An air compressor air filter element is an integral component of an air compressor system, designed to remove contaminants and impurities from the air before it enters the compressor. Here's a brief overview of this product:
Design and Function:
The air filter element is typically made of a pleated material, such as paper, cotton, or synthetic fibers, which provides a large surface area to capture and hold particles. Its primary function is to protect the air compressor from damage caused by dirt, dust, and other airborne particles.
The air filter element is housed in the air filter assembly, which is typically located on the intake side of the air compressor. As air is drawn into the compressor, it passes through the filter element, which traps and holds the particles.
Benefits:
Prolonged Equipment Life: By removing contaminants from the air, the air filter element helps to prevent wear and tear on the compressor's internal components, extending the lifespan of the equipment.
Improved Performance: Clean, filtered air allows the compressor to operate more efficiently, improving performance and reducing energy consumption.
Reduced Maintenance: Regular replacement of the air filter element can reduce the need for more extensive maintenance and repairs.
In summary, the air compressor air filter element is a crucial part of maintaining the health and efficiency of an air compressor system. It's a small component with a significant impact, providing protection for the compressor and ensuring optimal performance.

The primary materials used in the construction of an air compressor air filter element are as follows:
Filter Media: The most critical component of the filter element is the filter media, which is responsible for trapping and holding contaminants. The filter media is typically made from a pleated material to increase its surface area. The most common materials used are paper, cotton, or synthetic fibers. High-quality filter elements may use a glass fiber material because of its excellent filtration properties and durability.
End Caps: The end caps of the filter element are usually made of metal or a durable plastic. They serve to secure the filter media in place and provide a seal to prevent unfiltered air from bypassing the filter media.
Center Tube: The center tube provides support to the filter media and allows air to flow through the filter. It is typically made of a sturdy metal to withstand the pressure of the air flow.
Gasket: The gasket provides a tight seal between the filter element and the filter housing to prevent unfiltered air from leaking into the compressor. It is typically made of a flexible material like rubber or silicone.
These materials collectively ensure the efficient operation of the air compressor air filter element, providing optimal filtration and protection for the air compressor system.
The center tube of an air filter element plays a crucial role in the overall functionality and efficiency of the filter. Here are the main functions:
Structural Support: The primary function of the center tube is to provide structural support to the filter media. This ensures that the filter media maintains its shape and doesn't collapse under the pressure of the incoming air, which could otherwise hinder the filtration process.
Flow Path for Air: The center tube also serves as the path for the filtered air to flow out of the filter element. Once the air has passed through the filter media and contaminants have been trapped, the clean air flows through the center tube and into the air compressor.
Protection Against Pressure Surges: The center tube is usually made of a sturdy material like metal, which can withstand pressure surges. This is important because sudden changes in pressure could otherwise damage the filter media.
Enhances Filter Life: By providing support and protecting the filter media, the center tube indirectly helps to enhance the life of the filter element, ensuring that it can continue to effectively filter the air over a longer period of time.
So, the center tube is an integral part of the air filter element, contributing significantly to its functionality and effectiveness.
The working principle of an air compressor air filter element is a combination of physical and sometimes chemical processes. Here are the detailed steps:
Air Intake: The process starts when the air compressor draws in ambient air. This air often contains various contaminants such as dust, pollen, and other particulates.
Filtration: The contaminated air then enters the air filter element. The filter media, usually made of pleated paper, cotton, or synthetic fibers, serves to trap and hold these contaminants. The pleated design increases the surface area of the filter, allowing it to capture more particles and thus, clean a larger volume of air.
Air Flow: As the air passes through the filter media, the contaminants are trapped on the surface or within the fibers of the filter media. The clean air then flows through the center tube of the filter element.
Protection: The end caps and gasket of the filter element ensure that all air entering the compressor has passed through the filter media. They provide a seal to prevent unfiltered air from bypassing the filter media and entering the compressor directly.
Output: The now filtered air exits the filter element through the center tube and is directed into the air compressor. The air compressor then compresses the filtered air and sends it where it's needed, such as a pneumatic tool or an HVAC system.
Replacement: Over time, the filter media will become clogged with contaminants and will need to be replaced to maintain the efficiency and performance of the air compressor.
By filtering out harmful contaminants, the air compressor air filter element protects the compressor and its components, ensuring a longer service life and more efficient operation.
The air filter element plays a critical role in protecting the compressor and its components. Here's how:
Prevention of Contaminant Ingestion: The primary function of the air filter element is to prevent contaminants such as dust, pollen, and other particulates from entering the compressor. These contaminants can cause significant wear and tear on the compressor's internal components, reducing its efficiency and lifespan.
