The filter operates on a unique suction mechanism that ensures the tThe Sucking Type Self-Cleaning Filter is a remarkable innovation in the field of fluid purification and filtration. This product is designed to provide high efficiency in filtering various types of fluids, including water and oil, with a self-cleaning feature that enhances its usability and durability.horough removal of impurities from the fluid. The suction process is automated, thereby eliminating the need for manual cleaning and reducing maintenance requirements. The filter's self-cleaning feature is activated when the impurity accumulation reaches a certain level, ensuring that the filter's performance remains optimal at all times.
The product is built with high-quality materials that offer excellent resistance to corrosion and wear, thereby ensuring a long lifespan and consistent performance. Its compact design makes it easy to install in various systems and applications, making it a versatile solution for fluid filtration needs.
In terms of efficiency, the Sucking Type Self-Cleaning Filter excels by providing high filtration accuracy. It effectively removes both large and fine impurities, ensuring that the fluid remains clean and safe for use. This makes it an ideal choice for industries that require high purity levels in their processes.
In conclusion, the Sucking Type Self-Cleaning Filter is a reliable, efficient, and durable solution for fluid filtration. Its self-cleaning feature, high filtration accuracy, and robust construction make it a valuable addition to any system where fluid purity is of utmost importance.
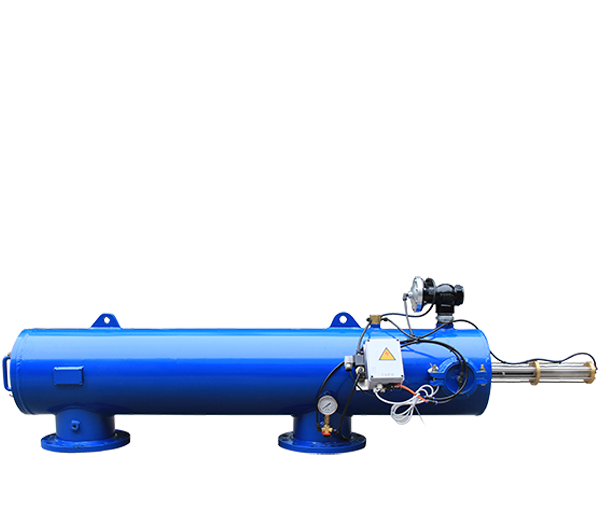
The Sucking Type Self-Cleaning Filter operates on an advanced principle that combines suction and backwashing to ensure efficient filtration and self-cleaning. Here's a detailed explanation of its working mechanism.
Filtration Phase: When the fluid enters the filter, it is directed towards the inner side of the filter screen. The impurities in the fluid are trapped on the inner surface of the filter screen, while the clean fluid passes through the filter screen and out of the filter outlet.
Pressure Differential Detection and Backwash initiation: Over time, as the impurities accumulate on the inner surface of the filter screen, a pressure differential is created across the screen. Once this pressure differential reaches a preset value, the backwash cycle is automatically initiated. Alternatively, the backwash cycle can also be initiated at preset time intervals.
Backwash Phase: During the backwash phase, the backwash valve is opened. The pressure differential between the internal pressure of the filter and the atmospheric pressure drives a portion of the fluid in reverse through the filter screen. This backwash fluid is directed through a suction scanner that is rotated by a motor. The suction scanner has multiple nozzles that create a high-velocity backwash flow, effectively sucking off the impurities from the inner surface of the filter screen.
Discharge Phase: The impurities removed from the filter screen are discharged out of the filter through the backwash valve. The backwash process is carried out during normal filtration, ensuring uninterrupted operation of the filter.
End of Backwash Cycle: Once the backwash cycle is completed, the backwash valve is closed, and the filter returns to normal filtration mode.
This innovative working principle of the Sucking Type Self-Cleaning Filter ensures high filtration efficiency and reduces maintenance requirements by automating the cleaning process. The filter can operate continuously, providing clean and safe fluid for various applications.
Pressure differential detection, also known as differential pressure sensing, is a crucial component in the operation of many filtration systems, including the Sucking Type Self-Cleaning Filter. Here's a detailed explanation of how it works:
The principle of pressure differential detection is based on measuring the difference in pressure between two points in a system. In the context of a filtration system, these two points are typically the inlet and outlet of the filter.
