable, making it ideal for a wide range of applications.
The Multi Cartridges Self-Cleaning Filter is an advanced filtration system designed to provide high-quality filtration and reduce maintenance needs. Here's an original, detailed explanation of its composition and functions:
Filter Housing: The filter housing is the outer casing that holds all the other components. It's typically made of robust materials like stainless steel to withstand pressure and ensure durability.
Cartridges: Inside the housing are multiple filter cartridges. Each cartridge is designed to trap different types and sizes of particles, providing comprehensive filtration. The cartridges are typically made of materials like polypropylene or polyester, which are known for their excellent filtration properties and chemical resistance.
Inlet and Outlet: The filter has an inlet through which the fluid to be filtered enters, and an outlet through which the filtered fluid exits. These are strategically positioned to ensure efficient flow and filtration.
Pressure Sensors: The filter is equipped with pressure sensors at the inlet and outlet. These sensors monitor the pressure differential across the filter. When the pressure differential exceeds a set threshold, it indicates that the cartridges are full and triggers the self-cleaning process.
Control System: The control system is the "brain" of the filter. It receives data from the pressure sensors and initiates the self-cleaning process when necessary. It can also be programmed to perform the cleaning process at set intervals.
Self-Cleaning Mechanism: Once the control system triggers the self-cleaning process, a backwashing cycle begins. The flow of fluid is reversed, dislodging the trapped particles from the cartridges. These particles are then expelled from the system through a waste outlet.
Waste Outlet: The waste outlet is where the dislodged particles are expelled during the self-cleaning process. This ensures that the filter system remains clean and efficient.
In conclusion, the Multi Cartridges Self-Cleaning Filter is a comprehensive filtration system. Its multiple cartridges provide thorough filtration, while the self-cleaning mechanism ensures longevity and consistent performance. This system is ideal for applications where high-quality filtration is required, and maintenance needs to be kept to a minimum.
The filter cartridges in a self-cleaning filter can be made from a variety of materials, depending on the specific requirements of the filtration process. Some of the most common materials include:
Polypropylene: This is a popular choice due to its chemical resistance and affordability. Polypropylene cartridges are often used in water filtration systems as they are effective at removing sediment, dirt, and other particulate matter.
Ceramic: Ceramic cartridges are known for their ability to filter out very small particles, even bacteria and viruses. They are often used in drinking water filtration systems.
Stainless Steel: In some cases, particularly in industrial applications, the cartridges might be made from stainless steel. These are durable and can withstand high temperatures and pressures.
Carbon: Carbon cartridges are used when the goal is to remove chemicals, such as chlorine, from the water. They are often used in combination with other types of cartridges to provide comprehensive filtration.
Pleated Fabric or Polyester: These materials are used when a larger surface area is needed for filtration. They are effective at trapping a wide range of particle sizes.
The specific material used will depend on the nature of the liquid being filtered, the size of the particles to be removed, and the desired longevity of the cartridge. It's always best to consult with the manufacturer or a filtration expert to determine the best material for a specific application.
Different materials used in filter cartridges are designed to handle different types of filtration processes. Here's a breakdown:
Polypropylene: Polypropylene is a versatile material that's suitable for a wide range of applications. It's particularly effective for sediment filtration, where it can remove dirt, rust, sand, and other particulates from water. It's often used in pre-filtration stages in various industries, including food and beverage, pharmaceuticals, and water treatment.
Ceramic: Ceramic filters are best for microfiltration processes. They have very small pores that can filter out bacteria, cysts, and other microorganisms, making them ideal for purifying drinking water. They're also used in medical and laboratory applications.
Stainless Steel: Stainless steel cartridges are robust and durable, making them suitable for demanding industrial applications. They can handle high pressures and temperatures, and are often used for filtration processes involving oils, chemicals, and high-temperature liquids.
Carbon: Carbon cartridges are used in adsorption processes, where contaminants are attracted and held onto the surface of the carbon. They're effective at removing chlorine, volatile organic compounds (VOCs), taste and odor from water. They're commonly used in drinking water treatment, as well as in the food and beverage industry.
Pleated Fabric or Polyester: These materials have a large surface area, which makes them effective at trapping a wide range of particle sizes. They're often used in pre-filtration stages to protect more expensive filters downstream. They can be used in a variety of industries, including pharmaceuticals, food and beverage, and chemicals.
Remember, the best material for a filter cartridge depends on the specific requirements of the filtration process, including the type of liquid, the size and type of contaminants, and the required flow rate.
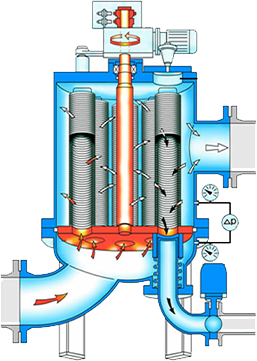
A Multi Cartridges Self-Cleaning Filter is a sophisticated piece of equipment designed for efficient filtration in various applications. Here are some of the general technical specifications and features that you might find in such a system:
Technical Specifications:
Shell Material: The shell of these filters is often made from Q235 or 304 stainless steel. These materials are highly durable and resistant to corrosion, ensuring the longevity of the filter system.
Filter Screen Material: The filter screen is typically made from 304 stainless steel, offering excellent resistance to wear and tear and providing efficient filtration.
Working Pressure: The working pressure of these systems can vary, but a maximum working pressure of around 125 psi (8.6 bar) is common.
Filtration Degree: Depending on the specific model and application, these filters can offer filtration degrees as low as 50 microns.
Flow Rate: The flow rate will depend on the specific model and the number of cartridges in the system. Some models can handle flow rates up to 280m3/hr or even higher.