Maintaining Compressor Efficiency: By filtering out contaminants, the air filter element ensures that the air entering the compressor is clean. This helps maintain the compressor's efficiency, as dirty air can cause the compressor to work harder, leading to increased energy consumption and decreased performance.
Protection of Downstream Components: The air filter element not only protects the compressor itself, but also the downstream components that rely on the compressed air. These can include pneumatic tools, control systems, and other equipment. By ensuring that the compressed air is clean, the air filter element helps extend the lifespan of these components and maintain their performance.
Preventing Clogging: The air filter element can also prevent contaminants from clogging the compressor's air intake, which could otherwise restrict airflow and reduce the compressor's efficiency.
Reducing Maintenance Costs: By protecting the compressor and its components from damage, the air filter element can help reduce maintenance costs. Replacing a clogged or damaged air filter element is typically much less expensive than repairing or replacing damaged compressor components.
In summary, the air filter element is a crucial component that helps protect the compressor and its components, ensuring that they continue to operate efficiently and effectively.
The air filter element is designed to prevent clogging of the air intake in a few ways:
Filtration: The air filter element is made of a fibrous material that traps and holds particles from the air that passes through it. These particles can include dust, pollen, and other airborne contaminants that could potentially clog the air intake. By trapping these particles, the air filter element prevents them from reaching the air intake and causing a blockage.
Regular Replacement: Over time, the trapped particles can build up on the air filter element, reducing its effectiveness and potentially leading to a clog. To prevent this, it's important to replace the air filter element regularly. The frequency of replacement will depend on the specific conditions in which the compressor is used, but a general rule of thumb is to replace the air filter element every 3-6 months.
Proper Sizing: The size of the air filter element is also critical in preventing clogs. If the filter element is too small, it may not be able to handle the volume of air being drawn into the compressor, leading to a buildup of particles and potential clog. Conversely, if the filter element is too large, it may not fit properly in the air intake, allowing particles to bypass the filter and cause a clog. Therefore, it's important to use an air filter element that's appropriately sized for the specific compressor.
Pre-Filters: In some cases, a pre-filter may be used in addition to the main air filter element. This is a secondary filter that's designed to trap larger particles before they reach the main filter, helping to prevent clogs and extend the life of the main filter.
In summary, the air filter element prevents clogging of the air intake by trapping particles, being replaced regularly, being properly sized, and sometimes being used in conjunction with a pre-filter.
An air compressor air filter element plays a crucial role in the overall performance and longevity of an air compressor system. It is primarily tasked with purifying the air that enters the compressor. Let's take a detailed look at its composition and function:
Composition:
Filter Media: This is the heart of the air filter element. It's typically made from materials like paper, foam, or synthetic fibers. The media's job is to trap and hold airborne particles such as dust, pollen, and other contaminants, preventing them from entering the compressor.
Metal End Caps: These are typically found at the top and bottom of the filter element. They provide structure and stability to the filter, ensuring the media stays in place and the air flows through it properly.
Center Tube: This is a metal tube that runs through the middle of the filter element, providing support to the filter media and allowing clean air to flow through to the compressor.
Gasket: This is a rubber or silicone seal that ensures a tight fit between the filter element and the filter housing, preventing unfiltered air from bypassing the filter.
Function:
Protecting the Compressor: The primary function of the air filter element is to protect the compressor by preventing harmful contaminants from entering it. This reduces wear and tear on the compressor's internal components, extending its lifespan and maintaining its efficiency.
Maintaining Air Quality: By removing contaminants from the air, the filter element helps maintain the quality of the compressed air. This is important for applications that require clean air, such as painting or sandblasting.
Reducing Maintenance Costs: By preventing contaminants from entering the compressor, the air filter element reduces the need for maintenance and repairs, saving time and money in the long run.
Preventing Clogs: The air filter element also prevents contaminants from clogging the compressor's air intake, which could restrict airflow and reduce the compressor's efficiency.
In summary, the air compressor air filter element is a vital component that protects the compressor, maintains air quality, reduces maintenance costs, and prevents clogs. Its composition of filter media, metal end caps, a center tube, and a gasket enables it to effectively perform these functions.
The air compressor air filter element carries several advantages and strengths that make it an integral part of any air compressor system. Here are some of the primary benefits:
Improved Performance: The air filter element ensures that the air entering the compressor is clean, which can significantly enhance the compressor's performance. A clean air intake reduces the risk of internal damage and helps the compressor operate at peak efficiency.