When the filter is clean, the pressure difference between the inlet and outlet is relatively small. This is because the fluid can flow freely through the filter screen, with minimal resistance to its flow.
As the filter screen accumulates impurities over time, the flow of fluid through the screen becomes more restricted. This increases the resistance to flow, which in turn increases the pressure at the inlet of the filter. Conversely, the pressure at the outlet of the filter decreases due to the reduced fluid flow.
This creates a pressure differential across the filter screen. The pressure differential can be detected using a pressure differential sensor, which is typically a part of the filter system. The sensor can be calibrated to trigger a signal when the pressure differential reaches a certain threshold. This signal can then be used to initiate the backwash cycle of the filter.
In essence, pressure differential detection works as an indicator of the filter's cleanliness. It provides a reliable and automated method to determine when the filter needs cleaning, thereby enhancing the efficiency and longevity of the filter system.
The Sucking Type Self-Cleaning Filter is a complex system made up of several integral components, each serving a specific function to ensure efficient filtration and self-cleaning. Here's a detailed breakdown of its structure and the role of each component:
Filter Housing: This is the main body of the filter where the filtration and backwash processes occur. It is typically made of robust materials like stainless steel to withstand high pressure and corrosive fluids.
Filter Screen: This is the core component where the actual filtration takes place. The fluid flows from the inside to the outside of the filter screen, leaving the impurities trapped on its inner surface.
Inlet and Outlet Ports: These are the entry and exit points for the fluid. The inlet port directs the fluid towards the inner side of the filter screen, while the clean fluid exits the filter through the outlet port.
Backwash Valve: This valve opens to initiate the backwash phase. It allows a portion of the fluid to flow in reverse through the filter screen, removing the impurities from its surface.
Suction Scanner: This is a key component in the self-cleaning process. The scanner, equipped with multiple nozzles, moves in a spiral path along the inner surface of the filter screen during the backwash phase. The high-velocity backwash flow through the nozzles effectively sucks off the accumulated impurities.
Motor: This powers the movement of the suction scanner during the backwash phase. It ensures the scanner covers the entire inner surface of the filter screen.
Pressure Differential Sensor: This sensor detects the pressure differential across the filter screen. When the pressure differential reaches a preset value, indicating the filter screen is sufficiently blocked with impurities, the sensor triggers the start of the backwash cycle.
Controller: This is the 'brain' of the filter. It receives the signal from the pressure differential sensor and controls the opening and closing of the backwash valve, as well as the operation of the motor. It ensures the filter operates in a fully automated manner, maximizing efficiency and minimizing manual intervention.
Through the coordinated operation of these components, the Sucking Type Self-Cleaning Filter achieves high filtration efficiency and automated self-cleaning, ensuring a continuous supply of clean fluid for various applications.
Ensuring the stability of a filter during operation involves several key steps:
Regular Maintenance: Regular inspection and maintenance of the filter components are crucial. This includes checking for leaks, assessing the condition of the filter screen, and ensuring the proper functioning of the backwash valve, suction scanner, motor, and pressure differential sensor.
Proper Installation: The filter should be installed correctly, following the manufacturer's guidelines. Improper installation can lead to operational instability and reduced filtration efficiency.
Monitoring Pressure Differential: The pressure differential across the filter screen should be monitored closely. If the pressure differential becomes too high, it could indicate a blockage in the filter screen, which could destabilize the filter operation.
Automated Control: Utilizing an automated control system can greatly enhance the stability of the filter. The controller can automatically initiate the backwash cycle based on the pressure differential, ensuring timely cleaning of the filter screen and preventing excessive pressure buildup.
Using Quality Fluids: The quality of the fluid being filtered can also affect the stability of the filter. Fluids with high levels of impurities can clog the filter screen quickly, leading to instability. Therefore, pre-treatment of the fluid to remove large impurities can be beneficial.
Appropriate Sizing: The filter should be appropriately sized for its intended application. A filter that is too small may become overloaded, leading to instability, while a filter that is too large may not operate efficiently.