Features:
Automatic Operation: These systems often feature automatic operation, reducing downtime and maintenance costs.
Self-Cleaning Mechanism: The self-cleaning feature ensures that the filter remains efficient and effective over time, without the need for frequent manual cleaning.
Modular Design: Some models offer a modular design, which makes it easy to expand the system's capacity if needed.
Versatility: These filters are suitable for a wide range of applications, including water treatment, food and beverage production, pharmaceutical manufacturing, and more.
Please note that the exact specifications and features can vary between different models and manufacturers. Always refer to the specific product documentation for accurate information.
Multi Cartridges Self-Cleaning Filters offer several advantages that make them an excellent choice for various filtration applications. Here are some of their key benefits:
Efficient Filtration: With multiple cartridges, these filters offer a large filtration area, ensuring efficient and thorough filtration of the fluid. This results in high-quality output and improved performance of the subsequent processes or equipment.
Self-Cleaning Mechanism: One of the standout features of these filters is their self-cleaning mechanism. This feature reduces the need for manual cleaning and maintenance, saving time and labor costs. It also ensures consistent filtration performance over time.
Continuous Operation: Thanks to the self-cleaning feature, these filters can operate continuously without the need for frequent shutdowns for cleaning or maintenance. This leads to increased productivity and reduced downtime.
Versatility: Multi Cartridges Self-Cleaning Filters are suitable for a wide range of applications. They can handle various types of fluids and are effective at removing a wide range of contaminants. This makes them a versatile solution for many industries, including water treatment, food and beverage, pharmaceuticals, and more.
Durable and Robust: Typically made from high-quality materials like stainless steel, these filters are designed to withstand harsh operating conditions and provide a long service life. This makes them a cost-effective solution in the long run.
Modular Design: Some models offer a modular design, which allows for easy expansion of the system's capacity as needed. This can be a significant advantage for businesses that anticipate growth in the future.
Improved Product Quality: By ensuring efficient and consistent filtration, these filters can help improve the quality of the final product, whether it's purified water, a beverage, a pharmaceutical product, or any other output.
Remember, the exact benefits can vary depending on the specific model and application. Always refer to the product documentation and consult with the manufacturer or supplier to understand the potential advantages in your specific context.
Multi Cartridges Self-Cleaning Filters are versatile pieces of equipment that can be used in a wide range of industries due to their efficient and reliable filtration capabilities. Here are some of the key sectors where these filters are commonly used:
Water Treatment: These filters are often used in water treatment plants for the removal of sediment, particulates, and other contaminants from water. Their self-cleaning feature ensures consistent water quality and reduces maintenance requirements.
Food and Beverage Industry: In the food and beverage industry, these filters are used to ensure the safety and quality of products. They can be used for the filtration of water, juices, wines, oils, and other liquids used in food and beverage production.
Pharmaceutical Industry: The pharmaceutical industry has strict standards for purity and cleanliness. Multi Cartridges Self-Cleaning Filters can help meet these standards by efficiently filtering out contaminants from liquids used in pharmaceutical production.
Chemical Industry: These filters are used in the chemical industry to filter out impurities from various chemical solutions. Their robust construction allows them to withstand harsh chemicals and high temperatures.
Oil and Gas Industry: In the oil and gas industry, these filters are used for the filtration of fuels, lubricants, and other petroleum products. They help in removing particulates and other impurities, ensuring the efficient operation of equipment and machinery.
Pulp and Paper Industry: These filters can be used to filter out impurities from water and other liquids used in the pulp and paper industry, helping to improve the quality of the final product.
Electronics Industry: In the electronics industry, these filters are used in the production of semiconductors and other electronic components, where high-purity water is required.
Agriculture: They can also be used in irrigation systems to filter out sediment and other particles from water, protecting the irrigation equipment from damage and ensuring efficient water usage.
These are just a few examples of the many industries where Multi Cartridges Self-Cleaning Filters can be used. Their versatility, efficiency, and self-cleaning capabilities make them a valuable asset in any application that requires reliable and efficient filtration.
The installation and maintenance of a Multi Cartridges Self-Cleaning Filter are crucial processes that ensure the efficient operation and longevity of the system. Here are some guidelines:
Installation:
Location: Choose a suitable location for the filter that allows easy access for maintenance and has enough space for the system.
Orientation: The filter should be installed in the correct orientation as indicated by the manufacturer. Incorrect installation can affect the performance of the filter and its self-cleaning mechanism.
Piping: Connect the filter to the piping system as per the manufacturer's instructions. Ensure that the connections are secure to prevent leaks.
Electrical Connections: If the filter has an automatic self-cleaning system, it will need to be connected to a power source. Make sure to follow the manufacturer's instructions for the electrical connections.
System Check: Once the installation is complete, perform a system check to ensure that the filter is working correctly. Check for leaks and make sure the self-cleaning system is functioning properly.
Maintenance:
Regular Inspection: Regularly inspect the filter for signs of wear and tear. Check the filter cartridges and replace them if necessary.
Cleaning: Although the filter has a self-cleaning mechanism, it may still need to be manually cleaned periodically. Follow the manufacturer's instructions for cleaning the filter.
Cartridge Replacement: The filter cartridges will need to be replaced periodically. The frequency will depend on the quality of the fluid being filtered and the usage of the filter.
System Check: Regularly check the entire system, including the piping and electrical connections, for any issues. Address any problems immediately to prevent damage to the filter or the system it's connected to.
Professional Service: For complex maintenance tasks or if you encounter any problems with the filter, it may be best to call in a professional service technician.
Remember, the specific installation and maintenance procedures can vary depending on the specific model of the filter and the manufacturer's guidelines. Always refer to the product manual or consult with the manufacturer for accurate information.