Extended Lifespan: By preventing harmful contaminants from entering the compressor, the air filter element can extend the lifespan of the compressor. This can result in significant cost savings over the long term, as the need for repairs or replacements is reduced.
Enhanced Air Quality: The air filter element can remove a wide range of contaminants from the air, including dust, pollen, and other particles. This results in cleaner, higher-quality air output, which is particularly important in applications where air purity is crucial, such as in medical or food processing industries.
Cost-Efficient: Regularly replacing the air filter element is a relatively inexpensive maintenance task, especially when compared to the potential cost of repairing or replacing a damaged compressor. Additionally, a clean filter element can improve the compressor's efficiency, potentially leading to energy savings.
Versatility: Air filter elements come in a variety of sizes and materials, making them suitable for a wide range of applications. Whether the compressor is being used in a small home workshop or a large industrial facility, there's likely an air filter element that's the perfect fit.
Easy to Replace: Most air filter elements are designed to be easy to replace, requiring no special tools or technical skills. This means that maintaining the air quality of your compressor can be a simple and straightforward task.
Prevents Clogs: The air filter element plays a crucial role in preventing clogs in the compressor's air intake. This helps maintain consistent airflow and compressor efficiency.
In summary, the air compressor air filter element offers improved performance, extended equipment lifespan, enhanced air quality, cost efficiency, versatility, ease of replacement, and prevention of clogs. These advantages make it a key component in maintaining the optimal functioning of an air compressor system.
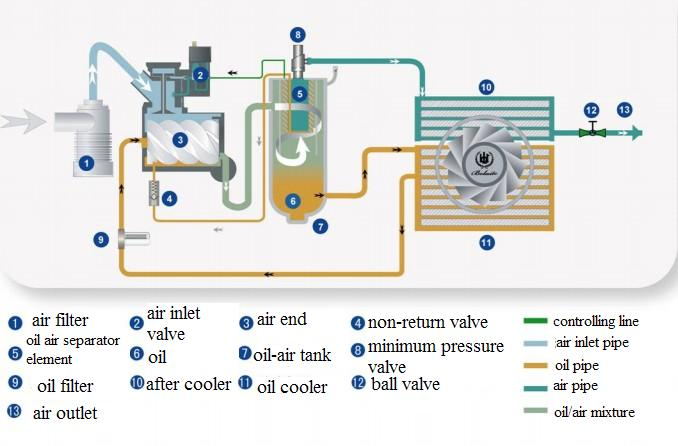
The technical parameters and specifications of an air compressor air filter element can vary greatly depending on the specific model and application. However, here are some general aspects that are typically considered:
Filter Media Material: The filter media is the material that actually traps the particles. It can be made from a variety of materials, including paper, cellulose, synthetic fibers, or a blend of materials. The choice of material can affect the filter's efficiency and lifespan.
Filtration Efficiency: This refers to the percentage of particles of a specific size that the filter is capable of removing from the air. For example, a filter with a 99% efficiency rating will remove 99% of particles of the specified size.
Micron Rating: This is a measure of the size of the particles that the filter can trap. It's usually expressed in microns. For example, a filter with a 10-micron rating can trap particles that are 10 microns or larger.
Flow Rate: This is the amount of air, usually measured in cubic feet per minute (CFM), that can pass through the filter. The filter should be able to handle the compressor's maximum airflow without causing a significant pressure drop.
Operating Temperature Range: This is the range of temperatures at which the filter can operate effectively. It's important that the filter is able to withstand the heat generated by the compressor.
Size and Dimensions: These are the physical measurements of the filter, including its length, width, and diameter. The filter needs to be the correct size to fit properly in the compressor's filter housing.
Service Life: This is the expected lifespan of the filter before it needs to be replaced. The service life can depend on a variety of factors, including the filter material, the operating conditions, and the level of contaminants in the air.
Pressure Drop: This is the reduction in air pressure that occurs as the air passes through the filter. A high pressure drop can reduce the compressor's efficiency, so it's important to choose a filter that minimizes pressure drop.
In summary, when considering the technical parameters and specifications of an air compressor air filter element, one should take into account the filter media material, filtration efficiency, micron rating, flow rate, operating temperature range, size and dimensions, service life, and pressure drop.
The air compressor air filter element is an essential component in a variety of industries due to its role in ensuring the efficiency and longevity of air compressor systems. Here are some of the key industries where it finds its applications:
Manufacturing: In manufacturing plants, air compressors are often used to power pneumatic tools and machinery. The air filter element ensures that the compressed air is free from contaminants, preventing damage to the tools and ensuring efficient operation.