By following these steps, the stability of a filter during operation can be ensured, leading to efficient filtration and a longer lifespan for the filter.
The Sucking Type Self-Cleaning Filter comes with a plethora of advantages and strengths that make it a preferred choice in many industries. Here's a detailed overview of its benefits:
Self-Cleaning Feature: The most prominent advantage of this filter is its self-cleaning capability. The automatic backwash cycle ensures that the filter remains clean without any manual intervention, saving time and reducing maintenance costs.
High Filtration Efficiency: The filter screen effectively traps impurities, providing a high level of filtration efficiency. This ensures the continuous supply of clean fluid, which is essential for maintaining the quality of processes in industries like food and beverage, pharmaceuticals, and water treatment.
Robust and Durable: Typically made from robust materials like stainless steel, these filters are designed to withstand high pressure and corrosive fluids, ensuring longevity and reliable performance.
Automated Operation: The integrated controller automates the operation of the filter, initiating the backwash cycle when the pressure differential reaches a preset value. This eliminates the need for constant monitoring and manual operation, further enhancing efficiency.
Versatility: These filters can handle a wide range of fluids, from water to viscous liquids, making them versatile for various industrial applications.
Energy Efficient: The backwash process is triggered based on the pressure differential, which means it only occurs when necessary. This makes the filter energy efficient as it doesn't waste energy on unnecessary cleaning cycles.
Space-Saving Design: Compared to traditional filters that require additional equipment for cleaning, the Sucking Type Self-Cleaning Filter is compact and space-efficient. It incorporates the cleaning mechanism within the filter housing, saving valuable floor space.
Reduced Downtime: As the filter continues to operate during the backwash cycle, there's no need to shut down the system for cleaning. This reduces downtime and enhances productivity.
In conclusion, the Sucking Type Self-Cleaning Filter is a technologically advanced, efficient, and reliable solution that offers numerous advantages, making it an excellent choice for various industrial filtration needs.
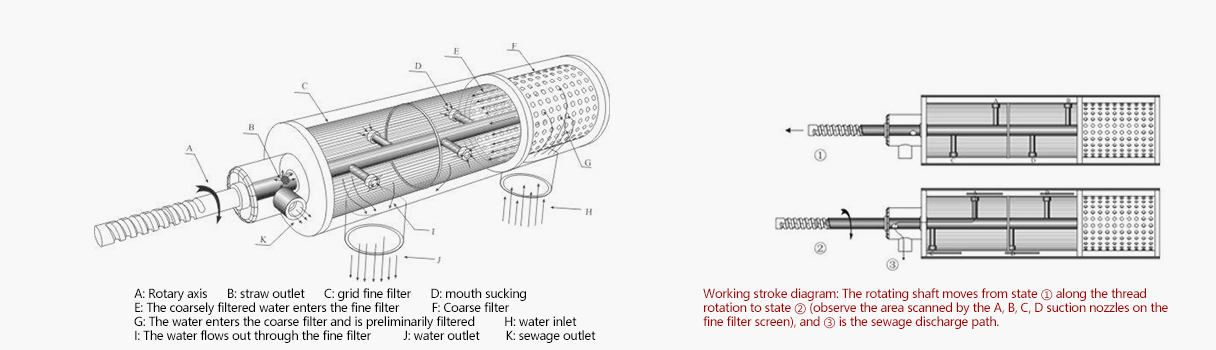
The Sucking Type Self-Cleaning Filter is a sophisticated piece of equipment with a variety of technical specifications and sizes. Here are some general technical parameters and specifications:
Filtration Accuracy: The filtration accuracy of these filters can range from 50 microns to 800 microns, catering to different filtration requirements.
Flow Rate: Depending on the size and design, the flow rate can vary greatly. Some models can handle flow rates up to 1000 cubic meters per hour or even higher.
Control Power Supply: The control power supply is typically 220V/50Hz, but this can vary based on the specific model and regional standards.
Automatic Drain Valve: This feature ensures automatic discharge of the collected impurities during the backwash cycle.
Electric Motor: The electric motor powers the suction scanner during the backwash cycle, ensuring efficient cleaning of the filter screen.