Automotive: In the automotive industry, air compressors are used in a variety of applications, from painting cars to inflating tires. The air filter element helps ensure that the air used in these processes is clean and free from harmful particles.
Construction: On construction sites, air compressors power a variety of tools, from jackhammers to nail guns. The air filter element plays a crucial role in maintaining the efficiency and longevity of these tools.
Food and Beverage: In the food and beverage industry, air compressors are used for a variety of processes, including packaging, bottling, and even food processing. The air filter element ensures that the compressed air used in these processes does not contaminate the food or beverages.
Medical: In medical facilities, air compressors are used in a variety of applications, from powering surgical tools to providing clean air for patients. The air filter element is critical in ensuring that the air is clean and free from contaminants.
Energy: In the energy sector, air compressors are used in a variety of applications, from powering tools to operating control systems. The air filter element ensures that the compressed air is clean and efficient.
Agriculture: In agriculture, air compressors are often used to power tools and machinery, from crop sprayers to milking machines. The air filter element helps ensure the longevity and efficiency of these tools.
In summary, the air compressor air filter element is a crucial component in a wide range of industries, including manufacturing, automotive, construction, food and beverage, medical, energy, and agriculture. It plays a key role in ensuring the efficiency and longevity of air compressor systems, contributing to the overall productivity and success of these industries.
Installing and maintaining an air compressor air filter element is crucial for the efficient operation of the compressor. Here's a detailed guide on how to do so:
Installation:
Before you begin, ensure that the air compressor is switched off and disconnected from the power source to prevent any accidental startups.
Locate the filter housing on your air compressor. It's usually on the intake side of the compressor.
Open the filter housing. This usually involves unscrewing a cover or removing a latch.
Remove the old filter element from the housing. Be careful not to allow any debris to fall into the compressor intake.
Inspect the new filter element for any damage or defects before installation.
Install the new filter element into the housing. Make sure it fits snugly and is properly seated.
Replace the filter housing cover and secure it tightly.
Reconnect the power source and turn on the compressor to check the installation.
Maintenance:
Regular Inspection: Check the filter element regularly for any signs of wear or damage. A visual inspection can help detect any obvious issues, but keep in mind that not all problems are visible to the naked eye.
Cleaning: Some filter elements can be cleaned and reused. This usually involves removing the element and gently cleaning it with a soft brush or compressed air. Always follow the manufacturer's instructions when cleaning the filter element.
Replacement: Over time, the filter element will become clogged with particles and will need to be replaced. The frequency of replacement will depend on the operating conditions and the type of filter element. As a general rule, replace the filter element at least once a year, or more frequently if the compressor is used in a dusty environment.
Monitor Performance: Keep an eye on the compressor's performance. If you notice a drop in pressure or efficiency, it could be a sign that the filter element needs to be replaced.
Record Keeping: Keep a record of when the filter element was last replaced. This can help you establish a regular maintenance schedule.
In conclusion, the proper installation and maintenance of an air compressor air filter element can significantly enhance the performance and lifespan of your air compressor. Regular inspection, cleaning, replacement, performance monitoring, and record keeping are all key aspects of maintaining your air filter element.
The environmental sustainability and social impact of an air compressor air filter element are significant and multifaceted. Here are some key points to consider:
Environmental Sustainability:
Air Quality Improvement: Air compressor air filter elements play a crucial role in improving air quality by filtering out harmful pollutants and particulates. This not only protects the machinery but also contributes to cleaner air in the surrounding environment.
Energy Efficiency: Efficient air filters can reduce the energy consumption of an air compressor by reducing the pressure drop and allowing the compressor to operate more efficiently. This can contribute to lower carbon emissions and a reduced environmental footprint.
Waste Reduction: Some air filters are designed to be cleaned and reused, reducing the need for frequent replacements and minimizing waste. Additionally, some filters are made from recyclable materials, further contributing to waste reduction.
Social Impact:
Health Protection: By improving air quality, air compressor air filter elements can help protect the health of workers in industries where air compressors are used. This can reduce the risk of respiratory issues and other health problems associated with exposure to airborne pollutants.
Productivity Improvement: A well-maintained air compressor with an efficient filter can improve productivity by reducing downtime and maintenance costs. This can have a positive impact on businesses and the economy as a whole.
Job Creation: The manufacturing, installation, and maintenance of air compressor air filter elements can contribute to job creation in these sectors. This can have a positive social impact by providing employment opportunities.
In conclusion, the environmental sustainability and social impact of an air compressor air filter element are significant. They contribute to improved air quality, energy efficiency, waste reduction, health protection, increased productivity, and job creation. These benefits highlight the importance of these components in our industrial and societal systems.