Pressure Indicator: This provides real-time monitoring of the pressure differential across the filter screen, which is a key parameter for initiating the backwash cycle.
Water Inlet and Outlet: The size and orientation of the water inlet and outlet can vary based on the specific model and installation requirements.
Screen and Suction Nozzle: The filter screen traps the impurities, and the suction nozzle cleans the screen during the backwash cycle.
Pipeline Diameter: The pipeline diameter can range from 8 inches to 36 inches, catering to different flow rate requirements.
Housing Material: The filter housing is typically made from robust materials like stainless steel to withstand high pressure and corrosive fluids.
These are general specifications, and the exact parameters can vary based on the specific model and manufacturer. It's always recommended to refer to the manufacturer's data sheet for precise specifications and to ensure the filter meets your specific requirements.
The Sucking Type Self-Cleaning Filter is a versatile piece of equipment that finds applications in a wide range of industries due to its efficient filtration capabilities and self-cleaning feature. Here are some key industries where this filter is commonly used:
Water Treatment: This filter is extensively used in water treatment plants for removing impurities from raw water. It ensures the supply of clean water for various purposes like drinking, irrigation, and industrial processes.
Food & Beverage: In the food and beverage industry, this filter is used for removing impurities from water used in food processing, brewing, and beverage production. It helps maintain the quality and safety of food products.
Pharmaceuticals: In the pharmaceutical industry, it is used for purifying water used in the production of medicines and other pharmaceutical products. It helps meet the stringent cleanliness standards of the industry.
Petrochemicals: This filter is used in petrochemical plants for filtering raw materials and process fluids. It helps prevent blockages in the process equipment and ensures smooth operation.
Power Generation: In power plants, this filter is used for filtering cooling water and boiler feed water. It helps prevent scale formation and corrosion in the heat exchangers and boilers.
Pulp & Paper: In the pulp and paper industry, it is used for filtering process water and pulp slurries. It helps improve the quality of the paper and reduces downtime due to clogged nozzles and screens.
Irrigation: This filter is used in irrigation systems for removing impurities from the irrigation water. It helps prevent blockages in the irrigation nozzles and ensures efficient water distribution.
Mining: In the mining industry, it is used for filtering process fluids and wastewater. It helps protect the process equipment and ensures compliance with environmental regulations.
In conclusion, the Sucking Type Self-Cleaning Filter is a highly versatile piece of equipment that plays a crucial role in various industries, ensuring the supply of clean and safe water and process fluids.
The Sucking Type Self-Cleaning Filter is a sophisticated piece of equipment that requires proper installation and maintenance to ensure its efficient operation and longevity. Here's a detailed guide on its installation and maintenance:
Installation:
Location: Choose a location that allows easy access for operation and maintenance. Ensure there's enough space for the filter and the associated piping.
Orientation: Install the filter in the correct orientation as indicated by the manufacturer. The direction of flow should match the arrow on the filter body.
Piping: Connect the filter to the system using suitable piping. Ensure the piping is properly supported to avoid stress on the filter connections.
Electrical Connections: Connect the control system to the power supply as per the manufacturer's instructions. Ensure the power supply matches the specifications of the control system.
Initial Startup: Before the initial startup, flush the system to remove any debris. Then, fill the system gradually to avoid sudden pressure surges.
Maintenance:
Regular Inspection: Regularly inspect the filter for any signs of wear or damage. Pay attention to the pressure differential indicator as a sudden increase may indicate a blockage.
Backwash Cycle: Ensure the backwash cycle is functioning properly. If the filter screen is not getting cleaned adequately, check the backwash valve and the suction scanner for any issues.
Seals and Gaskets: Check the seals and gaskets regularly for any signs of leakage. Replace them if necessary.
Control System: Regularly inspect the control system for any issues. Ensure the power supply is stable and the control settings are correct.
Scheduled Maintenance: Follow the manufacturer's recommendations for scheduled maintenance. This may include tasks like cleaning the filter housing, checking the motor, and replacing worn-out parts.
Remember, improper installation or lack of maintenance can lead to reduced performance and premature failure of the filter. Always follow the manufacturer's instructions and consult with a professional if you're unsure about any aspect of the installation or maintenance.